www.industrieweb.fr
02
'20
Written on Modified on
Analog Devices News
Avec la maintenance prédictive, les usines entrent dans l’ère du « wearable »
Dans le contexte de l’Industrie 4.0, la maintenance prédictive (Condition-based Monitoring — CbM) correspond aux bracelets portables qu’utilisent les amateurs de fitness. L’explosion de la connectivité permet d’observer le monde physique sous de nouvelles perspectives et de découvrir des processus physiques en action dans leurs moindres détails et en temps réel.
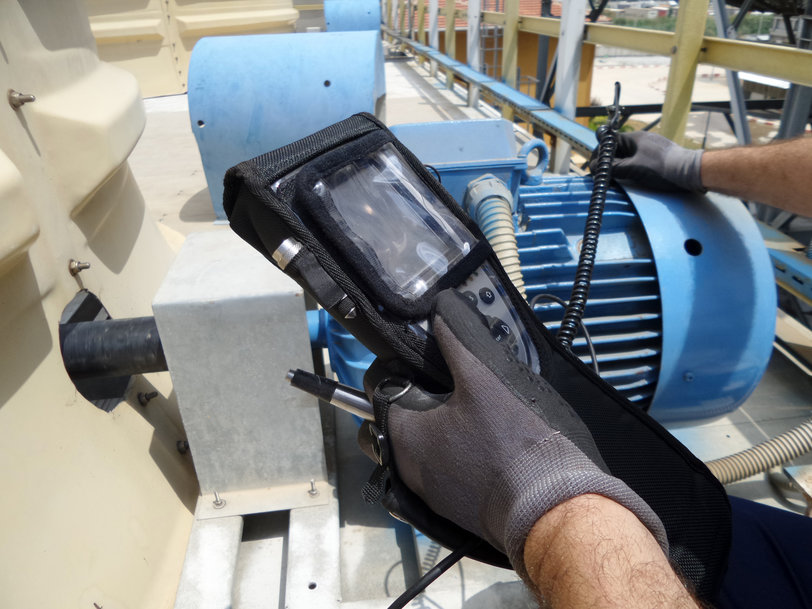
Par Stuart Servis, ingénieur d’applications, Analog Devices
Dans le secteur industriel, le vieillissement des équipements et des machines est un processus majeur, qu’il est très important de comprendre et ce, tous domaines d’activité confondus, des hydrocarbures à la production d’énergie éolienne en passant par le contrôle des processus industriels, où les dépenses d’infrastructure et d’équipements sont élevées et les indisponibilités opérationnelles particulièrement onéreuses.
Les indisponibilités non planifiées peuvent se chiffrer en milliers de dollars par heure. Selon une étude réalisée en 2017, les entreprises ont déclaré un coût moyen de 2 millions de dollars dû aux seules indisponibilités opérationnelles. Cette étude montre également que les indisponibilités non planifiées sont nettement plus coûteuses que les interventions de maintenance planifiées, dans la mesure où une machine doit être débranchée pendant toute la période qui englobe la phase de diagnostic, la commande des pièces et l’exécution des réparations.
Le fonctionnement continu de machines dans les limites de leurs spécifications, ainsi que leur cycle de vie prévu, sont influencés par des variables telles que la durée de service, la variation des charges et des environnements opérationnels, ainsi que l’apparition d’événements provoquant des dommages. Dans ce contexte, la maintenance prédictive a pour vocation de quantifier ces impacts, d’activer des alertes lorsqu’une attention immédiate est requise, et de prévoir à quel moment précis une intervention doit avoir lieu.
Chaque machine est particulière et vieillit selon des critères qui lui sont propres, même si ce processus est, de manière générale, aussi lent qu’imperceptible. Et tant que personne n’en cherche pas la trace, de subtils changements surviennent au fil du temps et le vieillissement se poursuit sans faire de vagues. Jusqu’au moment où une défaillance, potentiellement catastrophique, indique que la machine est hors service et qu’une réparation est nécessaire. Aujourd’hui, les utilisateurs veulent être alertés le plus rapidement possible de l’imminence d’une panne afin de pouvoir anticiper l’indisponibilité de la machine. Ils sont également à l’affût d’indicateurs de changement pouvant affecter la qualité du produit final, qu’il s’agisse de tôle ou de papier.
La nécessité de disposer conjointement de signes de plus en plus précoces de l’usure d’une machine et d’informations concernant la qualité des articles qu’elle produit implique l’utilisation de moyens de détection encore plus sensibles et encore plus omniprésents. Les techniques de mesure varient elles aussi de façon croissante, et des mesures acoustiques, du courant moteur et des tensions viennent s’ajouter aux relevés classiques de température et de vibrations. Ces systèmes de mesure sont associés pour fournir une vision plus globale de l’état des équipements avec à la clé une hausse considérable du nombre de voies de mesure dans chaque machine. Les mesures individuelles doivent souvent être synchronisées avec précision pour afficher les relations qui existent, par exemple entre les vibrations mesurées sur les axes x, y et z. Un tel degré de synchronisation accroît bien évidemment la complexité des systèmes.
Face à la prolifération des nœuds et des modes de mesure, les méthodes d’inspection et de relevé manuelles reposant sur des ressources elles aussi manuelles sont à la peine. Les systèmes doivent être déployés d’un bout à l’autre des usines ou dans un site distant en s’appuyant sur le câblage existant ou un réseau sans fil en utilisant des systèmes robustes et sécurisés. Pour s’intégrer à ces environnements, les volumineux et onéreux capteurs et agrégateurs doivent céder la place à des produits plus discrets, moins coûteux et plus sobres.
De nouvelles solutions de précision interviennent au niveau des composants et des sous-systèmes. Grâce à leur niveau d’intégration élevé, les constructeurs de systèmes peuvent faire en sorte que cet avenir qui se distinguera par un haut degré de détection soit, dès aujourd’hui, une réalité.
Acquisition de données
Pour obtenir des indications relatives à l’usure d’une machine de façon précoce, des dons de voyance sont pratiquement nécessaires ! Dans le domaine de l’analyse et de la maintenance prédictive, c’est toutefois possible en scrutant les plus infimes traces de changement qui touchent le système, que ce soit au niveau de la température, des vibrations ou de la signature acoustique. Ces imperceptibles variations peuvent être détectées à l’aide de capteurs et de systèmes d’acquisition de données conçus pour identifier sans erreur les moindres changements survenant aux plus bas niveaux de détection et ce, même lorsque les vibrations ou les températures sont élevées. Cette approche requiert l’utilisation de chaînes de signal se caractérisant par une dynamique extrêmement élevée, en d’autres termes de systèmes dont le niveau de bruit est extrêmement faible, tout en étant aptes à traiter d’importantes variations du signal. Par exemple, pour détecter un début d’usure sur une pompe à pistons plongeurs, le changement peut être inférieur à 1/10e de millimètre au niveau de la position en fin de course du piston, ce dernier se déplaçant sur une distance pouvant atteindre 300 mm. Pour qu’un tel changement puisse être remarqué, le bruit du système doit être inférieur d’au moins un facteur
10, ce qui pousse le niveau de détection à 1:300 000, soit 109 dB, et nécessite l’utilisation de systèmes d’acquisition de données de 18 bits ou plus.
Un autre aspect doit être pris en compte, à savoir la nécessité de « sortir » de la bande passante d’intérêt. Les essieux moteurs et un grand nombre de systèmes à engrenages présentent des vibrations caractéristiques à des fréquences relativement basses et proches de la vitesse de rotation de l’essieu ou de faibles multiples de celle-ci. Or, d’autres composants du système affichent des caractéristiques fréquentielles supérieures. Pour détecter les changements dans l’usure des composants qui fonctionnent à de plus hautes fréquences — roulements à billes ou roulements lubrifiés, par exemple —, la détection doit pouvoir atteindre une haute résolution et une forte dynamique au-delà de 10 kHz et jusqu’à parfois 80 kHz.
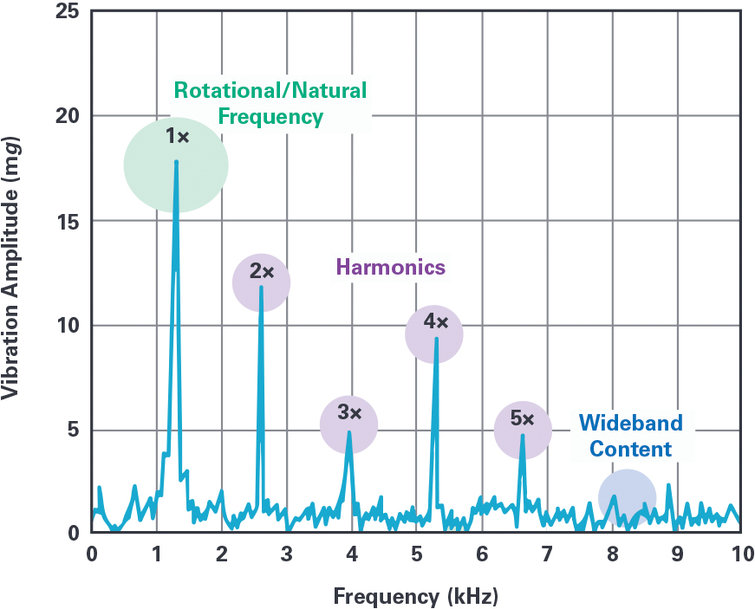
Signature vibratoire typique
Les spécifications du système de détection doivent inclure une dynamique élevée (DR — Dynamic Range), ainsi qu’un taux de distorsion harmonique (THD — Total Harmonic Distorsion) extrêmement faible afin de résoudre ces caractéristiques du domaine fréquentiel dans le profil vibratoire du système. Dans ce type de systèmes, les tout derniers convertisseurs sigma-delta (Σ-Δ) de précision large bande sont utilisés pour exécuter les tâches de conversion analogique/numérique. Certains convertisseurs extrêmement précis sont capables de répondre aux exigences clés de ces systèmes. Ils sont spécifiés pour une dynamique et un THD élevés (respectivement de +108 dB et -120 dB typiques), obtenus dans une bande passante comprise entre le continu et au moins 80 kHz ; en outre, ils se distinguent par des fonctionnalités d’utilisation aisée telles que des tampons de précharge sur les entrées analogiques, des filtres numériques intégrés et une synchronisation entre différents composants pour l’adaptation de phase multivoies qui en font des composants clés pour réaliser les systèmes d’acquisition de données les mieux adaptés aux tâches de maintenance prédictive.
Les fonctions d’adaptation de la consommation d’énergie (power scaling) permettent de régler un équipement donné par rapport à des plafonds de puissance spécifiques, un compromis pouvant être établi entre la dynamique ou la largeur de bande et la consommation totale. De plus, le fait d’assurer un haut niveau de précision au continu, ainsi qu’à des largeurs de bande supérieures, permet aux voies d’entrée de répondre aux exigences de détection de température ou de déformations au continu et en bande étroite dans la même plateforme, ce qui simplifie l’architecture et la complexité du système de maintenance prédictive, une plateforme unique convenant aux différents types de capteurs CbM.
Échantillonnage simultané
Dans les systèmes de maintenance prédictive, la technique d’échantillonnage simultané est utilisée pour préserver la relation de phase entre les ensembles de données du domaine temporel. Par exemple, la disposition de deux capteurs de vibrations selon des axes orthogonaux permet de détecter la direction et l’amplitude des phaseurs de vibrations. Dans l’idéal, les retards de phase sur le chemin d’entrée de chaque capteur doivent être correctement adaptés et suivre l’évolution de la température.
Les convertisseurs analogique/numérique à approximations successives (SAR) conviennent particulièrement aux systèmes de maintenance prédictive qui nécessitent une flexibilité de conception encore plus élevée pour répondre à leurs exigences sur le plan de la fréquence d’échantillonnage, de la largeur de bande ou de l’adaptation de la puissance. Ces composants se caractérisent également par une dynamique et un THD élevés à des fréquences d’échantillonnage pouvant atteindre 2 Méch/s ; par ailleurs, ils intègrent des fonctions d’utilisation aisée qui réduisent la consommation d’énergie sur la chaîne du signal en la simplifiant, et augmentent la densité de voies. Les convertisseurs disposant de modes d’impédance d’entrée plus élevés élargissent la gamme d’amplificateurs de précision basse consommation pouvant commander directement ces convertisseurs analogique/numérique tout en obtenant des performances optimales.
Pour permettre aux fabricants de systèmes d’atteindre des densités de voies aussi élevées que possible dans des nœuds d’acquisition plus compacts ou distribués, ainsi que pour réduire leurs délais de lancement sur le marché, Analog Devices propose les produits de traitement de la chaîne du signal de la série µModule® dont le niveau d’intégration est plus élevé que jamais.
Ces produits μModule combinent des composants clés utilisés de façon courante dans des chaînes de signal d’acquisition de données au format compact de type circuit intégré.
L’approche μModule permet au concepteur de transférer vers le système les tâches de sélection, d’optimisation et de disposition des composants analogiques et à signal mixte, et ainsi de raccourcir les délais de conception et de limiter les interventions de maintenance sur le système, tout en accélérant la mise sur le marché. Montés sur de minuscules boîtiers, les composants μModule conviennent aussi bien aux systèmes de maintenance prédictive compacts et distribués comptant un nombre de voies réduit qu’aux systèmes en rack dont le nombre de voies est plus élevé.
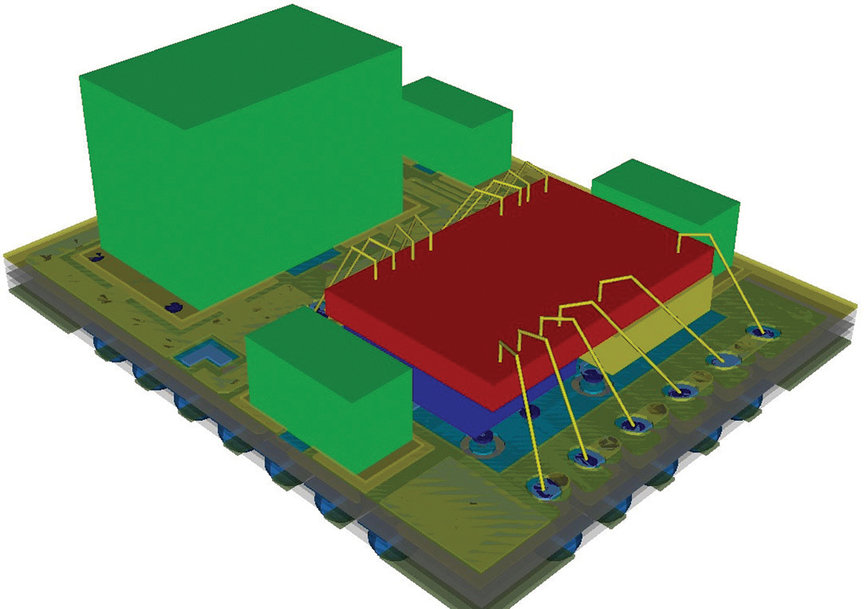
Rendu 3D d’un ensemble µModule
Capteurs
La conjugaison d’une dynamique élevée, d’une bande passante plus large, d’un meilleur rendement énergétique et de densités de voies supérieures dans la partie acquisition de données de la chaîne du signal permet de relever une partie seulement du défi de conception d’un système de maintenance prédictive. Volumineux, encombrants et coûteux, les capteurs de vibrations piézoélectriques classiques à électronique intégrée IEPE (Integrated Electronics PiezoElectric) fonctionnent généralement sous des tensions relativement supérieures à celle du système d’acquisition de données. Les capteurs piézoélectriques couramment utilisés sont alimentés sous une tension unique de -24 V, consommant plus de 2 mA, et sont logés dans des boîtiers métalliques lourds.
L’alimentation des capteurs étant généralement délivrée par le module d’acquisition de données, l’augmentation de la densité de voies dans le boîtier (box) soulève un double problème de densité de puissance et de densité de composants. De plus, outre la nécessité de disposer de nœuds d’acquisition sans fil alimentés par des batteries, notre capteur de vibrations piézoélectrique ne répond plus aux exigences de ces chaînes de signal.
Les capteurs de vibrations et inertiels de type MEMS (microsystèmes électromécaniques) permettent à présent de répondre aux exigences de ces systèmes. Les composants MEMS large bande les plus récents affichent des performances de bruit et de bande passante qui conviennent idéalement aux applications de maintenance prédictive. De plus, ils atteignent le degré de performances requis dans de minuscules boîtiers standard pour montage en surface (CMS) avec des niveaux de consommation 20 fois inférieurs à ceux de capteurs IEPE comparables. Les faibles dimensions et le profil de consommation des capteurs MEMS permettent de développer de très petits systèmes multiaxiaux alimentés par batterie et capables de surveiller de façon permanente et constante l’état d’un système.
Puissance et connectivité
Détecter le niveau de température, de vibrations ou de bruit d’une machine et convertir les données relevées en informations numériques forment une partie essentielle de la surveillance, même si ces détails ne donnent qu’une image incomplète de la situation. Lors de la réalisation d’un système de maintenance prédictive, il est important d’accorder une attention particulière aux différents composants analogiques, numériques et à signal mixte qui seront utilisés. Pour atteindre un faible niveau de bruit dans la chaîne d’acquisition des données, il est non seulement nécessaire d’employer des convertisseurs analogique/numérique et des capteurs à faible bruit, mais également une alimentation à faible niveau de bruit. Et pour minimiser le niveau de consommation du système, on emploiera également des composants de puissance capables d’extraire efficacement l’énergie de la batterie ou du câblage de terrain sans ajouter à la complexité du design.
Les exigences de connectivité varient en fonction de l’environnement applicatif. De nombreuses installations industrielles sont déjà dotées d’un vaste réseau de câblage utilisé pour le contrôle des processus, ou d’une infrastructure de détection environnementale —par exemple, pour relever la température. Il est toutefois possible qu’une partie significative de l’infrastructure en place ne soit pas en mesure de gérer les importantes quantités de données brutes ni de supporter les débits de transmission de données qu’impose une maintenance prédictive à grande échelle.
L’une des approches existantes consiste à améliorer les capacités du câblage de terrain en ajoutant des données supplémentaires, mais sans affecter les fonctions existantes. Par exemple, la technologie HART® (Highway Addressable Remote Transducer) permet d’ajouter des informations de diagnostic sous forme numérique en plus de l’interface analogique de 4 à 20 mA. De même, l’Ethernet industriel ajoute déterminisme et contrôle en temps réel à des infrastructures dotées d’un câblage Ethernet, ce qui permet d’obtenir une latence connue dans les applications de contrôle, ainsi qu’une bande passante plus large là où des données vibratoires ou FFT (Fast Fourier Transform) sont requises, tout en autorisant plusieurs nœuds sur chaque liaison.
Il est également possible de transférer les informations en mode sans fil. Dans les environnements industriels, une connectivité sans fil à la fois robuste et sécurisée est nécessaire. Les produits radio maillés intelligents les plus récents, c’est-à-dire des puces sans fil et des modules pour cartes électroniques précertifiés, permettent de communiquer en consommant peu d’énergie et avec une fiabilité des données supérieure à 99,999 %, même dans des environnements RF difficiles et sujets à de constantes fluctuations. Dans le cas de la maintenance prédictive, cette solution garantit que les défauts ou les événements transitoires seront communiqués au système hôte et qu’ils pourront être traités dans les plus brefs délais.
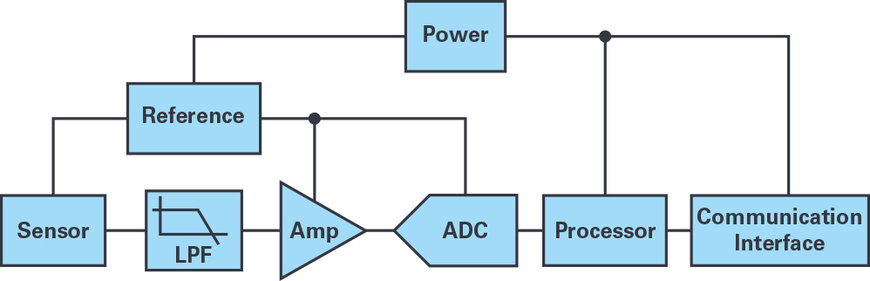
Synoptique des sous-blocs d’une chaîne de signal d’acquisition de données de précision
L’avenir de la maintenance prédictive CbM
La maintenance prédictive (Condition-based Monitoring) est une approche incontournable pour les secteurs qui nécessitent des investissements de grande valeur tels que l’énergie, le pétrole ou le gaz, et où les temps d’arrêt non planifiés ont des répercussions directes sur les coûts de production. Elle revêt également une importance croissante dans les usines où elle peut être utilisée comme une solution proactive pour assurer la maintenance des machines, mais également pour vérifier que le niveau de qualité des produits fabriqués par ces machines est homogène au quotidien. À mesure que la valeur de ces possibilités de surveillance apparaîtra plus clairement, cette technologie quittera le pré carré des éoliennes ou des papeteries pour s’imposer dans un nombre croissant de machines — que ce soit à bord des trains, des avions et des automobiles — pour à terme équiper les machines à laver et des appareils de moindres dimensions.
Les fabricants de composants système intégreront le capteur, voire l’ensemble de la chaîne de détection, à l’intérieur du composant. Les moteurs seront dotés de capteurs de vibrations et de courant, et il en sera de même pour les roulements et les boîtes de vitesse. Des nœuds autonomes seront connectés à nos terminaux mobiles. Un capteur monté sur la porte du garage vous avertira que votre voiture risque d’être enfermée à l’intérieur !
Pour répondre aux besoins croissants de détection dans ces différents scénarios, les fabricants d’équipements devront adopter une approche de type plateforme, où un ensemble réduit de plateformes permet de répondre à un ensemble de besoins variés. Les voies de mesure devront traiter différents types de capteurs, de sorte que les équipements montés en rack pourront être réaffectés à différentes combinaisons de capteurs. En ce qui concerne les équipements de plus petites dimensions, il devra être possible d’adapter les systèmes à différents profils de puissance pour qu’un même nœud de surveillance puisse être utilisé dans une machine à laver comme dans un outil alimenté par batterie.
Conclusion
La maintenance prédictive a pour vocation d’évaluer l’état de santé d’une machine en détectant divers paramètres quantifiables. L’augmentation de la précision et de la sensibilité de ces mesures, ainsi que la réduction des dimensions, du poids et de la consommation d’énergie de l’équipement utilisé, permettent aux responsables d’usine de déployer cette technologie dans l’ensemble de leur site.
Les usines disposent désormais d’un « moniteur de santé », équivalent industriel des bracelets de fitness, qui permet de mieux comprendre le fonctionnement de leurs activités. En étant informés des changements infimes qui affectent le fonctionnement de leur parc de machines, les directeurs d’usine peuvent prendre plus rapidement des décisions judicieuses.
Planifier la maintenance à l’avance, et uniquement pour les machines qui l’exigent vraiment, permettra de réduire sensiblement les dépenses de maintenance et, à terme, d’éliminer les coûts liés aux techniciens de garde et d’astreinte.
Les dépenses d’infrastructure et d’équipement peuvent être réduites en améliorant le contrôle des usines. La détection et le remplacement anticipés des composants usés protègent l’état de santé général des machines, tandis qu’une surveillance plus étroite limite les risques de défaillance, voire de catastrophe. En outre, la durée de vie des équipements peut être prolongée grâce au soin apporté à la gestion des machines jusqu’à leur fin de vie.
Il sera par ailleurs possible d’abaisser le coût de production des produits fabriqués dans ce type d’usine. La connaissance de l’état de santé des machines permet en effet de contrôler les tolérances sur les machines. La qualité des produits gagnera en cohérence d’un lot de production à l’autre et les cas de machines fonctionnant « hors limites » ou d’arrêts intempestifs seront moins fréquents, réduisant ainsi les retouches et le gaspillage.
Comment Analog Devices contribue à résoudre ce problème
Analog Devices, Inc. (ADI) maîtrise parfaitement les exigences de détection et de mesure des entreprises qui souhaitent maximiser l’efficacité et la durée de vie de leurs équipements, ou qui fournissent des solutions de mesure et d’analyse à leurs utilisateurs finaux.
Comme le savent la plupart de ses clients, les opérations de détection et de mesure imposées par la maintenance prédictive peuvent être prises en charge grâce à l’offre technologique combinée proposée par ADI au niveau des composants, mais également à un plus haut niveau d’intégration grâce à l’intégration d’éléments µModule et de produits de puissance μModule dans la chaîne du signal, ce qui permet à nos clients d’accélérer la phase de prototypage ou de conception de produits viables.
ADI fournit l’ensemble des composants qui forment la chaîne du signal, des capteurs MEMS basse consommation aux convertisseurs de données hautes performances et basse consommation, en passant par les solutions de connectivité sans fil et de gestion de l’énergie. L’offre technologique d’ADI réunit les meilleures options de performances pour les systèmes centralisés montés en rack, tout en répondant aux besoins des nœuds de surveillance distribués. C’est dans le monde analogique que sont créées les données. Analog Devices se positionne historiquement à la pointe de cette technologie, avec pour ambition de convertir ces données en informations réelles à la fois significatives et utiles.
www.analog.com