www.industrieweb.fr
14
'25
Written on Modified on
Un contrôle sans faille grâce à l’aide des caméras IDS USB3 uEye+ XC
Un système multi-caméras avec IA et une traçabilité complète ne laisse aucune chance aux erreurs.
en.ids-imaging.com
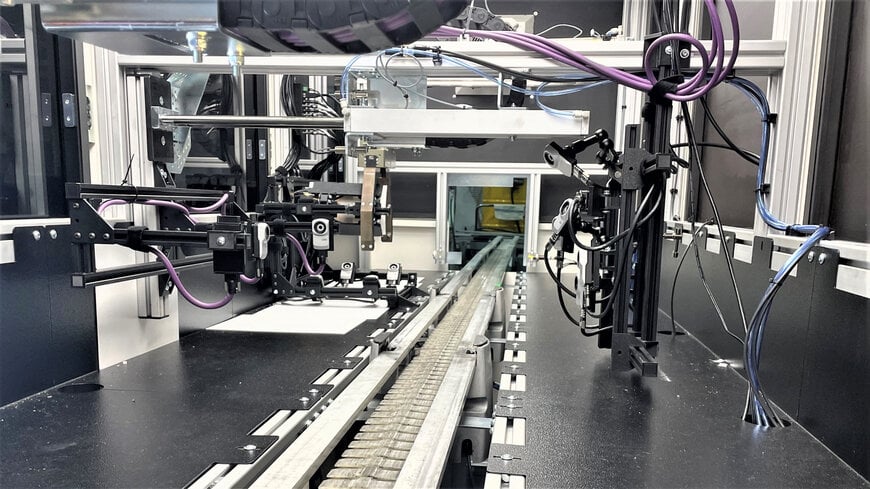
Tunnel à caméra multi-cellules pour une manipulation automatisée
Dans des domaines tels que le travail des métaux de haute précision, la précision n'est pas une option. Il s'agit notamment du secteur automobile et de ses fournisseurs, qui traversent une crise profonde dans notre pays pour diverses raisons. Les conflits commerciaux ne sont pas les seuls à affaiblir l'industrie automobile allemande : les retards en matière d'innovation, les coûts élevés et la faible efficacité sont autant d'éléments qui font que l'industrie automobile allemande s'affaiblit. Les entreprises sont soumises à une énorme pression, non seulement pour livrer des produits fiables et de qualité irréprochable, mais aussi pour réduire leurs coûts d'exploitation. Des solutions numériques sont demandées dans la production afin de surmonter les anomalies de produits ou de réduire les taux de rebut. La réponse : L'intelligence artificielle en interaction avec la vision par ordinateur et le lien entre les données de qualité et les données de production.
Les exigences sont toutefois élevées : Pour répondre aux normes strictes d'assurance qualité de l'industrie automobile, même les géométries de pièces complexes doivent être contrôlées à des vitesses de processus élevées - et ce avec une précision et une sécurité de processus maximales. Les fluctuations de la détection, la traçabilité insuffisante au niveau du numéro de série unique ou du lot et les défis posés par les conditions environnementales changeantes peuvent entraîner des erreurs coûteuses, des arrêts de production et des réclamations.
La société VIVALDI Digital Solutions GmbH a développé une solution exemplaire et innovante pour le contrôle de qualité par IA en temps réel. Dans ce que l'on appelle la SensorBox, le traitement d'image intelligent joue un rôle clé, en plus d'un serveur de périphérie avec processeur Intel. Conçue pour un sous-traitant automobile et son site de production en République tchèque, jusqu'à 70 caméras autofocus USB3 uEye+ XC d'IDS Imaging Development Systems assurent le contrôle visuel automatique pour l'inspection des surfaces dans plusieurs cellules de contrôle.
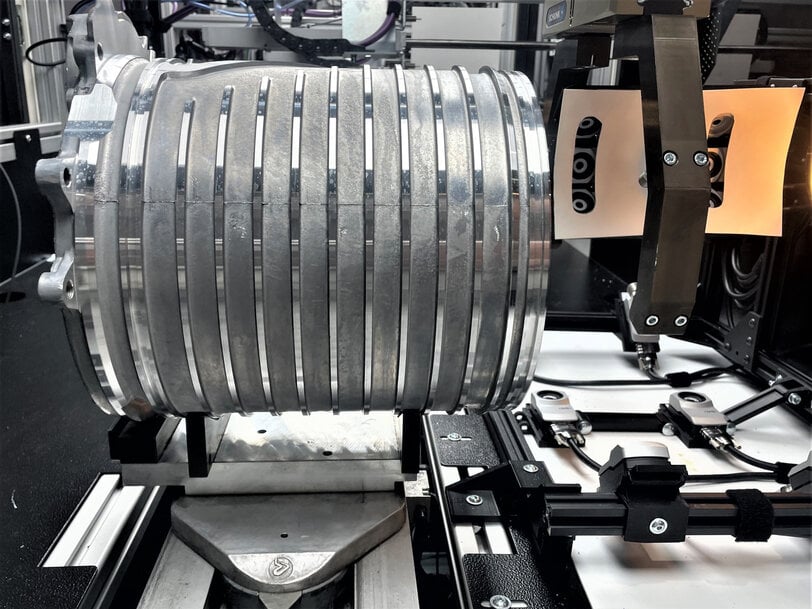
Même les géométries de pièces rondes avec de fortes réflexions doivent être contrôlées de manière fiable.
"Les caméras IDS intégrées dans les cellules d'inspection capturent des images haute résolution de la surface des composants en aluminium des équipementiers allemands, dans ce cas un moteur électrique", explique Uwe Siegwart, directeur chez Vivaldi. Les images prises sont prétraitées afin d'optimiser des facteurs tels que l'exposition, la balance des blancs et la correction des couleurs. L'IA détecte divers défauts de surface tels que les rayures, les pores ou la saleté. "Dans l'usine en République tchèque, les directives sont très strictes. Selon le cahier des charges, les défauts à partir de 0,2 millimètre doivent être détectés de manière sûre pour le processus. Le temps de contrôle par composant ne doit pas dépasser 36 secondes", explique Uwe Siegwart pour préciser le niveau d’exigence. Jusqu'à 2400 boîtiers de moteurs électriques sont contrôlés chaque jour de manière 100 % automatisée grâce au système mis en place avec succès.
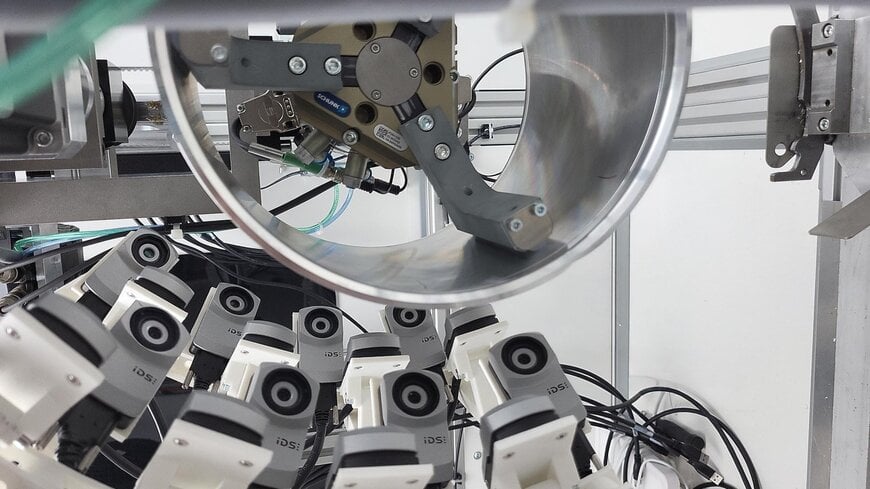
Des prises de vue simultanées assurent une inspection sans faille et permettent de respecter le temps de cycle
Pourquoi le spécialiste de l'IA a-t-il choisi la caméra uEye XC d'IDS ?
"Outre l'interface avec le contrôleur de caméra développé en interne et la taille compacte, l'étendue des fonctions des capteurs et, en raison de la quantité de caméras nécessaires, le prix ont également joué un rôle", explique Eike Humpert du département Business Development de Vivaldi. "Le fait que la caméra autofocus puisse détecter plusieurs surfaces, chacune à une distance différente, a été déterminant". Cela simplifie énormément le processus de contrôle et assure une efficacité et une flexibilité accrues. Un facteur décisif lorsqu'il s'agit par exemple de tester différentes variantes de composants. En outre, la distance minimale entre l'appareil et l'objet pourrait être très facilement raccourcie grâce à la lentille d'adaptation macro.
Le capteur CMOS AR1335 de 13,10 mégapixels d'onsemi, dont est équipée la caméra compacte uEye+ XC, marque ici des points supplémentaires. Le capteur couleur à obturateur de type obturateur roulant (rolling shutter) (4200 x 3120 px, taille de pixel 4200,1 µm) offre une fréquence d'image de 20,0 images par seconde et garantit un maximum de détail. "La technologie des pixels BSI permet au capteur de fournir des résultats précis et fiables de manière constante, même dans des conditions d'éclairage non controlées", explique Jürgen Hejna, Product Owner Caméras 2D chez IDS. Il est particulièrement adapté à cette application, et pas seulement en raison de ses excellentes performances en basse lumière et de son bruit de pixels minimal. "Le zoom numérique 24x, combiné à l'auto-balance des blancs et à la correction précise des couleurs, contribue largement au succès de cette procédure de contrôle exigeante", souligne Jürgen Hejna. Avec des dimensions de seulement 32 x 61 x 19 millimètres, la caméra est compacte, robuste malgré sa légèreté et absolument adaptée à l'industrie. L'expert en caméras 2D cite encore un autre point positif : "Les composants utilisés ici se caractérisent par une longue disponibilité, une des exigences les plus importantes pour les solutions destinées à l'industrie automobile".
Intégration facile et performance maximale grâce à IDS peak
"Pour profiter pleinement des avantages précédemment cités des caméras IDS via USB3.0, nous misons sur IDS peak. Le SDK fourni par IDS nous permet d'intégrer de manière transparente les protocoles de transport IDS Vision dans notre code", conclut Uwe Siegwart à propos de l'intégration. Grâce au puissant kit de développement logiciel d'IDS, la caméra industrielle USB3 a pu être programmée de manière ciblée pour cette application. "Nous utilisons une API REST qui génère des images avec IDS peak via le protocole de transport IDS USB3 Vision. Grâce à IDS USB3 Vision, nous disposons d'une bande passante de 5 Gbit/s ou plus via USB3.0 - par rapport à l'alternative avec le pilote Video4Linux, où le taux de transfert via USB2.0 serait limité à 480 Mbit/s", ajoute Uwe Siegwart. L'avantage qui en résulte : des résolutions plus élevées et des temps de transmission plus courts grâce à l'augmentation de la bande passante.
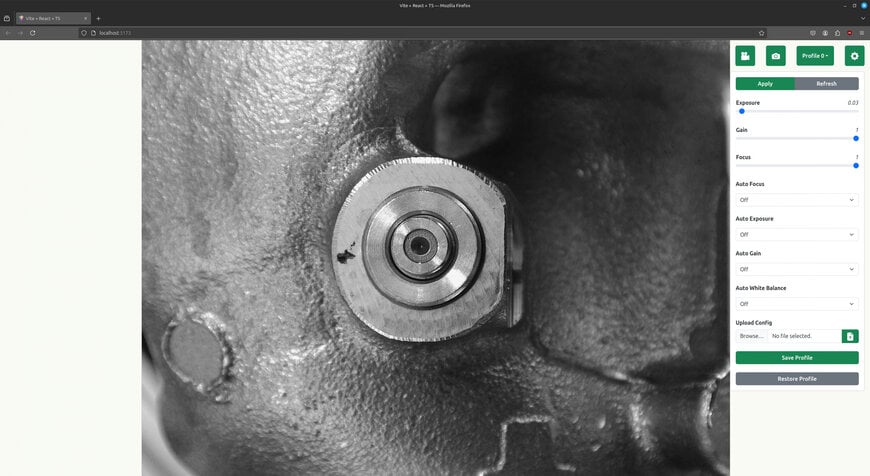
Les paramètres de la caméra peuvent être facilement modifiés directement dans le logiciel Vivaldi grâce à l'interface IDS peak
Analyses basées sur l'IA et contrôle synchrone des caméras par serveur Edge
La tâche de traitement d'image simultané est complexe, les défis sont nombreux. Les pièces en aluminium ont souvent des surfaces très brillantes qui reflètent la lumière et influencent donc fortement les prises de vue. Ces réflexions rendent difficile la détection fiable de défauts tels que les rayures, les frottements, les marques de broutage ou les irrégularités de surface, car elles sont souvent masquées ou faussées par les reflets de la lumière. De plus, dans le cas des pièces en aluminium, il arrive souvent que les surfaces non traitées aient un aspect différent à chaque fois. Les zones qui n'ont pas été traitées présentent des structures et des nuances de couleur différentes, qui ne doivent toutefois pas être confondues avec de véritables défauts. Le traitement d'image basé sur l'IA doit donc être en mesure de faire une distinction précise entre la structure normale du matériau et les véritables ébauches dans les surfaces à traiter, qui sont considérées comme des défauts.
Le traitement d'images est en outre rendu plus difficile par les conditions ambiantes dans les halls de production. Des facteurs tels que la qualité de l'air, notamment en raison d'un mélange de fluides de coupe, peuvent avoir un impact sur la clarté et la netteté des images capturées. À cela s'ajoutent les variations de température et les vibrations causées à la fois par la mécanique dans la boîte elle-même et par les autres machines dans l'environnement. Ces secousses peuvent entraîner des prises de vue floues ou des écarts de position, ce qui complique encore la détection des erreurs.
Pour relever ces défis, une coordination précise des systèmes de traitement d'images était nécessaire. L'éclairage, le positionnement de la caméra et les algorithmes d'évaluation des images ont été adaptés de manière à minimiser les reflets et à interpréter correctement les différences de matériaux. En même temps, le système est suffisamment robuste pour compenser les perturbations dues aux facteurs environnementaux et pour fournir des résultats fiables et constants. Les composants défectueux doivent pouvoir être remplacés rapidement et facilement par le service de maintenance du client de manière autonome.
"Le traitement des images se fait via une infrastructure optimisée. Il est possible de connecter jusqu'à huit caméras par hub USB, ce qui permet de capturer simultanément plusieurs zones d'inspection. Deux de ces hubs USB au maximum sont reliés à un 'cam-contrôleur' développé en interne, qui regroupe et traite les signaux d'image. Plusieurs contrôleurs de caméra sont mis en réseau avec le serveur Edge. Ce serveur se charge non seulement de calculer les analyses basées sur l'IA, mais communique aussi directement avec le système de contrôle de l'installation, qui coordonne le déclenchement des caméras et assure une détection synchrone".
Pas à pas vers un contrôle final automatisé
Les réticences face à l'introduction de nouvelles technologies basées sur l'IA est encore grande dans de nombreuses entreprises. Le processus de Vivaldi ne remplace pas directement le contrôle qualité existant. "Au cours des 8 à 12 premières semaines environ, le contrôle final manuel classique est effectué comme auparavant et soutenu par notre module vCHECK", décrit Eike Humpert. Cela signifie que le contrôleur final ne documente plus manuellement les erreurs à l'aide de listes ou de cartes d'erreurs, mais les marque numériquement sur les différentes images (détaillées). Pour cela, une interface numérique est disponible via un PC tactile au poste de contrôle final. Le contrôleur final localise l'erreur sur l'image et la catégorise en fonction d'un catalogue d'erreurs prédéfini.
Cela présente deux avantages : Premièrement, le contrôleur final se familiarise peu à peu avec le contrôle numérique final et s'habitue à travailler main dans la main avec Vivaldi. Deuxièmement, les images de produits marquées avec un marquage et une classification des erreurs sont utilisées pour l'entraînement de l'IA. De plus, des images de produits déjà existantes sont utilisées pour l'entraînement, par exemple des pièces défectueuses identifiées dans le passé et documentées dans le cadre du processus de réclamation.
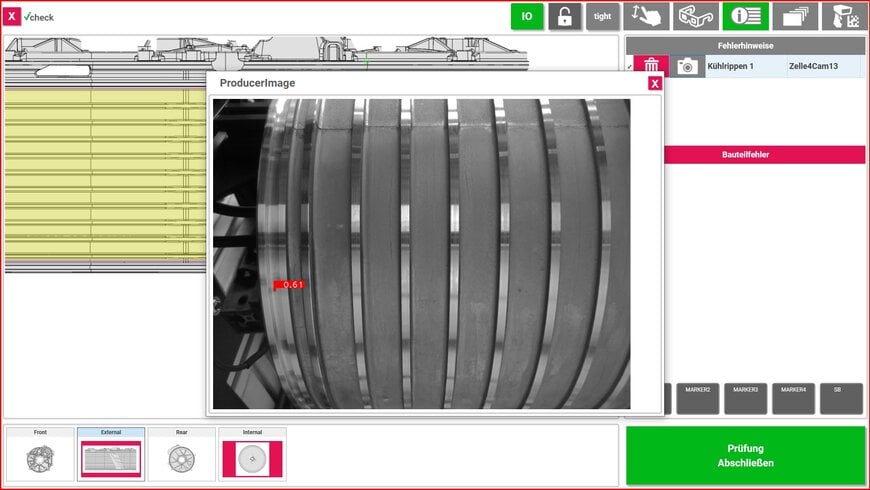
"Human-in-the-loop" dans la pratique - le PreCheck de l'IA est évalué par l'homme
"En combinant l'inspection manuelle et l'inspection automatisée des surfaces, nous pouvons atteindre un taux d'erreur inférieur à un pour cent, même pour les grandes quantités", souligne Eike Humpert. En même temps, cette approche permet à l'IA de s'entraîner en permanence. L'utilisateur a constamment le contrôle sur la manière dont l'IA vérifie et contrôle.
Toujours en point de mire : Reconnaissance d'images en temps réel combinée à l'archivage des informations pour la traçabilité
La mise en œuvre de la CamBox en combinaison avec de puissantes caméras industrielles USB3 a permis de réaliser un progrès décisif dans l'assurance qualité. Cette technologie permet un contrôle stable et très précis des composants - même à des vitesses de processus extrêmement élevées. La qualité des détections reste constante, sans aucune variation.
Un avantage décisif est la fiabilité de la détection, même lorsque les conditions environnementales changent individuellement. Les variations d'éclairage, de température ou d'autres influences externes n'affectent pas la précision des tests. Grâce à la capacité d'analyser simultanément plusieurs caractéristiques, l'efficacité des processus de contrôle augmente considérablement.
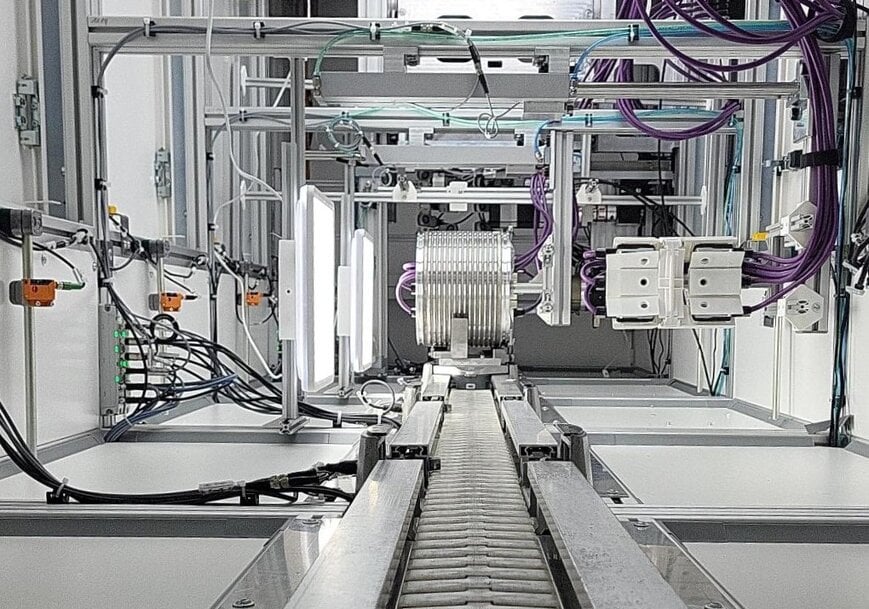
42 caméras uEye XC inspectent le boîtier d'un moteur électrique
Une autre caractéristique remarquable est l'enregistrement automatique d'images pour chaque numéro de série, qui garantit une traçabilité complète des données de processus et de qualité. Les résultats des tests peuvent ainsi être suivis et documentés à tout moment - un facteur décisif pour l'assurance qualité dans l'un des secteurs les plus exigeants au monde. "L'être humain doit continuer à avoir le dernier mot", déclare Uwe Siegwart. "Tout doit résister aux directives strictes des OEM en matière d'assurance qualité. Pour chaque composant, le cycle de vie complet de la création de valeur doit être documenté de manière sûre pour l'audit. Cela signifie quelle pièce a été placée sur quelle installation, à quel moment, et a été contrôlée avec quels moyens de contrôle et quels résultats". Tout cela est garanti par le système Vivaldi :
Les avantages en un coup d'œil :
• Contrôle stable des composants, même à des vitesses de processus élevées
• Détections fiables sans fluctuations
• Détection fiable malgré les changements individuels des conditions environnementales
• Contrôle simultané de plusieurs caractéristiques
• Enregistrement automatique des images pour une traçabilité complète
• Maintenance facile des composants
• Traçabilité au niveau des composants (données de processus et de qualité)
"Le traitement d'image est un composant central pour la traçabilité, qui est le véritable cœur technologique de la solution, et pour ce point, IDS est le partenaire idéal. De cette manière, la boucle est bouclée entre l'assurance qualité et la traçabilité". — Uwe Siegwart, directeur général chez Vivaldi —
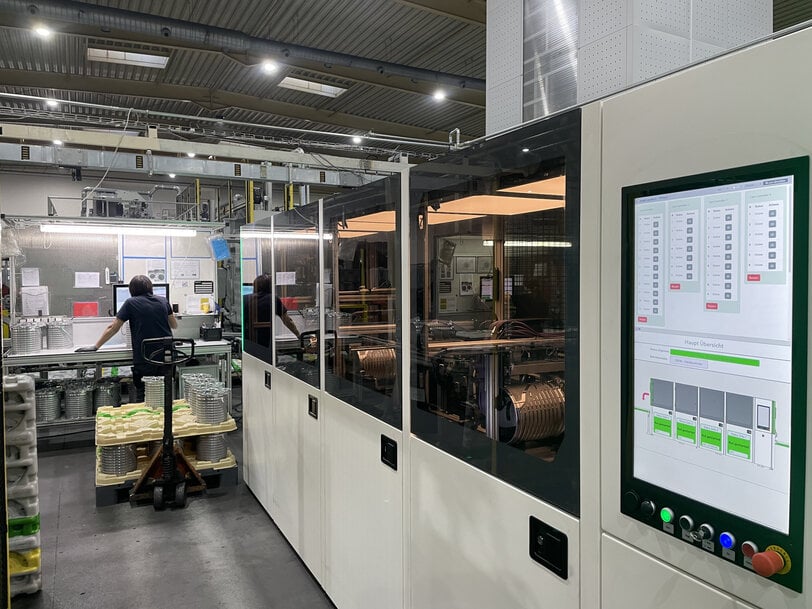
CamBox à 4 cellules avec poste de travail de post-contrôle
"Notre technologie est flexible, la plateforme est évolutive. Elle est parfaitement adaptée à la technologie la plus moderne et s'intègre sans problème dans les processus de fabrication les plus divers", explique Uwe Siegwart. "Grâce à l'évolutivité de la solution, les entreprises des secteurs les plus divers peuvent adapter leur contrôle qualité aux exigences individuelles". Grâce à un traitement intelligent des données de processus et de qualité, les sources d'erreur sont détectées à temps, ce qui permet une amélioration continue du processus au cœur des entreprises de production.
"La saisie numérique des données de qualité en temps réel ainsi que le lien avec d'autres paramètres de production augmentent non seulement l'efficacité, mais réduisent aussi considérablement les rebuts et les retouches. Les erreurs sont minimisées, les coûts sont réduits et les processus de production sont optimisés". En République tchèque, le système a déjà porté ses fruits : Le nombre de réclamations par an a été réduit de deux tiers et celui des défauts de surface non détectés a même été réduit à zéro.
Perspectives
Le marché du contrôle qualité numérique évolue rapidement, notamment grâce à une technologie de caméra plus avantageuse, par exemple en termes de résolutions plus élevées. Des processus et des outils de traitement d'images optimisés permettent en outre aux utilisateurs finaux d'effectuer des analyses en temps réel", constate Eike Humpert. "Ce qui est demandé, c'est une résolution améliorée, une construction plus compacte et des caméras dont le prix est optimisé". Le portefeuille du fabricant de caméras industrielles IDS est conçu pour répondre à ce besoin avec une technologie de pointe.
Caméra
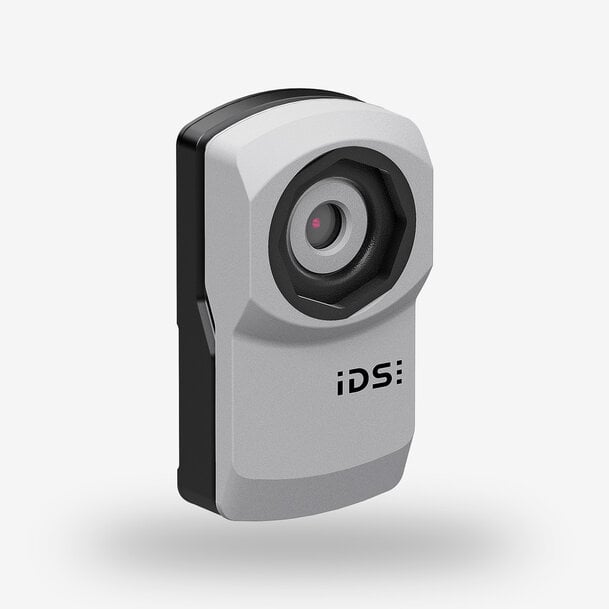
uEye XC - Automatically perfect images
Model used: U3-36LOXC
Camera family: uEye XC
www.ids-imaging.fr
Dans des domaines tels que le travail des métaux de haute précision, la précision n'est pas une option. Il s'agit notamment du secteur automobile et de ses fournisseurs, qui traversent une crise profonde dans notre pays pour diverses raisons. Les conflits commerciaux ne sont pas les seuls à affaiblir l'industrie automobile allemande : les retards en matière d'innovation, les coûts élevés et la faible efficacité sont autant d'éléments qui font que l'industrie automobile allemande s'affaiblit. Les entreprises sont soumises à une énorme pression, non seulement pour livrer des produits fiables et de qualité irréprochable, mais aussi pour réduire leurs coûts d'exploitation. Des solutions numériques sont demandées dans la production afin de surmonter les anomalies de produits ou de réduire les taux de rebut. La réponse : L'intelligence artificielle en interaction avec la vision par ordinateur et le lien entre les données de qualité et les données de production.
Les exigences sont toutefois élevées : Pour répondre aux normes strictes d'assurance qualité de l'industrie automobile, même les géométries de pièces complexes doivent être contrôlées à des vitesses de processus élevées - et ce avec une précision et une sécurité de processus maximales. Les fluctuations de la détection, la traçabilité insuffisante au niveau du numéro de série unique ou du lot et les défis posés par les conditions environnementales changeantes peuvent entraîner des erreurs coûteuses, des arrêts de production et des réclamations.
La société VIVALDI Digital Solutions GmbH a développé une solution exemplaire et innovante pour le contrôle de qualité par IA en temps réel. Dans ce que l'on appelle la SensorBox, le traitement d'image intelligent joue un rôle clé, en plus d'un serveur de périphérie avec processeur Intel. Conçue pour un sous-traitant automobile et son site de production en République tchèque, jusqu'à 70 caméras autofocus USB3 uEye+ XC d'IDS Imaging Development Systems assurent le contrôle visuel automatique pour l'inspection des surfaces dans plusieurs cellules de contrôle.
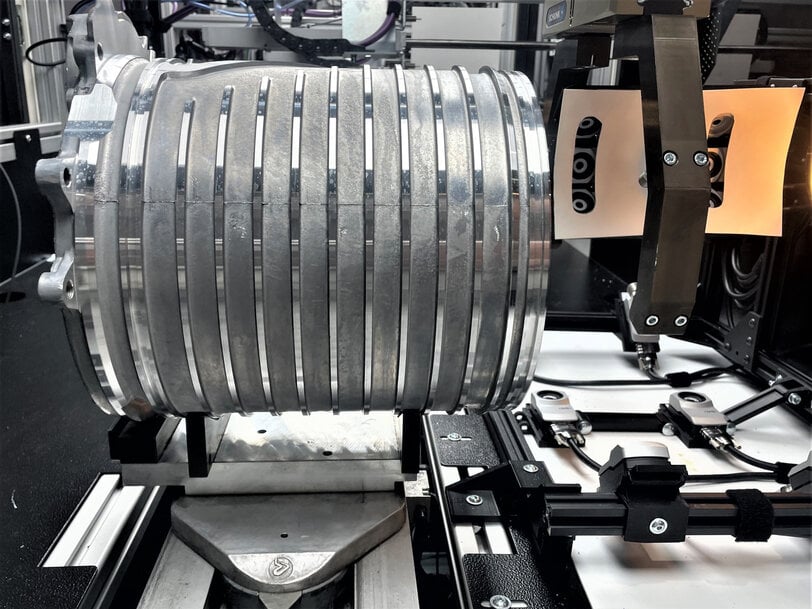
Même les géométries de pièces rondes avec de fortes réflexions doivent être contrôlées de manière fiable.
"Les caméras IDS intégrées dans les cellules d'inspection capturent des images haute résolution de la surface des composants en aluminium des équipementiers allemands, dans ce cas un moteur électrique", explique Uwe Siegwart, directeur chez Vivaldi. Les images prises sont prétraitées afin d'optimiser des facteurs tels que l'exposition, la balance des blancs et la correction des couleurs. L'IA détecte divers défauts de surface tels que les rayures, les pores ou la saleté. "Dans l'usine en République tchèque, les directives sont très strictes. Selon le cahier des charges, les défauts à partir de 0,2 millimètre doivent être détectés de manière sûre pour le processus. Le temps de contrôle par composant ne doit pas dépasser 36 secondes", explique Uwe Siegwart pour préciser le niveau d’exigence. Jusqu'à 2400 boîtiers de moteurs électriques sont contrôlés chaque jour de manière 100 % automatisée grâce au système mis en place avec succès.
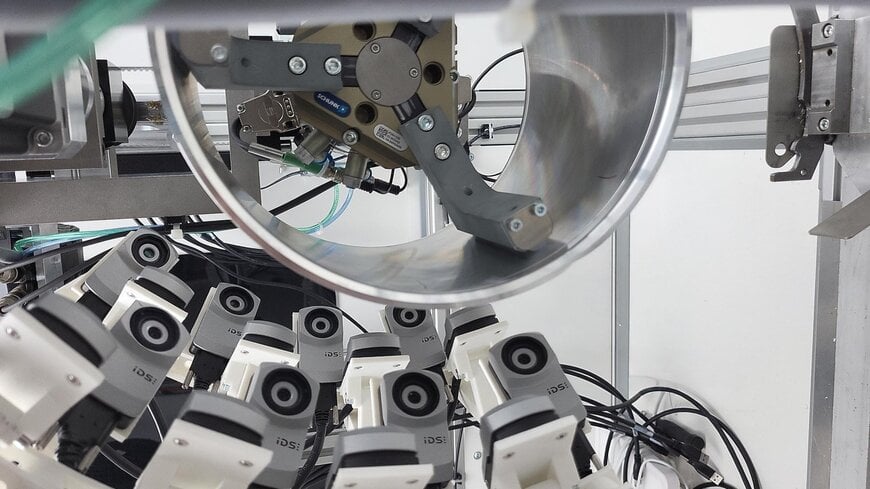
Des prises de vue simultanées assurent une inspection sans faille et permettent de respecter le temps de cycle
Pourquoi le spécialiste de l'IA a-t-il choisi la caméra uEye XC d'IDS ?
"Outre l'interface avec le contrôleur de caméra développé en interne et la taille compacte, l'étendue des fonctions des capteurs et, en raison de la quantité de caméras nécessaires, le prix ont également joué un rôle", explique Eike Humpert du département Business Development de Vivaldi. "Le fait que la caméra autofocus puisse détecter plusieurs surfaces, chacune à une distance différente, a été déterminant". Cela simplifie énormément le processus de contrôle et assure une efficacité et une flexibilité accrues. Un facteur décisif lorsqu'il s'agit par exemple de tester différentes variantes de composants. En outre, la distance minimale entre l'appareil et l'objet pourrait être très facilement raccourcie grâce à la lentille d'adaptation macro.
Le capteur CMOS AR1335 de 13,10 mégapixels d'onsemi, dont est équipée la caméra compacte uEye+ XC, marque ici des points supplémentaires. Le capteur couleur à obturateur de type obturateur roulant (rolling shutter) (4200 x 3120 px, taille de pixel 4200,1 µm) offre une fréquence d'image de 20,0 images par seconde et garantit un maximum de détail. "La technologie des pixels BSI permet au capteur de fournir des résultats précis et fiables de manière constante, même dans des conditions d'éclairage non controlées", explique Jürgen Hejna, Product Owner Caméras 2D chez IDS. Il est particulièrement adapté à cette application, et pas seulement en raison de ses excellentes performances en basse lumière et de son bruit de pixels minimal. "Le zoom numérique 24x, combiné à l'auto-balance des blancs et à la correction précise des couleurs, contribue largement au succès de cette procédure de contrôle exigeante", souligne Jürgen Hejna. Avec des dimensions de seulement 32 x 61 x 19 millimètres, la caméra est compacte, robuste malgré sa légèreté et absolument adaptée à l'industrie. L'expert en caméras 2D cite encore un autre point positif : "Les composants utilisés ici se caractérisent par une longue disponibilité, une des exigences les plus importantes pour les solutions destinées à l'industrie automobile".
Intégration facile et performance maximale grâce à IDS peak
"Pour profiter pleinement des avantages précédemment cités des caméras IDS via USB3.0, nous misons sur IDS peak. Le SDK fourni par IDS nous permet d'intégrer de manière transparente les protocoles de transport IDS Vision dans notre code", conclut Uwe Siegwart à propos de l'intégration. Grâce au puissant kit de développement logiciel d'IDS, la caméra industrielle USB3 a pu être programmée de manière ciblée pour cette application. "Nous utilisons une API REST qui génère des images avec IDS peak via le protocole de transport IDS USB3 Vision. Grâce à IDS USB3 Vision, nous disposons d'une bande passante de 5 Gbit/s ou plus via USB3.0 - par rapport à l'alternative avec le pilote Video4Linux, où le taux de transfert via USB2.0 serait limité à 480 Mbit/s", ajoute Uwe Siegwart. L'avantage qui en résulte : des résolutions plus élevées et des temps de transmission plus courts grâce à l'augmentation de la bande passante.
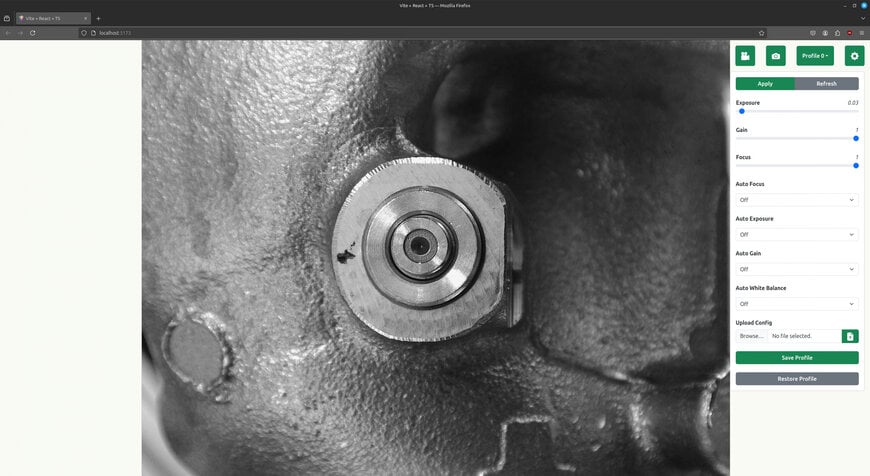
Les paramètres de la caméra peuvent être facilement modifiés directement dans le logiciel Vivaldi grâce à l'interface IDS peak
Analyses basées sur l'IA et contrôle synchrone des caméras par serveur Edge
La tâche de traitement d'image simultané est complexe, les défis sont nombreux. Les pièces en aluminium ont souvent des surfaces très brillantes qui reflètent la lumière et influencent donc fortement les prises de vue. Ces réflexions rendent difficile la détection fiable de défauts tels que les rayures, les frottements, les marques de broutage ou les irrégularités de surface, car elles sont souvent masquées ou faussées par les reflets de la lumière. De plus, dans le cas des pièces en aluminium, il arrive souvent que les surfaces non traitées aient un aspect différent à chaque fois. Les zones qui n'ont pas été traitées présentent des structures et des nuances de couleur différentes, qui ne doivent toutefois pas être confondues avec de véritables défauts. Le traitement d'image basé sur l'IA doit donc être en mesure de faire une distinction précise entre la structure normale du matériau et les véritables ébauches dans les surfaces à traiter, qui sont considérées comme des défauts.
Le traitement d'images est en outre rendu plus difficile par les conditions ambiantes dans les halls de production. Des facteurs tels que la qualité de l'air, notamment en raison d'un mélange de fluides de coupe, peuvent avoir un impact sur la clarté et la netteté des images capturées. À cela s'ajoutent les variations de température et les vibrations causées à la fois par la mécanique dans la boîte elle-même et par les autres machines dans l'environnement. Ces secousses peuvent entraîner des prises de vue floues ou des écarts de position, ce qui complique encore la détection des erreurs.
Pour relever ces défis, une coordination précise des systèmes de traitement d'images était nécessaire. L'éclairage, le positionnement de la caméra et les algorithmes d'évaluation des images ont été adaptés de manière à minimiser les reflets et à interpréter correctement les différences de matériaux. En même temps, le système est suffisamment robuste pour compenser les perturbations dues aux facteurs environnementaux et pour fournir des résultats fiables et constants. Les composants défectueux doivent pouvoir être remplacés rapidement et facilement par le service de maintenance du client de manière autonome.
"Le traitement des images se fait via une infrastructure optimisée. Il est possible de connecter jusqu'à huit caméras par hub USB, ce qui permet de capturer simultanément plusieurs zones d'inspection. Deux de ces hubs USB au maximum sont reliés à un 'cam-contrôleur' développé en interne, qui regroupe et traite les signaux d'image. Plusieurs contrôleurs de caméra sont mis en réseau avec le serveur Edge. Ce serveur se charge non seulement de calculer les analyses basées sur l'IA, mais communique aussi directement avec le système de contrôle de l'installation, qui coordonne le déclenchement des caméras et assure une détection synchrone".
Pas à pas vers un contrôle final automatisé
Les réticences face à l'introduction de nouvelles technologies basées sur l'IA est encore grande dans de nombreuses entreprises. Le processus de Vivaldi ne remplace pas directement le contrôle qualité existant. "Au cours des 8 à 12 premières semaines environ, le contrôle final manuel classique est effectué comme auparavant et soutenu par notre module vCHECK", décrit Eike Humpert. Cela signifie que le contrôleur final ne documente plus manuellement les erreurs à l'aide de listes ou de cartes d'erreurs, mais les marque numériquement sur les différentes images (détaillées). Pour cela, une interface numérique est disponible via un PC tactile au poste de contrôle final. Le contrôleur final localise l'erreur sur l'image et la catégorise en fonction d'un catalogue d'erreurs prédéfini.
Cela présente deux avantages : Premièrement, le contrôleur final se familiarise peu à peu avec le contrôle numérique final et s'habitue à travailler main dans la main avec Vivaldi. Deuxièmement, les images de produits marquées avec un marquage et une classification des erreurs sont utilisées pour l'entraînement de l'IA. De plus, des images de produits déjà existantes sont utilisées pour l'entraînement, par exemple des pièces défectueuses identifiées dans le passé et documentées dans le cadre du processus de réclamation.
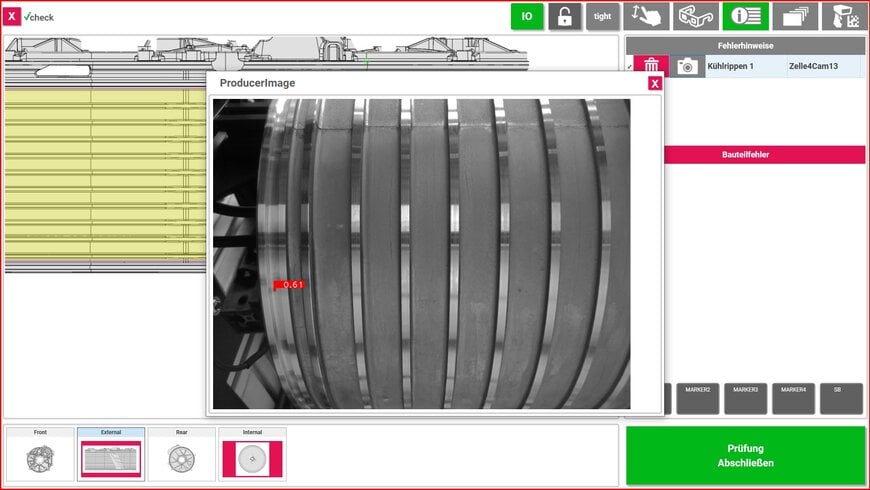
"Human-in-the-loop" dans la pratique - le PreCheck de l'IA est évalué par l'homme
"En combinant l'inspection manuelle et l'inspection automatisée des surfaces, nous pouvons atteindre un taux d'erreur inférieur à un pour cent, même pour les grandes quantités", souligne Eike Humpert. En même temps, cette approche permet à l'IA de s'entraîner en permanence. L'utilisateur a constamment le contrôle sur la manière dont l'IA vérifie et contrôle.
Toujours en point de mire : Reconnaissance d'images en temps réel combinée à l'archivage des informations pour la traçabilité
La mise en œuvre de la CamBox en combinaison avec de puissantes caméras industrielles USB3 a permis de réaliser un progrès décisif dans l'assurance qualité. Cette technologie permet un contrôle stable et très précis des composants - même à des vitesses de processus extrêmement élevées. La qualité des détections reste constante, sans aucune variation.
Un avantage décisif est la fiabilité de la détection, même lorsque les conditions environnementales changent individuellement. Les variations d'éclairage, de température ou d'autres influences externes n'affectent pas la précision des tests. Grâce à la capacité d'analyser simultanément plusieurs caractéristiques, l'efficacité des processus de contrôle augmente considérablement.
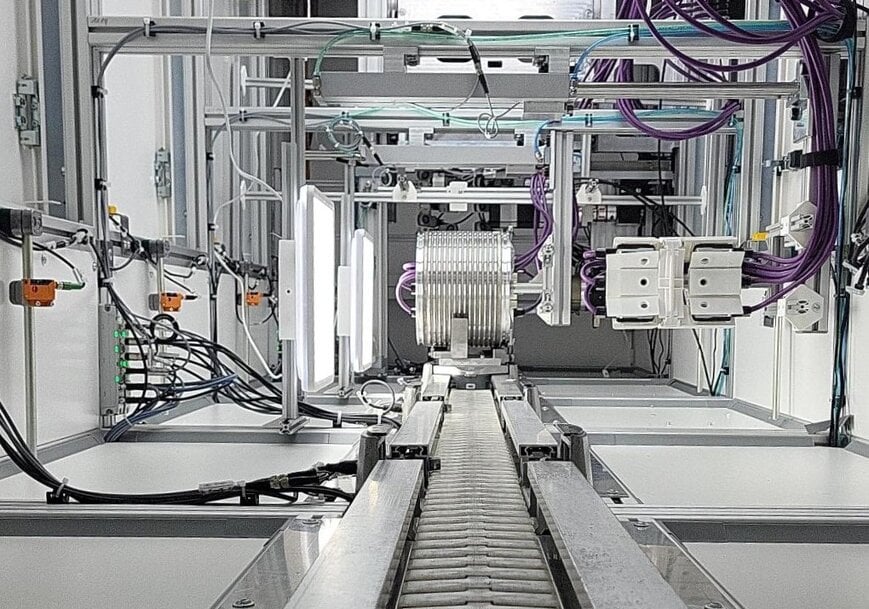
42 caméras uEye XC inspectent le boîtier d'un moteur électrique
Une autre caractéristique remarquable est l'enregistrement automatique d'images pour chaque numéro de série, qui garantit une traçabilité complète des données de processus et de qualité. Les résultats des tests peuvent ainsi être suivis et documentés à tout moment - un facteur décisif pour l'assurance qualité dans l'un des secteurs les plus exigeants au monde. "L'être humain doit continuer à avoir le dernier mot", déclare Uwe Siegwart. "Tout doit résister aux directives strictes des OEM en matière d'assurance qualité. Pour chaque composant, le cycle de vie complet de la création de valeur doit être documenté de manière sûre pour l'audit. Cela signifie quelle pièce a été placée sur quelle installation, à quel moment, et a été contrôlée avec quels moyens de contrôle et quels résultats". Tout cela est garanti par le système Vivaldi :
Les avantages en un coup d'œil :
• Contrôle stable des composants, même à des vitesses de processus élevées
• Détections fiables sans fluctuations
• Détection fiable malgré les changements individuels des conditions environnementales
• Contrôle simultané de plusieurs caractéristiques
• Enregistrement automatique des images pour une traçabilité complète
• Maintenance facile des composants
• Traçabilité au niveau des composants (données de processus et de qualité)
"Le traitement d'image est un composant central pour la traçabilité, qui est le véritable cœur technologique de la solution, et pour ce point, IDS est le partenaire idéal. De cette manière, la boucle est bouclée entre l'assurance qualité et la traçabilité". — Uwe Siegwart, directeur général chez Vivaldi —
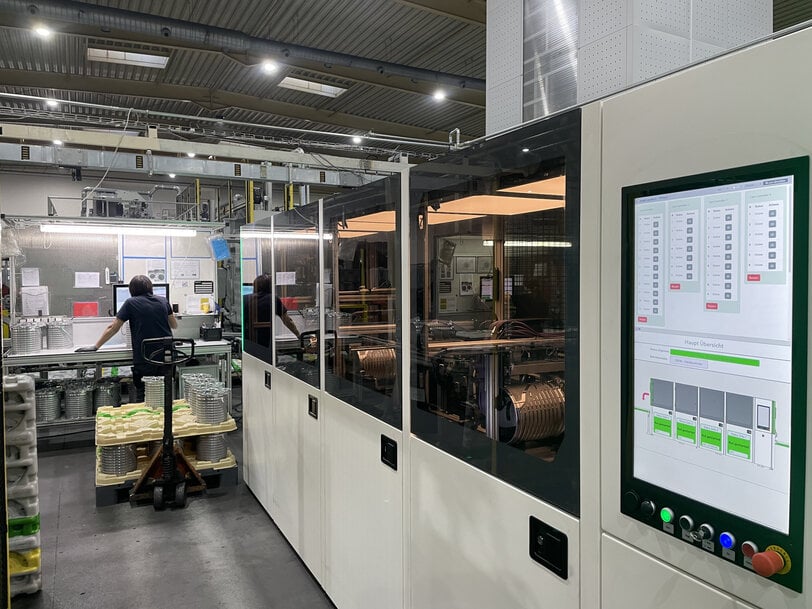
CamBox à 4 cellules avec poste de travail de post-contrôle
"Notre technologie est flexible, la plateforme est évolutive. Elle est parfaitement adaptée à la technologie la plus moderne et s'intègre sans problème dans les processus de fabrication les plus divers", explique Uwe Siegwart. "Grâce à l'évolutivité de la solution, les entreprises des secteurs les plus divers peuvent adapter leur contrôle qualité aux exigences individuelles". Grâce à un traitement intelligent des données de processus et de qualité, les sources d'erreur sont détectées à temps, ce qui permet une amélioration continue du processus au cœur des entreprises de production.
"La saisie numérique des données de qualité en temps réel ainsi que le lien avec d'autres paramètres de production augmentent non seulement l'efficacité, mais réduisent aussi considérablement les rebuts et les retouches. Les erreurs sont minimisées, les coûts sont réduits et les processus de production sont optimisés". En République tchèque, le système a déjà porté ses fruits : Le nombre de réclamations par an a été réduit de deux tiers et celui des défauts de surface non détectés a même été réduit à zéro.
Perspectives
Le marché du contrôle qualité numérique évolue rapidement, notamment grâce à une technologie de caméra plus avantageuse, par exemple en termes de résolutions plus élevées. Des processus et des outils de traitement d'images optimisés permettent en outre aux utilisateurs finaux d'effectuer des analyses en temps réel", constate Eike Humpert. "Ce qui est demandé, c'est une résolution améliorée, une construction plus compacte et des caméras dont le prix est optimisé". Le portefeuille du fabricant de caméras industrielles IDS est conçu pour répondre à ce besoin avec une technologie de pointe.
Caméra
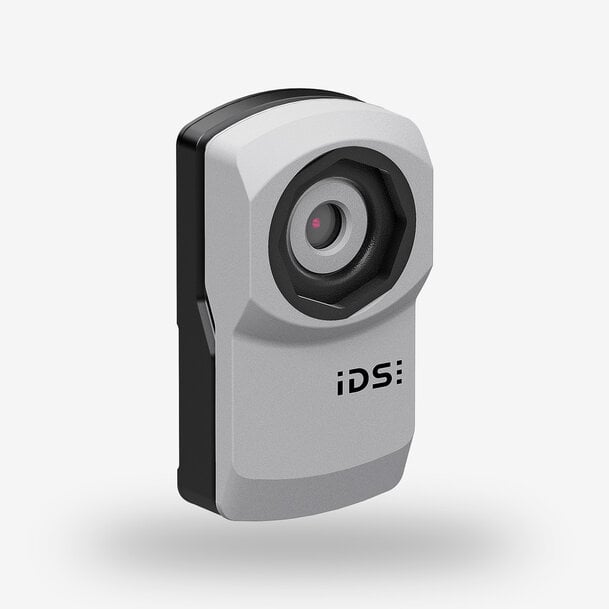
uEye XC - Automatically perfect images
Model used: U3-36LOXC
Camera family: uEye XC
www.ids-imaging.fr