www.industrieweb.fr
01
'09
Written on Modified on
CIAT reçoit les certifications ISO 14001 et OHS 18001
Trois sites de production français du Groupe CIAT (Culoz, Belley, Chautagne) viennent de recevoir les certifications ISO 14001 et OHS 18001. Alors que la première concerne le respect environnemental des usines, la seconde se concentre sur la sécurité et la santé des salariés dans les process de fabrication et dans le cadre de l’utilisation des produits. CIAT, qui veut devenir une référence en matière d' Hygiène, Santé, Sécurité, et Environnement, devient ainsi un des seuls constructeurs de pompes à chaleur à détenir les deux certificats. Dans un contexte de fort développement du groupe, cette démarche s’inscrit dans le programme d’excellence industrielle, dans toutes les usines CIAT.
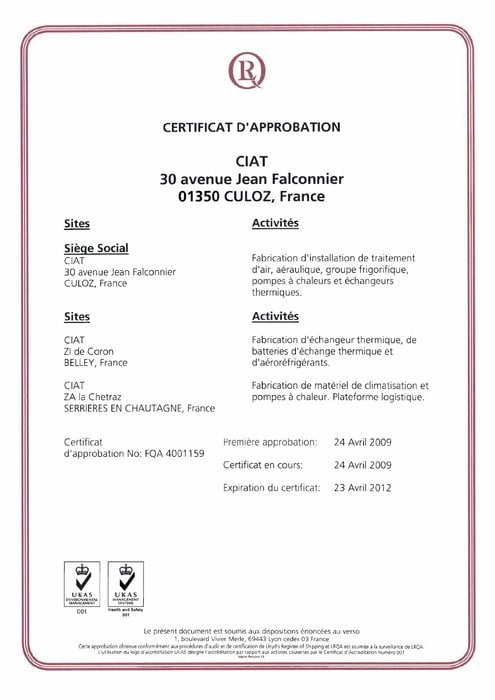
Entreprise responsable, CIAT pratique depuis plusieurs années, une politique d’innovation produits inscrite dans une démarche de développement durable : utilisation de fluides frigorigènes écologiques, mises au point de procédés en vue d’une réduction croissante de la consommation d’énergie, traitement d’air nouvelle génération… Pour aller plus loin, le Groupe a lancé dès 2007 un programme très ambitieux en matière d' Hygiène, Santé, Sécurité, et Environnement. C’est dans cette démarche que s’inscrivent les certifications obtenues.
L’objectif de l’ISO 14001 est d’inciter les sites industriels à consommer le moins possible d’énergie et de matières premières en fabrication, et également dans le cycle de vie du produit. Pour ce faire, plusieurs chantiers ont été mis en place.
Une chaufferie bois a été installée pour chauffer les locaux. Les déchets bois tels que les palettes de manutention servent de combustible, évitant ainsi le traitement de ces dernières. Composée d’une chaudière à foyer statique d’ 1,75 méga Watts, d’un broyeur à palettes avec dé ferraillage automatique et d’un dispositif de transfert, cette chaufferie bois dessert trois unités industrielles de CIAT, soit une superficie totale d’environ 43 000 m². 470 tonnes équivalent pétrole sont ainsi substituées chaque année.
Le circuit de livraison fournisseurs a été centralisé et optimisé afin de réduire les distances parcourues et donc les émissions CO2 des transporteurs. Au lieu d’avoir un circuit logistique par fournisseur, les circuits de livraison intègrent maintenant l’ensemble de la chaîne fournisseurs des usines.
La nouvelle station d’essai de groupes de froid intègre un circuit de recyclage thermique qui permet d’utiliser l’eau froide fournie en sortie du groupe pour refroidir l’air chaud rejeté par le groupe testé ; la consommation en eau est ainsi diminuée par cinq, et la consommation électrique de chaque essai par deux.
L’éclairage des locaux de production est maintenant régulé avec des luxmètres qui coupent l’électricité dès que l’éclairage naturel est suffisant.
La consommation d’eau de nappe a été diminuée de 50% en 5 ans, par la mise en œuvre de compteurs, variateurs et par l’amélioration du fonctionnement des stations d’essais.
Enfin, un partenariat a été passé avec des sous traitants locaux, pour valoriser 80% au moins des déchets de production: papier et carton, laine de verre, plastique. Un projet est également en cours pour installer plus de 1800 m2 de panneaux photovoltaïques sur les toitures.
En ce qui concerne le référentiel OHSAS 18001, c’est d’abord les toitures en fibro-ciment amianté qui sont progressivement démantelées (alors qu’il n’y a pas d’obligation légale de le faire), supprimant ainsi le risque Amiante et permettant d’améliorer l’isolation des locaux.
Depuis 2006 la totalité des CMR (Cancérogène, mutagène, toxique pour la reproduction) est éliminée des peintures, et des solvants utilisés. Des peintures à l’eau sont maintenant utilisées, et 30 tonnes solvants présents sur les sites ont été éliminés.
Les lignes de production ont été réaménagées pour réduire les contraintes physiques des employés. L’ergonomie des situations de travail a pour but de mettre en cohérence les objectifs de production avec la santé des travailleurs. Elle s’inscrit dans des politiques de prévention des Troubles Musculo-Squelettiques (TMS), d’insertion ou de maintien dans l’emploi de salariés présentant un handicap. Intégrer l’ergonomie dès la phase de conception des nouvelles productions est de plus un atout pour l’entreprise permettant de garantir une meilleure efficacité de la production. Ce projet a été piloté par le service médical du groupe et par un cabinet d’ergonomie.
Pour aller encore plus loin dans la démarche environnementale, une démarche d’éco conception a également été initiée. Il s’agit d’une démarche préventive, s’appuyant en partie sur l’analyse du cycle de vie, qui vise à réduire les impacts du produit sur l’environnement en envisageant dès la conception :
- la possibilité d’influer sur le choix des matériaux (notamment selon leur impact sanitaire),
- la meilleure efficacité énergétique,
- le potentiel de recyclage des matériaux,
- l’implication du constructeur dans la fin de vie du produit.
Le déploiement de cette démarche s’étendra sur l’ensemble des sites Européens du Group CIAT, pour fin 2012 au plus tard.
L’objectif de l’ISO 14001 est d’inciter les sites industriels à consommer le moins possible d’énergie et de matières premières en fabrication, et également dans le cycle de vie du produit. Pour ce faire, plusieurs chantiers ont été mis en place.
Une chaufferie bois a été installée pour chauffer les locaux. Les déchets bois tels que les palettes de manutention servent de combustible, évitant ainsi le traitement de ces dernières. Composée d’une chaudière à foyer statique d’ 1,75 méga Watts, d’un broyeur à palettes avec dé ferraillage automatique et d’un dispositif de transfert, cette chaufferie bois dessert trois unités industrielles de CIAT, soit une superficie totale d’environ 43 000 m². 470 tonnes équivalent pétrole sont ainsi substituées chaque année.
Le circuit de livraison fournisseurs a été centralisé et optimisé afin de réduire les distances parcourues et donc les émissions CO2 des transporteurs. Au lieu d’avoir un circuit logistique par fournisseur, les circuits de livraison intègrent maintenant l’ensemble de la chaîne fournisseurs des usines.
La nouvelle station d’essai de groupes de froid intègre un circuit de recyclage thermique qui permet d’utiliser l’eau froide fournie en sortie du groupe pour refroidir l’air chaud rejeté par le groupe testé ; la consommation en eau est ainsi diminuée par cinq, et la consommation électrique de chaque essai par deux.
L’éclairage des locaux de production est maintenant régulé avec des luxmètres qui coupent l’électricité dès que l’éclairage naturel est suffisant.
La consommation d’eau de nappe a été diminuée de 50% en 5 ans, par la mise en œuvre de compteurs, variateurs et par l’amélioration du fonctionnement des stations d’essais.
Enfin, un partenariat a été passé avec des sous traitants locaux, pour valoriser 80% au moins des déchets de production: papier et carton, laine de verre, plastique. Un projet est également en cours pour installer plus de 1800 m2 de panneaux photovoltaïques sur les toitures.
En ce qui concerne le référentiel OHSAS 18001, c’est d’abord les toitures en fibro-ciment amianté qui sont progressivement démantelées (alors qu’il n’y a pas d’obligation légale de le faire), supprimant ainsi le risque Amiante et permettant d’améliorer l’isolation des locaux.
Depuis 2006 la totalité des CMR (Cancérogène, mutagène, toxique pour la reproduction) est éliminée des peintures, et des solvants utilisés. Des peintures à l’eau sont maintenant utilisées, et 30 tonnes solvants présents sur les sites ont été éliminés.
Les lignes de production ont été réaménagées pour réduire les contraintes physiques des employés. L’ergonomie des situations de travail a pour but de mettre en cohérence les objectifs de production avec la santé des travailleurs. Elle s’inscrit dans des politiques de prévention des Troubles Musculo-Squelettiques (TMS), d’insertion ou de maintien dans l’emploi de salariés présentant un handicap. Intégrer l’ergonomie dès la phase de conception des nouvelles productions est de plus un atout pour l’entreprise permettant de garantir une meilleure efficacité de la production. Ce projet a été piloté par le service médical du groupe et par un cabinet d’ergonomie.
Pour aller encore plus loin dans la démarche environnementale, une démarche d’éco conception a également été initiée. Il s’agit d’une démarche préventive, s’appuyant en partie sur l’analyse du cycle de vie, qui vise à réduire les impacts du produit sur l’environnement en envisageant dès la conception :
- la possibilité d’influer sur le choix des matériaux (notamment selon leur impact sanitaire),
- la meilleure efficacité énergétique,
- le potentiel de recyclage des matériaux,
- l’implication du constructeur dans la fin de vie du produit.
Le déploiement de cette démarche s’étendra sur l’ensemble des sites Européens du Group CIAT, pour fin 2012 au plus tard.