www.industrieweb.fr
28
'12
Written on Modified on
Du maillon faible à l’usinage superstar
Pourquoi la nouvelle interface outil/broche permet d'augmenter les debits copeaux
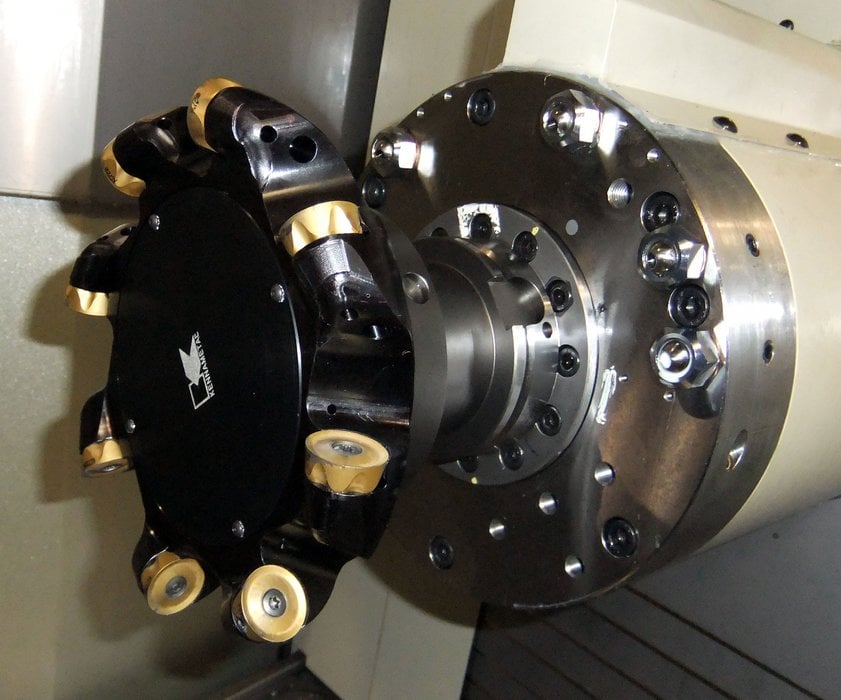
Mark Huston, Vice-président chargé des solutions techniques évoluées globales,
Doug Ewald, Directeur chargé de la gestion globale des produits, Systèmes d’Outillage,
Ruy de Frota de Souza, Responsable systèmes d’outillage globaux, Ingénierie Produits Kennametal Inc., Latrobe (Pennsylvanie).
L’usinage des matériaux durs comme le titane constitue un véritable défi pour l'usinage d’alliages durs, sans compter la pression qu’imposent en outre les objectifs d’amélioration des rendements de production, conduit à optimiser le taux d’enlèvement de matière au regard de faibles vitesses et des efforts importants de coupe. Les fabricants de machines-outils ont réagi en lançant des centres spécialisés de fraisage et tournage caractérisés par une rigidité et un amortissement supérieurs au niveau de la broche et des structures essentielles de machines, ce afin de réduire les vibrations parasites qui détériorent la qualité de la pièce et mettent en péril la longévité de l’outil. En dépit des gains de productivité générés par ces avancées, le raccordement à broche lui-même constitue souvent le maillon faible.
Dans la plupart des cas, l'interface outil/broche détermine la quantité de matière pouvant être enlevée sur une opération donnée. Cela tient au fait que cette interface doit résister à de lourdes charges et cependant conserver sa rigidité, jusqu’à une déflexion trop élevée des outils ou un début de broutement. Grâce aux progrès constants des outils de coupe et des centres d’usinage, une interface exploitant toute la puissance disponible constitue un point important à envisager en phase initiale de planification de la production.
Plusieurs types d'interface broche ont été développés ou optimisés au cours des dernières décennies. En raison d’un bon rapport coût/utilité, le cône ISO à queue 7/24 a envahi l’un des systèmes les plus prisés du marché. Ce cône a connu un grand succès dans de nombreuses applications, mais ses limites en matière de précision et grande vitesse ont porté un coup d’arrêt à sa progression.
L’avènement du contact direct a marqué une évolution importante par rapport au cône standard à queue 7/24. La combinaison d’un contact direct et d’un robuste cône à queue 7/24 procure une précision plus élevée dans le sens de l’axe Z, mais présente néanmoins quelques inconvénients, à savoir le manque de rigidité à grande vitesse ou par forces transversales élevées. La plupart des outils du marché sont robustes, mais avec des broches offrant une force de serrage relativement faible. La rigidité du raccordement est limitée, car l’interférence radiale nécessite d’être la plus réduite possible. Les tolérances requises pour réaliser un contact direct réussi sont ainsi très étroites, ce qui a pour conséquence des coûts de fabrication élevés.
En 1985, Kennametal et WIDIA ont monté un projet commun visant à développer un système de remplacement rapide universel, connu aujourd’hui sous l’appellation KMTM et récemment standardisé sous la norme ISO 26622. Au début des années 90, on a commencé à employer en Europe, sur les machines CNC, le système HSK devenu plus tard DIN 69893, puis ISO 12164.
L’outil de remplacement rapide KM™ comporte deux composants de base : le dispositif de serrage et la tête de coupe. Le dispositif de serrage se monte sur la machine outil (tourelle ou porte-outil pour les applications fixes, et broche tournante pour les applications rotatives) et accueille l’unité de coupe ou le porte-outil de remplacement. En cas de nécessité de remplacement de l’outil, l’opérateur libère simplement le mécanisme de verrouillage, insère la nouvelle unité de coupe et la verrouille en place. Le temps d’immobilisation de la machine est, tout au plus, l’affaire de quelques secondes.
Le KM4XTM de Kennametal représente la génération de KM suivante. Sans doute, certains systèmes sont-ils capables de transmettre une énorme quantité de couple ; mais les efforts de coupe génèrent également des moments de flexion qui dépassent alors les capacités de l’interface avant même d’atteindre les limites de couple. En combinant une force de serrage élevée à des niveaux d’interférence optimisés, le KM4X garantit un raccordement robuste, une rigidité particulièrement élevée et une capacité de charge en flexion qui améliorent sensiblement les performances de l’usinage des alliages et autres matériaux à haute résistance, en assurant des taux d’enlèvement de métal extrêmement élevés et la réalisation quotidienne d’un nombre supérieur de pièces.
Résistance au moment de flexion multipliée par trois
Le raccordement à broche doit dispenser des capacités de couple et de charge en flexion compatibles avec les caractéristiques de la machine outil et les exigences de niveaux de productivité supérieurs. Il ressort clairement que, dans les applications de fraisage en bout, où les longueurs de projection sont généralement plus importantes, le facteur limitant, c’est la capacité de flexion de l’interface à broches. A titre d’exemple, une fraise hélicoïdale (hérisson) doté d’une projection de 250 mm du support de broche et d’un diamètre de 80 mm, génère 4620 Nm de moment de flexion et moins de 900 Nm de couple lorsqu’on enlève 360 cm3/min de titane de type Ti6Al4V avec un engagement de 12,7 mm et une profondeur de passe de 63,5 mm.
Les paramètres les plus critiques d’un raccordement à broche par cône et surface de contact sont la force de serrage et l’interférence radiale. La rigidité du raccordement peut être augmentée en optimisant la force de serrage et en choisissant les bonnes valeurs d’interférence.
Grâce à trois éléments de contact garantissant une meilleure stabilité et optimisant la répartition de la force de serrage et l’ajustement, la conception du KM4XTM se traduit par une capacité de résistance au moment de flexion trois fois supérieure à celle des autres systèmes d’outillages.
Autrement dit :
- les ateliers peuvent mettre à profit les machines-outils haute performance équipées d’un KM4X pour augmenter les avances et vitesses dans les opérations d’usinage difficiles, pour ainsi exploiter pleinement le potentiel de productivité de la machine outil.
- Un raccordement KM4X plus petit comme le KM4X100 assurera souvent des résultats identiques voire supérieurs à ceux d’un raccordement de plus grande dimension.
- Les systèmes KM4X peuvent être appliqués sur les centres d’usinage et tournage multitâches et les machines transferts en mode manuel, semi-automatique ou automatique mode.
Par conception, le KM4X est capable d’exécuter un large éventail d’opérations, depuis de faibles vitesses et couples élevés jusqu’à des vitesses élevées et faibles couples, garantissant aux fabricants de tirer le maximum de leurs équipements de production.
Le fraisage, le perçage et le tournage de toute une gamme de matériaux ont tout simplement fait un bond de productivité !
Les règles et recommandations sont par nature générales. Si vous avez besoin de conseils particuliers concernant l’usinage du titane et notamment le KM4X, veuillez contacter Kennametal ou visiter www.kennametal.com.
Visuels :
KM4X_with_cutter.jpeg : En combinant une force de serrage élevée à des niveaux d’interférence optimisés, le KM4X garantit un raccordement robuste, une rigidité particulièrement élevée et une capacité de charge en flexion qui améliorent sensiblement les performances de l’usinage des alliages et autres matériaux à haute résistance, en assurant des taux d’enlèvement de métal extrêmement élevés et la réalisation quotidienne d’un nombre supérieur de pièces.
KM4X_8.jpeg : Le système de raccordement à broche KM4XTM de Kennametal est configuré pour un usage intensif et capable d’exécuter ses tâches dans des conditions de vitesse élevée ou faible, et de couple élevé. Sans KM4X, les outils de coupe hélicoïdaux comme celui-ci dépasseraient les contraintes de moment de flexion bien avant d’atteindre les limites de couple.
KM4X_9.jpeg : Contact et force de serrage combinés favorisent un meilleur ajustement et multiplie par trois la résistance au moment de flexion par rapport aux autres systèmes. Le remplacement d’outil est rapide et facile, ce qui réduit les temps d’immobilisation des machines.