www.industrieweb.fr
10
'20
Written on Modified on
MARCHESINI GROUP, GÉANT DES MACHINES D'EMBALLAGE, ADOPTE LE MODÈLE ÉCONOMIQUE DE LA PRODUCTION SUR MESURE GRÂCE À L'IMPRESSION 3D DE STRATASYS
Le groupe surmonte les limites de la fabrication traditionnelle pour produire de façon rentable des pièces de machine à la demande. Ses douze imprimantes 3D Stratasys de qualité industrielle, qui fonctionnent à temps plein, en font l'un des principaux clients européens de Stratasys.
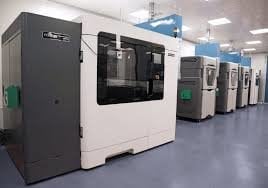
Marchesini Group S.p.A. est un fabricant italien de machines d'emballage, leader à échelle internationale, et qui fournit notamment à certains des plus grands noms des secteurs de la pharmacie, des cosmétiques et de l'agro-alimentaire. S'agissant de l'un des plus gros clients de Stratasys en Europe, le groupe fait aujourd'hui la lumière sur la façon dont il a pu mettre en place un modèle économique de production totalement sur mesure et répondre aux besoins du secteur de l'emballage international, grâce à sa batterie d'imprimantes 3D Stratasys de qualité industrielle.
Implanté à Pianoro, en Italie, Marchesini Group possède des locaux dédiés à l'impression 3D et équipés de dix imprimantes 3D FDM de qualité de production Stratasys, à savoir une Fortus 900mc de grandes dimensions, quatre Fortus 450mc et cinq systèmes F270, ainsi que deux imprimantes 3D multi-matériaux PolyJet. La technologie est utilisée tout au long de la phase de conception, du développement et de la fabrication des encartonneuses, qui sont le produit phare de l'entreprise, parmi d'autres lignes d'emballage. Chaque machine fabriquée est personnalisée pour un secteur déterminé ou pour le processus de production spécifique d'un client, ce qui est essentiel pour assurer une performance et une efficacité optimales sur le terrain.
« Chez Marchesini Group, nous avons l'habitude de dire que ce qui fait notre ordinaire, c'est l'extraordinaire : nous devons faire face à des projets complexes, totalement sur mesure, pratiquement tous les jours », affirme Mirko Fortunati, responsable de la coordination des ateliers mécaniques chez Marchesini Group. Cependant, la production de pièces complexes et sur mesure avec les méthodes de fabrication traditionnelles s'avérait extrêmement coûteuse et chronophage, un inconvénient aujourd'hui devenu incompatible avec les demandes croissantes du secteur actuel de l'emballage.
« La fabrication additive de Stratasys nous a permis de résoudre ces problèmes et d'adopter un modèle de production sur mesure, ce qui a été décisif pour notre activité », a-t-il poursuivi. « L'intégration d'imprimantes 3D FDM de qualité industrielle dans notre processus de production a considérablement réduit les délais de fabrication de nos pièces, qui sont passés de plusieurs semaines à seulement quelques jours. Nous pouvons en outre produire de façon rentable la quantité exacte de pièces qu'il nous faut, sans besoin d'outillage ou d'usinage coûteux. Cette capacité de production à la demande permet aux ingénieurs de tirer parti de la plus grande liberté de conception de l'impression 3D, et donne à Marchesini Group la possibilité d'offrir des résultats de meilleure qualité à ses clients. »
Et surtout, cette capacité de production à la demande s'étend aussi à la maintenance et à la réparation. Pour ses machines d'emballage installées chez des clients du monde entier, le groupe est désormais en mesure d'imprimer en 3D, rapidement et à moindre coût, des pièces de rechange personnalisées à la demande, sans exiger la commande d'une quantité minimum. Cela permet à Marchesini Group de livrer ses clients en un temps record, tout en évitant de maintenir des installations de stockage coûteuses pour ses pièces.
Amélioration des performances des machines pour les clients
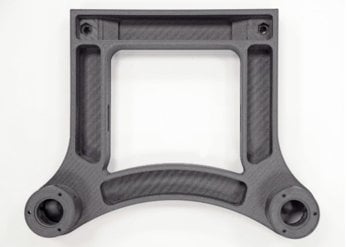
L'équipe a imprimé en 3D des milliers de pièces et composants fonctionnels pour ses machines d'emballage, y compris des boîtiers de protection, des systèmes de support de câbles et des boîtes de jonction, pour n'en citer que quelques-uns. Ces applications sont particulièrement importantes pour les systèmes d'emballage robotisés du groupe, où chaque composant est essentiel pour garantir l'agilité, la précision et la vitesse des mouvements du robot. Il s'agit d'un domaine dans lequel les matériaux d'impression 3D à hautes performances font une grande différence.
« L'emploi de thermoplastiques résistants, comme les filaments de FDM Nylon 12CF ou la résine ULTEM 9085 de Stratasys, au lieu de composants métalliques usinés avec des méthodes traditionnelles, nous a permis de réduire le poids de certaines pièces d'au moins 30 % », précise Fortunati. « Cela augmente la vitesse des mouvements et la productivité des robots pour nos clients, tout en diminuant le taux de dégradation. Ces matériaux d'impression 3D sont également capables de respecter des réglementations industrielles spécifiques, ce qui nous permet d'élargir cette technologie à encore plus d'applications de production et d'offrir plus d'innovations sur nos produits à nos clients. »
Marchesini Group utilise également la technologie Stratasys PolyJet pour fabriquer des pièces et des composants destinés à des applications qui requièrent la combinaison de deux ou plusieurs matériaux. « Un parfait exemple de cette technologie est la production de tenailles de saisie, qui sont conçues pour manipuler des objets légers, comme des notices ou de tout petits récipients. Grâce aux capacités avancées de l'impression 3D multi-matériaux, nous pouvons élaborer des conceptions complexes associant des matériaux durs et de type caoutchouc en une seule tâche d'impression, ce qui aurait normalement dû être réalisé en plusieurs étapes, longues et coûteuses », ajoute Fortunati.
La batterie d'imprimantes 3D de Stratasys au sein du département de fabrication additive de Marchesini Group fonctionne à plein temps.
Fortunati conclut : « Il est juste de dire que la fabrication additive fait partie intégrante de la production de Marchesini Group. Rien qu'en 2019, notre équipement d'impression 3D FDM a enregistré un total de 22 480 heures de fonctionnement, soit près de 15 heures par jour. Nos deux imprimantes 3D PolyJet ont fonctionné pendant un total de 1 700 heures, ce qui représente environ 8 heures par jour. Et au fur et à mesure que nous déployons ces technologies à l'ensemble de notre processus de conception et de production, il est probable que ces chiffres soient de plus en plus élevés. »