www.industrieweb.fr
14
'20
Written on Modified on
LA PREMIÈRE USINE DE CONSTRUCTION DE VÉHICULES ÉLECTRIQUES D’ALLEMAGNE POSE DE NOUVEAUX JALONS
Le plus important constructeur de véhicules automobiles au monde s’équipe pour l’avenir. Volkswagen mise radicalement sur l’électromobilité dans les prochaines années, et l’usine à Zwickau joue un rôle décisif en la matière. C’est là que vit le jour le modèle ID.3, viatique pour la nouvelle flotte de véhicules électriques. Les spécialistes du pliage de Bystronic sont de la partie.
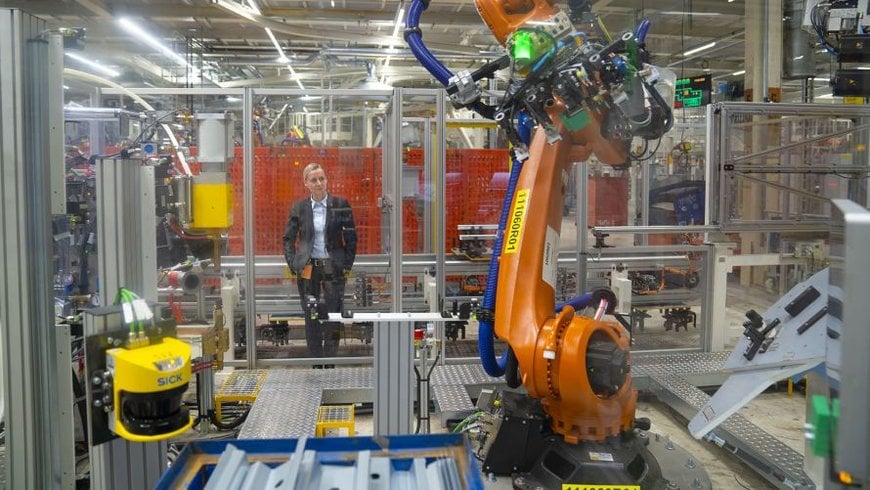
Dans l’industrie automobile, beaucoup de choses se déroulent à huis clos. C’est aussi le cas de la nouvelle orientation du constructeur en faveur de l’électromobilité. Mais lorsqu’Angela Merkel en personne donne le top départ de la production de la nouvelle VW ID.3, cela devient tout à fait officiel. Ceci s’est passé en novembre dernier à Zwickau en Saxe. Les chaînes de production y ont entamé le projet probablement le plus ambitieux pour le moment de toute l’industrie automobile.
L’ID.3 est bien plus qu’un nouveau modèle, car ce bolide matérialise en effet l’avenir de VW et débute une nouvelle ère. Le groupe s’est fixé pour objectif de devenir le premier constructeur au monde de véhicules électriques. Et cette annonce définit le programme. Ayant investi 1,2 milliards d’euros, VW ambitionne de faire de l’usine de Zwickau la plus grande usine de construction de véhicules électriques d’Europe. En 2021, plus de 300.000 véhicules électriques devraient sortir des chaînes de montage.
Des systèmes modulaires adaptables à toute la gamme
Jusqu’à présent, les ventes de véhicules électriques ne progressaient que très lentement. L’ID.3 doit cependant amener du changement en la matière – grâce à son prix attractif inférieur à 30.000 euros, un temps de charge extrêmement rapide et une autonomie jusqu’à 550 kilomètres. Jürgen Stackmann, membre du directoire de la marque, promet: «Aussi grande qu’une Golf de l’extérieur, avec l’intérieur d’une Passat et une accélération digne d’une GTI.» Les promesses ont manifestement été entendues par les clients: Plus de 30.000 véhicules ont déjà été commandés et seront livrés cette année encore.
L’ID.3 est à la base d’une génération de véhicules non polluants, allant du SUV T-Cross à l’e-Bulli. La plateforme modulaire électrique – ou MEB selon l’acronyme allemand – assure l’évolutivité requise: d’ici 2022, elle sera intégrée dans 27 véhicules de quatre marques du groupe. Le prototype «ID.R Pikes Peak» a déjà démontré que les possibilités d’évolution sont illimitées. En effet, lors de la course de côte éponyme aux États-Unis, la supercar dotée d’un puissant moteur électrique à transmission intégrale cumulant 680 ch est entrée dans l’histoire du sport automobile le 24 juin 2018 en pulvérisant le record absolu détenu par la légende des rallyes, Sébastien Loeb. Ce bolide restera certes un rêve pour le circuit, mais il a aussi démontré ce dont la technologie de motorisation électrique de VW est capable.
Durée de cycle de 76 secondes
Kati Langer se tient dans le hall de production N° 12. Elle examine l’Xpert 40 qui est intégrée à la cellule de production avec deux robots Kuka. La commerciale Bystronic, passionnée, qui s’est investie depuis le début dans le projet ID.3 aux côtés de VW, est visiblement fière de l’installation. «Pour assurer l’intégration parfaite de l’installation de pliage dans la ligne de production de VW, nous avons dû relever des défis en procédant à certains changements structurels», dit-elle tandis que nous observons les deux robots de pliage en pleine action.
Le premier robot prend la pièce de l’unité de tri et la dépose sur l’unité de centrage. Le deuxième robot l’emporte en un rien de temps à la presse plieuse et effectue les deux premières opérations de pliage. Il repose alors la pièce sur l’unité de centrage et le premier robot poursuit les opérations de pliage restantes. Deux écrous sphériques sont ensuite soudés dans une installation stationnaire. Le bras préhenseur prend ensuite la pièce et la dépose sur la bande de convoyeur.
L’ensemble du processus ne dure pas plus de 76 secondes. Ce fut un véritable plaisir de voir comment les robots accomplissent leurs séquences de pliage. Il est difficilement concevable, sans l’avoir vu de ses propres yeux, avec quelle élégance et agilité les deux robots s’échangent des pièces dans leurs mains, ou plus précisément, grâce à leurs préhenseurs. La pièce pliée qui est ensuite montée sur la structure porteuse du châssis sert à stabiliser le soubassement. Une seconde cellule de pliage entièrement automatisée forme une pièce qui est ensuite montée sur la partie avant du châssis.
www.bystronic.com