Modules électroniques sans circuits imprimés
La structuration directe au laser (LDS) est sans aucun doute une réussite particulièrement importante. Il est possible d’appliquer depuis près de 20 ans, des pistes électroniques conductrices directement à des pièces en plastique dès leur production en série.
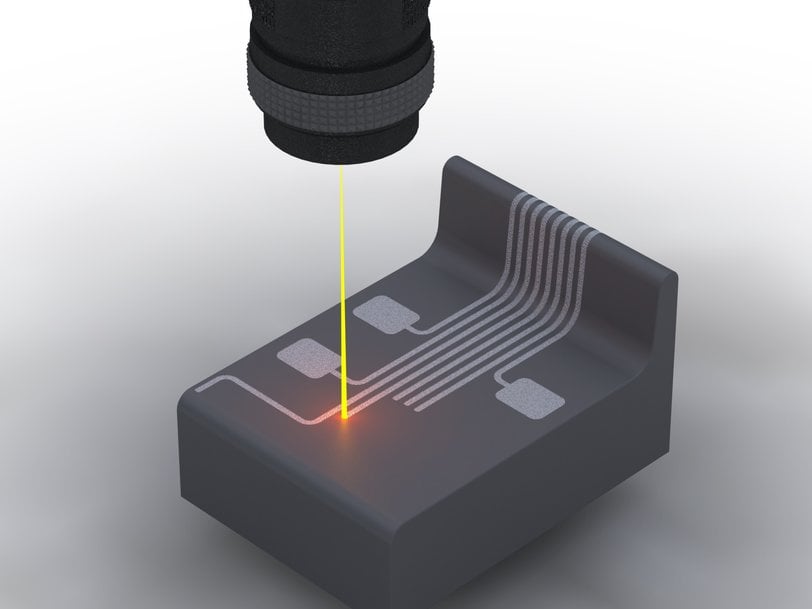
Structuration directe par laser (LDS) - La structure de la piste conductrice est appliquée en utilisant le processus LDS. LDS permet des modules électroniques aux formes géométriques flexibles. Grâce à ce processus, les téléphones portables, les aides auditives et les montres intelligentes deviennent de plus en plus petits et puissants.
LDS permet des modules électroniques aux formes géométriques flexibles. Un procédé grâce auquel les produits électroniques tels que les smartphones, les capteurs ou les appareils médicaux deviennent de plus en plus petits et puissants. Les processus de fabrication automatisés rendent également ce procédé de plus en plus attractif d’un point de vue économique.
L’espace pour les modules électroniques étant de plus en plus exigu, on est toujours à la recherche de solutions pour remplacer les circuits imprimés classiques. LDS permet une miniaturisation supplémentaire et des conceptions géométriques toujours plus complexes. Ce processus stable et fiable s'est également imposé dans des domaines particulièrement critiques pour la qualité tels que la technologie médicale ou les composants de sécurité destinés à l'industrie automobile.
Le processus LDS permet de réaliser des modules 3D
La structuration laser directe rend possible des modules 3D-MID (Mechatronic Integrated Devices ou Systèmes intégrés mécatroniques). Avec 3D-MID, les composants électroniques peuvent être montés directement sur un corps de base tridimensionnel, sans circuits imprimés ni câbles de connexion. Le corps de base est fabriqué par un processus de moulage par injection car le matériau thermoplastique contient un additif inorganique non conducteur.
Pour que la matière plastique puisse s’intégrer dans les conducteurs électriques, les additifs dans le matériau sont « activés » par structuration directe au laser. Le faisceau laser décrit les zones destinées aux pistes conductrices ce qui crée une structure micro-rugueuse. Les particules métalliques libérées forment les noyaux pour la métallisation chimique ultérieure. Ainsi, des pistes conductrices électriques sont appliquées dans les zones marquées par le laser. Les autres zones du corps de base tridimensionnel restent inchangées. Le composant en plastique peut être assemblé ultérieurement dans des processus SMD standard comme une carte de circuit imprimé traditionnel et convient également au processus de brassage dans un four de refusion.
La technologie laser peut être utilisée de manière flexible
HARTING 3D-MID AG est le plus grand fournisseur de composants 3D-MID en dehors de l'Asie. Pour le processus LDS, HARTING utilise des systèmes laser haute performance caractérisée par trois lasers en parallèle, chacun décalé de 45 degrés. Grâce à l'axe de rotation supplémentaire, il est possible de traiter les composants par le laser à 360 degrés et de tous les côtés en même temps. Cette technologie permet de réaliser des formes géométriques flexibles, telles que des coques de réflecteur ou des lumières LED. En dépit de la faible épaisseur de la piste conductrice comprise entre 16 à 20 μm, les pistes conductrices sont adaptées aux composants automobiles exigeants ou aux applications avec des courants allant jusqu'à 10 A, telles que les bobines chauffantes dans les caméras qui empêchent l'optique de s'embuer.
Dimensionnement et position - Valeur minimale des distances entre les pistes conductrices (a) : 150 μm de largeur minimale des pistes conductrices (b) : 150 à 250 μm Rayon (r) : 0,2 mm
Des changements fréquents lors du développement de l'électronique ou de nouveaux composants aux dimensions modifiées entraînent des ajustements complexes dans la production de circuits imprimés traditionnels. La disposition du laser, en revanche, peut être adaptée de manière très facilement grâce aux entrées du logiciel de contrôle du laser. Inutile de modifier le moulage par injection !
Par rapport aux procédés traditionnels, la production de prototypes chez LDS est également plus facile. HARTING peut produire le corps de base en plastique avec un matériau compatible LDS par impression 3D. Le moulage par injection avec des outils prototypes bon marché est également utilisé.
Nouvelles tendances dans le processus LDS
Au cours de ces dernières années la technologie LDS a été améliorée et développée dans plusieurs domaines :
- La zone de travail du laser a été agrandie en passant de 160 x 160 x 80 mm à 200 x 200 x 80 mm, ce qui permet d’avoir une densité de tassement plus élevée ou de traiter de pièces encore plus grandes.
- Il est possible de doubler la vitesse de travail du laser à 4 m / s en optimisant les unités asservies et les miroirs de guidage pour le faisceau laser, afin de réduire considérablement le temps de traitement.
- L'amélioration de l'optique permet un laser d'un diamètre de 100 μm et un laser de focalisation fine de 50 μm pour le traitement de structures encore plus petites.
HARTING est le seul fabricant de 3D-MID au monde qui dispose d'un système laser à trois optiques pour une mise au point fine de 50 μm. Grâce au laser à mise au point fine, des distances de pistes conductrices encore plus petites sont atteintes. De cette manière, un plus grand nombre de pistes conductrices peut être créé sur le même composant avec une densité de tassement plus élevée. Il est utilisé, entre autres, pour la technologie de sécurité car les pistes conductrices étroitement espacées et entrelacées déclenchent des alarmes de sécurité même avec la plus petite interférence physique.
Progrès matériels et économiques
Seuls les thermoplastiques sélectionnés sont certifiés pour le processus LDS et disponibles en stock. D'autres améliorations du processus concernent les adaptations spécifiques du matériau plastique de la part du client :
- HARTING utilise un procédé pour fabriquer des matériaux non certifiés compatibles MID avec les additifs LDS.
- L’ajout de pigments de couleur et d’additifs LDS spéciaux permet d’obtenir des couleurs RAL ou Pantone spécifiques avec des plastiques MID.
- En sélectionnant des additifs appropriés, des propriétés RF spéciales peuvent également être créées en fonction de la plage de fréquences.
Support de composants - Les composants électroniques sont montés directement sur le support à l’aide d’un processus automatisé. Les processus souvent complexes nécessaires à la fabrication de circuits imprimés flexibles sont supprimés, ce qui permet d’économiser deux tiers des coûts.
Pour optimiser davantage la rentabilité du processus de fabrication, HARTING mise sur l'automatisation avec des systèmes robotisés. Les systèmes laser LDS sont équipés d'une table d'indexation rotative afin qu'un composant puisse être inséré ou retiré pendant qu'un autre composant est encore en cours de traitement. L'alimentation et le déchargement sont automatisés chez HARTING grâce à la technologie robotique. Cela augmente le débit et l'autonomie et permet l'intégration dans des processus de production automatisés. Le prestataire de services ajout une étape d'automatisation dans le processus de moulage par injection. Même dans ce cas, un robot est prévu pour le retrait des pièces moulées par injection. L'utilisation de robots augmente également la reproductibilité exacte des processus tout en améliorant qualité du produit.
Poursuite de la croissance pour 3D-MID
Capuchons de sécurité pour les terminaux de paiement - Les capuchons de sécurité de HARTING protègent les informations de carte de crédit de toute lecture abusive. Les capuchons 3D-MID protègent l'électronique mécaniquement et électroniquement contre les accès non autorisés. Une structure d’interdigitation de haute précision détecte chaque intervention, aussi petite soit-elle, et empêche ainsi le vol de données.
HARTING fait face à de demandes croissantes pour les projets MID et a encore élargi la division 3D-MID en investissant dans le parc de machines et en reprenant les activités commerciales d'un concurrent. Des produits internes innovants contribuent également à sa croissance constante. HARTING a développé une solution qui se base sur la technologie 3D-MID et permet de remplacer les circuits imprimés flexibles par un support de composants. Ce même support peut être équipé directement de composants électroniques au lieu de la carte de circuit imprimé flexible, pour des économies allant jusqu'à deux tiers des coûts.
Dirk Rettschlag
HARTING AG
Project Manager & IE MID
Leugenestrasse 10
CH-2500 Biel 6
This email address is being protected from spambots. You need JavaScript enabled to view it.
HARTING.com/3D-MID
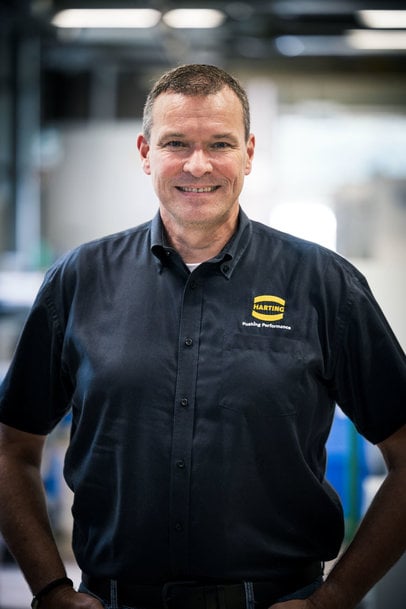