Une avancée majeure : comment les composants standardisés peuvent réduire le coût des investissements en équipements de production
La maintenance et le service des équipements représentent un des coûts les plus importants en production et fabrication. David Messant, Directeur de Production chez norelem, étudie comment des éléments standardisés peuvent faire baisser ces coûts et rendre les machines aussi « sans maintenance » que possible.
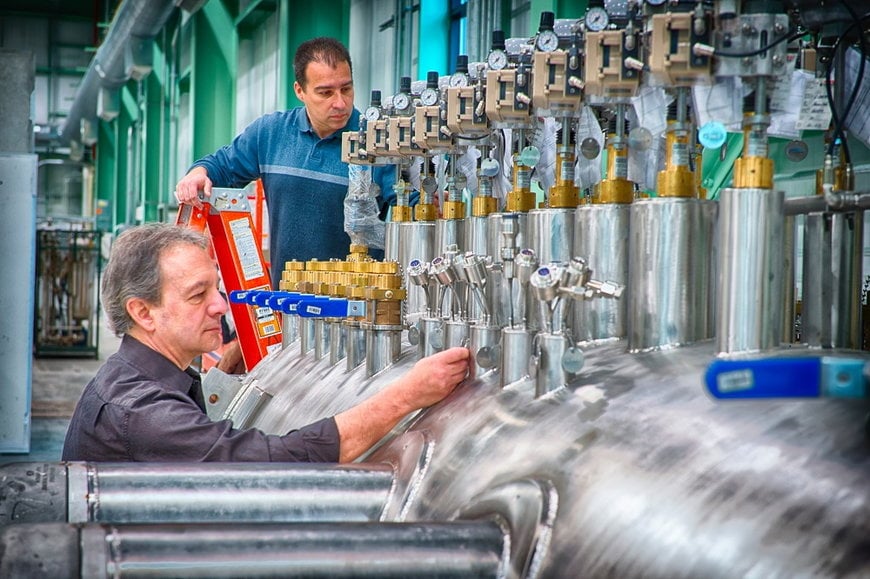
Il n’y a sans doute pas besoin de rappeler que la maintenance est primordiale. Dans certains cas, le coût de la maintenance pendant la durée d’utilisation de la machine peut dépasser le coût de l’investissement initial lui-même, si celle-ci n’est pas gérée correctement.
Dans le sondage In Plant Engineering’s 2018 Maintenance Survey 35% des personnes interrogées annonçaient dépenser plus de 10% du budget de fonctionnement en maintenance et 34 autres pourcents dépensaient entre 5 et 10% en maintenance.
Les entreprises ne peuvent guère se permettre de laisser leurs machines tomber en panne, ou de laisser un équipement en arrêt non planifié. Cela causerait une chute importante de productivité, de chiffre d’affaires et de bénéfice. Selon l’étude IndustryWeek les arrêts non planifiés en fabrication coûtent aux industriels environ 50 milliards de dollars par an et 42% sont dus à des pannes. Les arrêts imprévus ont pour conséquence l’augmentation des coûts de maintenance, de réparations et des remplacement d’équipement, de façon croissantes voire excessive La stratégie de maintenance « rouler jusqu’à la panne » est clairement empreinte de risques. Par conséquent, il existe deux stratégies principales pour réduire ces coûts, la maintenance préventive et la maintenance prédictive.
Deux approches contratées de la maintenance
La maintenance préventive a longtemps été la méthode pour garder les machines en état et produire. Cette stratégie tourne donc autour de l’entretien des machines et de leurs composants à des intervalles réguliers afin de les prémunir contre toute panne imprévue.
Pendant que le risque de panne est fortement réduit, choisir la maintenance préventive signifie que vous devez assurer l’entretien des machines, et ceci représente un recours important aux opérateurs pour des contrôles réguliers indispensables.
D’un autre côté, la maintenance prédictive, qui n’est pas nouvelle, a récemment augmenté grâce aux avancées rapides en Industrie 4.0, technologies connectées et IIOT (Internet Industriel des Objets). En utilisant des capteurs et des systèmes, les ingénieurs peuvent désormais collecter de grandes quantités de données sur tout équipement, des cycles et des températures de fonctionnement aux vibrations et bruits. Recourir à cette approche rend possible de prédire si un composant doit être remplacé sur une machine, ou si la machine doit être entièrement retirée du service à cause d’anomalies dans les données.
Le revers de la médaille est que la mise en place d’un système de maintenance prédictive peut être coûteux au départ, à cause du besoin d’un système IOT complet, de capteurs et de logiciels de contrôle, et de la formation des équipes à l’analyse des données. Quel que soit le chemin choisi pour maintenir vos équipements, toutes les machines peuvent bénéficier d’éléments standardisés pour réduire les coûts et rendre la maintenance plus efficace.
Standardiser la maintenance des machines grâce à des composants standard
Un des plus grands défis de la maintenance est d’avoir à disposition des équipes avec les compétences nécessaires pour assurer les tâches de maintenance requises. Il est largement reconnu qu’il existe un déficit de compétences en fabrication mécanique, et de moins en moins d’entreprises ont des équipes dédiées à la maintenance sur site, tout simplement parce que trouver les talents et les retenir est une tâche ardue. Le sondage de Plant Engineering révèle que 16% des sondés n’externalisent pas leur maintenance, 44% d’entre eux externalisent jusque 20% de leur maintenance totale et 10% recourent à des tiers pour au moins 50% de leurs besoins. Le manquede compétences en estla raison principale.46% des sondés par Plant Engineering déclarent qu’il existe un manque de compétences dans leurs équipes existantes. Cependant 46% déclarent également que la maintenance moderne nécessite davantage de connaissances spécialisées.
Il est clair que les machines deviennent plus complexes, mais en utilisant des composants standard dans la construction des machines, ce déficit de compétences peut être minimisé. En raison des dimensions et des versions standardisées, les opérateurs n’ont pas besoin de posséder des connaissances préalables pour des composants spécifiques et peuvent aisément remplacer ces composants si besoin est.
Sélectionner des composants sans entretien
L’idéal pour toute machine est d’être sans entretien et de ne nécessiter aucune maintenance du tout. Cela peut sembler étonnant. Les opérateurs savent que l’usure est parfaitement normale, car l’environnement industriel cause t une accumulation de poussières, de débris et de saletés. Toutefois, certains éléments des machines peuvent être réalisés avec des composants sans entretien afin d’aider à réduire les coûts de réparations.
Exemple : l’utilisation d’engrenages et de pignons coniques.
Traditionnellement, ces engrenages sont réalisés en acier (coûteux à changer). Désormais, des versions en matière plastique de ces engrenages sont disponibles et norelem propose une gamme de ces composants légers et résistants à la corrosion, n’ayant besoin que de peu ou pas de maintenance. Autolubrifiants, ces engrenages sont très silencieux en opération et peuvent être utilisés dans une vaste variété d’applications, et apporter un bon rapport prix performance, les rendant très économiques. Il existe toute une famille de composants sans entretien dans l’offre de norelem. Les douilles de guidage par exemple sont aussi des composants largement utilisés en ingénierie et norelem en propose une version réalisée en bronze avec des inserts en graphite. L’insert en graphite assure une lubrification à vie. C’est seulement sous des charges extrêmes et des vitesses élevées qu’une lubrification additionnelle est recommandée.
Composants standard, performances extraordinaires
Un dernier moyen pour réduire les besoins en maintenance des équipements est de choisir des composants pouvant offrir de hautes performances et de la qualité. Cela est particulièrement important pour les pièces soumises à des charges, forces et des efforts élevés. Une illustration parfaite en est le mouvement linéaire avec des pièces travaillées lourdes.. Pour ce type d’application, il est recommandé que les actionneurs linéaires soient utilisés avec de larges supports mobiles, afin qu’ ils puissent absorber les charges élevées dans toutes les directions. Les gammes de produits norelem incluent des actionneurs linéaires dans des longueurs standardisées avec des courses de n200 à 1500 mm, tandis que des longueurs sur demande sont livrables pour des projets spécifiques.
Dans les secteurs des matériaux, de l’emballage ou de l’agro-alimentaire, les opérateurs peuvent aussi voir leurs coûts de maintenance exploser, à cause de fonctionnalités requises qu’ils doivent prendre en charge. Habituellement des chaînes à rouleaux et des pignons sont montés sur ces machines, mais en substituant des chaînes à rouleaux doubles ou triples, les coûts et temps de maintenance seront fortement réduits. Les performances d’une chaîne à rouleaux doubles sont 1,75 fois meilleures que celles d’une chaine simple, tandis qu’une chaine à rouleaux triples offrira 2,5 fois mieux. Une offre complète de ces éléments, accompagnés des pignons et des galets tendeurs correspondants sont disponibles dans THE BIG GREEN BOOK, le catalogue général de norelem qui contient 60 000 composants, informations techniques et plans.
Limiter les délais de fabrication et les temps d’arrêts imprévus
Pour faire baisser les coûts de maintenance, il faut commencer par prévoir les zones et constituants de la machine où une maintenance régulière sera requise. De cette manière et en construisant les machines avec des composants standardisés quand c’est possible, les entreprises peuvent commencer à relever les défis classiques associés avec la discipline de la fabrication mécanique. En n’ayant pas besoin de techniciens expérimentés pour assurer la maintenance et en possédant des composants sans entretien et de qualité, les entreprises verront graduellement baisser le budget d’entretien de leurs équipements. En outre, les éléments standardisés pourront aider à faire chuter les temps d’arrêt imprévus. norelem tient en stock 98 % de ses composants, avec des fiches de données et des fichiers CAO pour chacun d’entre eux. Cela implique que les éléments qui s’useront de façon inopinée pourront être remplacés rapidement et que les usines comme la production ne seront pas arrêtées longtemps.
Pour en savoir plus sur norelem, visitez www.norelem.fr.