www.industrieweb.fr
14
'14
Written on Modified on
Efficacité énergétique : la Compagnie des Fromages mise sur l’innovation avec les technologies d’Emerson.
La filiale du Groupe Bongrain s'est engagée dans la réduction des coûts énergétiques et des émissions de CO2 en investissant dans une installation conçue par Cofely Axima, un leader du froid industriel appartenant au groupe GDF Suez. Cette solution se distingue par la mise en place d’un processus produisant dans un même cycle du chaud et du froid et par l’utilisation de composants clés fournis par le Groupe Emerson : un compresseur à vis unique Vilter, d'Emerson Climate Technologies, et un système d’entraînement à vitesse variable Leroy-Somer, d’Emerson Industrial Automation.
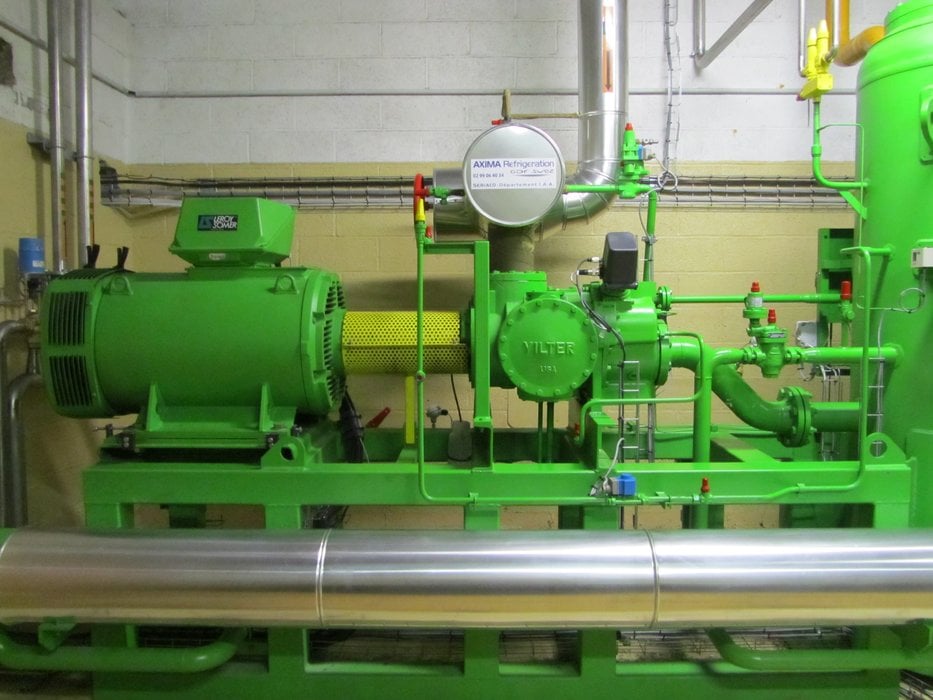
La compagnie des Fromages fait partie du groupe Bongrain, le cinquième transformateur mondial de lait avec 18870 collaborateurs.
« Nous avons un rôle de conseil auprès de nos clients. C’est ainsi que nous avons lancé un audit énergétique avec l’usine de Vire de la Compagnie des Fromages », explique Jean-Yves Druillennec, Directeur du Développement Durable, au sein de Cofely Axima GDF Suez. Basée sur une campagne de mesures, cette étude a permis de dresser un bilan des consommations et de proposer l’installation d’une thermo-frigo-pompe en lieu et place de 4 compresseurs à pistons qui ne produisaient que du froid.
Une thermo-frigo-pompe est un système thermodynamique de transfert d’énergie permettant de produire simultanément le froid et le chaud. Le système frigorifique permet de fournir au même instant une puissance frigorifique à l'évaporateur et une puissance thermique au condenseur. A Vire, quand on réfrigère 1000 kW d’eau glacée, on récupère dans le même processus une quantité d’énergie de 1300 kW servant à chauffer de l’eau à +62°C, le tout pour une consommation électrique supplémentaire de 100 kW. Toutes énergies produites et consommées sont intégralement récupérées : 0 rejet d’énergie. Une unité de stockage tampon d’énergie de 150 m3 permet de lisser l’utilisation d’eau chaude suivant les besoins du processus (notamment nettoyage). Auparavant, cette eau était chauffée par le gaz, d’où un bilan carbone nettement amélioré. Par ailleurs, la chaleur produite et non récupérée, était évacuée par le biais d’une tour de refroidissement. Le nouveau système permet ainsi d’économiser 9000 m3 par an en consommation d’eau et a diminué l’usage de la tour de refroidissement, qui a toujours une image négative vis à vis des riverains qui voient une fumée s’échapper de l’usine.
Dans le détail, l’installation comprend un moteur 390 kW et un variateur, tous deux de marque Leroy-Somer. Ceux-ci entraînent un compresseur à vis unique de la marque Vilter d’une capacité frigorifique de 1000 kW. Dans la logique environnementale, le fluide frigorigène utilisé dans l’installation est l’ammoniac (NH3), fluide frigorigène naturel couramment utilisé dans ce cas. Pendant un tiers du temps, le froid et le chaud sont produits simultanément. Pour chauffer l’eau de 15°C à 58°C (avec un COP* mixte de 7.67), l’ammoniac, après avoir extrait la chaleur du côté froid pour la production d’eau glacée, doit être comprimé afin d’obtenir la pression et la température adéquates. Cette température est bien supérieure à la température habituelle pour une installation de refroidissement classique. L’ammoniac condense dans ce cas à 59°C. La chauffe de l’eau est réalisée en transférant la chaleur de l’ammoniac via le condenseur et d’autres échangeurs de chaleur disposés dans l’installation pour optimiser la récupération de chaleur.
Le tiers du temps restant, la production d’eau glacée se fait de manière classique tout en fournissant un COP de 5.75. A terme, l’installation permettra de récupérer 100% de la chaleur extraite lors de la production de l’eau glacée.
Un retour sur investissement en 18 mois
La production quotidienne de l'eau glacée de 1 à 7 ° C et celle de 200 m3 d'eau chaude à 60 ° C nécessitaient une consommation d'énergie annuelle moyenne de 820 kW par tonne de production. Aujourd’hui, cette consommation a été réduite à 560 kW. « Le retour sur investissement est ainsi particulièrement court, même si ce calcul est fait en tenant compte d’aides à hauteur de moins de 20% du financement », explique Patrick Marie, responsable de la Maintenance pour la Compagnie des Fromages. « Mais le gain énergétique ne se situe pas uniquement au niveau du processus qui permet de produire du chaud avec une moindre consommation supplémentaire, mais elle réside aussi dans l’utilisation de composants bien moins énergivores », précise Jean-Yves Druillennec.
Une motorisation Dyneo® à haut rendement et haute fiabilité
LSRPM de la gamme Dyneo® est une série de moteurs synchrones à aimants permanents qui bénéficie de la technologie brevetée Leroy-Somer. La conception innovante du rotor à aimants permet une augmentation significative du rendement qui atteint ainsi des taux proches de 98%.
« Nous constatons un gain d’énergie de 7% par rapport aux moteurs asynchrones à haut rendement. C’est un avantage très significatif en matière de rentabilité, surtout lorsque l’on sait que le coût de l’énergie électrique devrait augmenter de 25% au cours des 5 prochaines années. Ce moteur se distingue en étant idéal pour la variation de vitesse. On a remarqué que certains moteurs asynchrones étaient sollicités de manière excessive en régime variable. Avec Leroy-Somer, nous n’avons pas ce problème. Les moteurs restent fiables quelle que soit la charge appliquée. L’usage d’un moteur asynchrone nous aurait amenés à utiliser un moteur surdimensionné ».
Par ailleurs, les faibles pertes de la technologie rotor à aimants limitent considérablement l'échauffement des roulements. Cela diminue d'autant la fréquence d'intervention pour leur graissage et augmente la durée de vie du moteur. « Nous avons mis en œuvre plus de 30 applications sur 4 ans sans rencontrer le moindre problème », ajoute Jean-Yves Druillennec.
La technologie Vilter pour une fiabilité et une efficacité énergétique accrues
Vilter est une marque d’Emerson Climate Technologies qui compte plus de 16 000 personnes dans le monde. A l’inverse des compresseurs standard à double vis, la société utilise un procédé très différenciant : les compresseurs à vis unique, Single Screw Vilter. La compression est réalisée sur une unique vis à l’aide de deux rotors satellites en étoile. Grâce à la conception du compresseur, la vis unique est équilibrée radialement et axialement. Cet équilibrage assure des charges très basses sur les paliers, et ainsi une grande fiabilité, le tout avec des niveaux de vibration et de bruit considérablement réduits. Cette conception permet à Vilter de proposer une garantie exclusive dite « 5/15 » : 5 ans pour le compresseur et 15 ans pour les paliers.
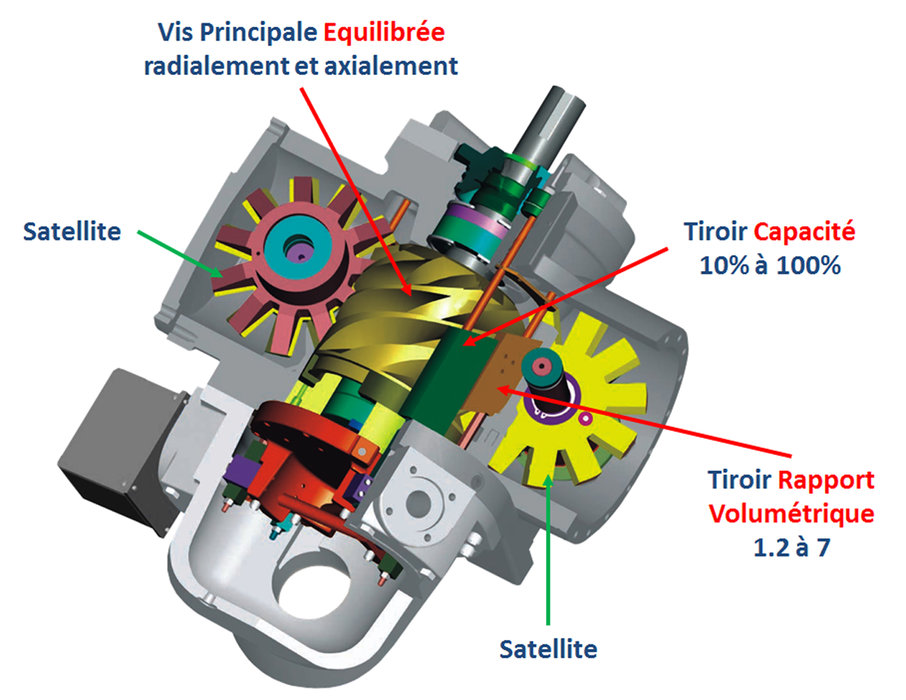
La clé du rendement élevé du compresseur à simple vis Single Screw réside dans le système à tiroirs Parallex™, une exclusivité de Vilter, qui permet au compresseur de fonctionner à un rendement optimal sur toute sa gamme de puissance. Les tiroirs de réglage du volume et du débit (avec un rapport volumétrique étendu de 1,2 à 7) se déplacent indépendamment l’un de l’autre quelles que soient les conditions opératoires. Ils éliminent de la sorte tout surrégime ou sous-régime de compression et économisent la puissance du moteur. « Ces compresseurs se distinguent par leur possibilité de régler la capacité et le rapport volumétrique de manière indépendante. Cela crée une réelle différence en cas de fonctionnement en charge partielle. Avec les compresseurs Vilter, nous avons toujours mesuré un écart net en matière d’efficacité énergétique qui, selon les applications, peut atteindre jusqu’à 10% par rapport à la technologie standard à double vis», explique Jean-Yves Druillennec.
Il faut privilégier le coût global
Cofely Axima a été responsable de la gestion complète du projet : ingénierie, installation, régulation et supervision (gestion par automate, suivi instantané des performances et traçabilité de tous les paramètres). Seul le câblage électrique est réalisé par des sous-traitants. A noter, que le processus de la Compagnie des Fromages n’a été arrêté que 3 heures lors de la mise en route. Cofely Axima multiplie les installations internationales comme en Thaïlande, au Koweït ou en Italie. « Nous subissons une pression sur les prix. Un client ne sera intéressé par une solution que si le retour sur investissement est inférieur à deux ans. Il est important de pouvoir s’engager en toute sécurité. Au global, les solutions Emerson offre un meilleur rendement, une meilleure fiabilité, et ils offrent une bien meilleure flexibilité pour les régimes variables. L’ensemble permet de créer une réelle différence sur le coût global », conclut Jean-Yves Druillennec.
* Le COP (Coefficient Of Performance) représente la performance énergétique de la machine et correspond au rapport entre la puissance thermique restituée et la puissance électrique consommée. Plus le COP est élevé, plus la facture d’électricité est diminuée.
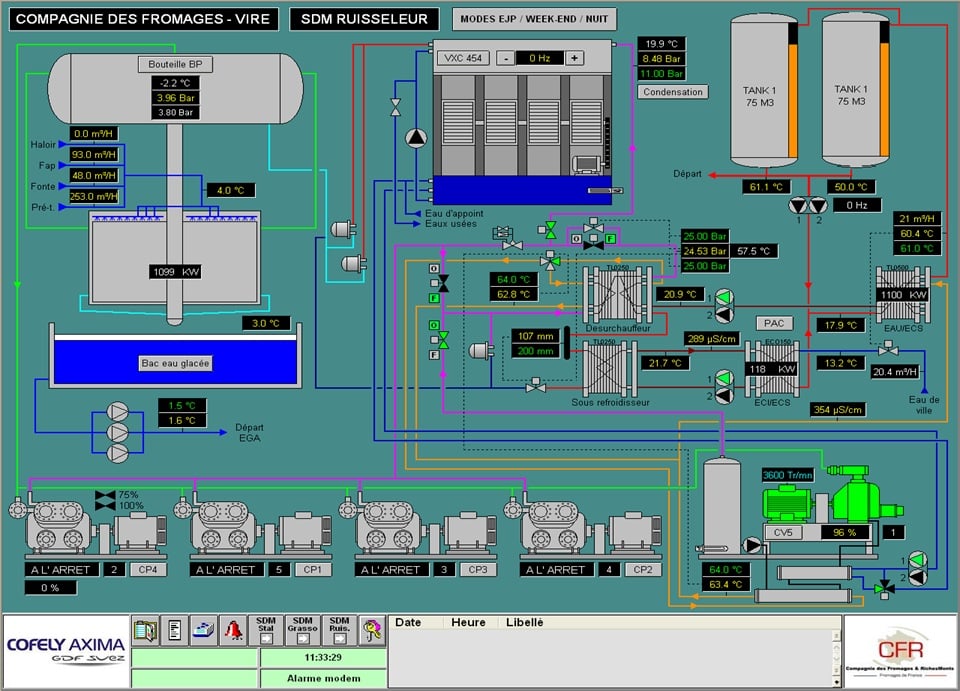
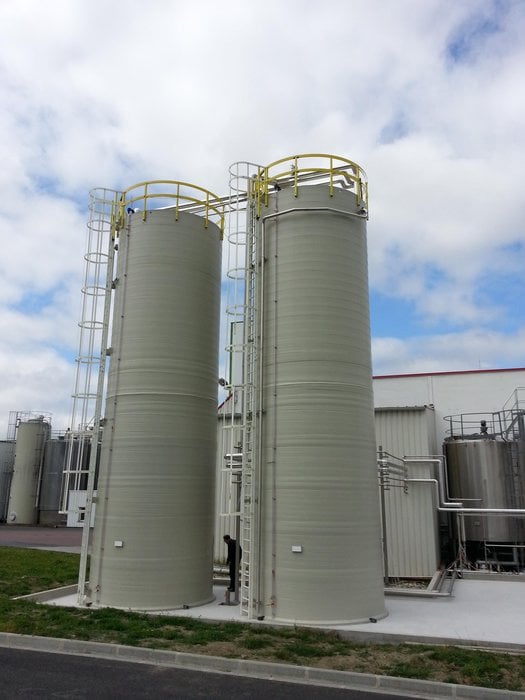
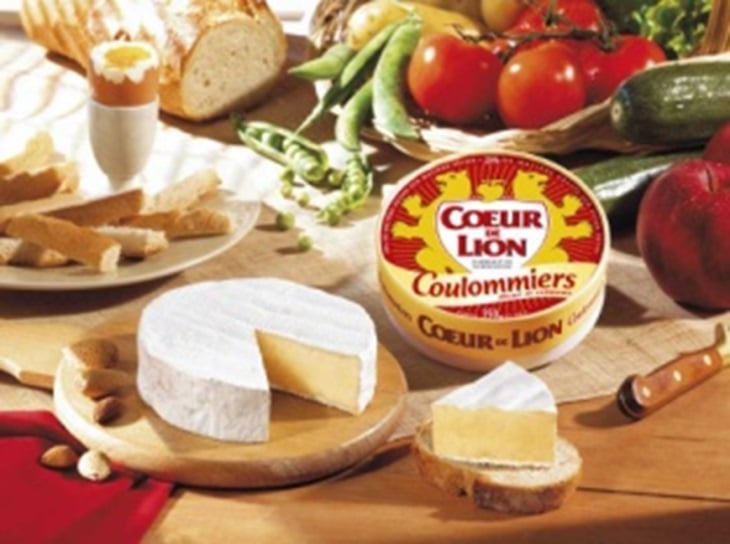
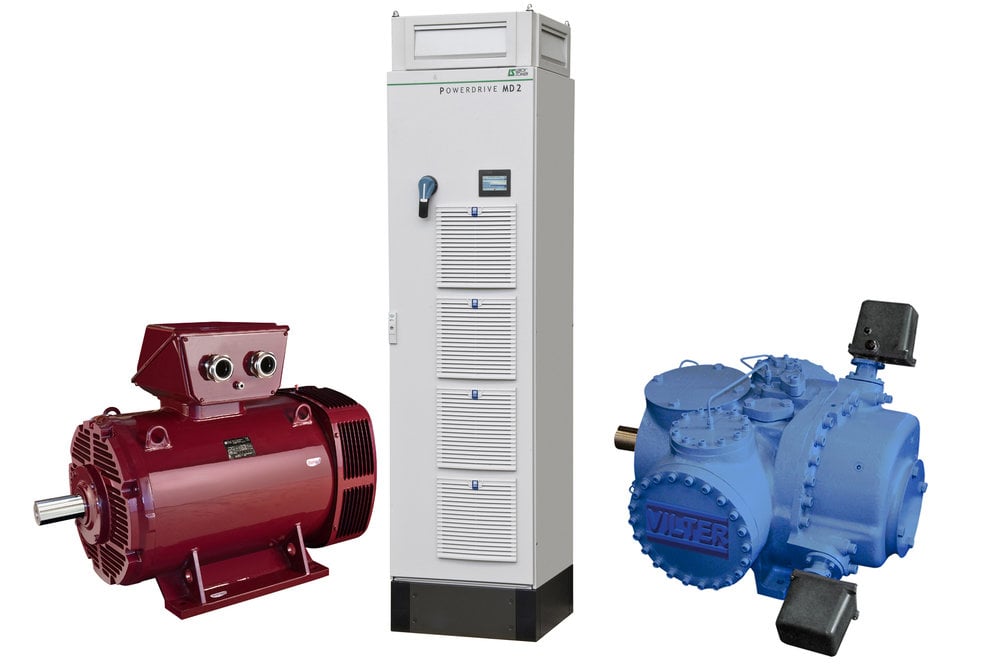