Pas le droit à l’erreur!
Les modules PROFIBUS et les radios industrielles ProSoft Technology garantissent la transmission de données critiques via les automates Rockwell Automation ControlLogix utilisés dans le cadre d'un système de protection contre les inondations. Le remplacement du système de contrôle d’un barrage anti-inondation est problématique. En effet, un dysfonctionnement pourrait provoquer une catastrophe pour des milliers de logements, d'entreprises et de personnes.
La rénovation d'un barrage anti-inondation nécessite des mois de travaux car ce dernier doit rester fonctionnel pendant celle-ci. La conception du projet doit donc être minutieuse pour garantir un niveau de sécurité maximal. Des mesures de prévention des pannes et des solutions de secours doivent être mises en place. Il suffit d’ailleurs de se rendre une fois sur un barrage anti-inondation pour être convaincu que de tels systèmes de sécurité sont essentiels.
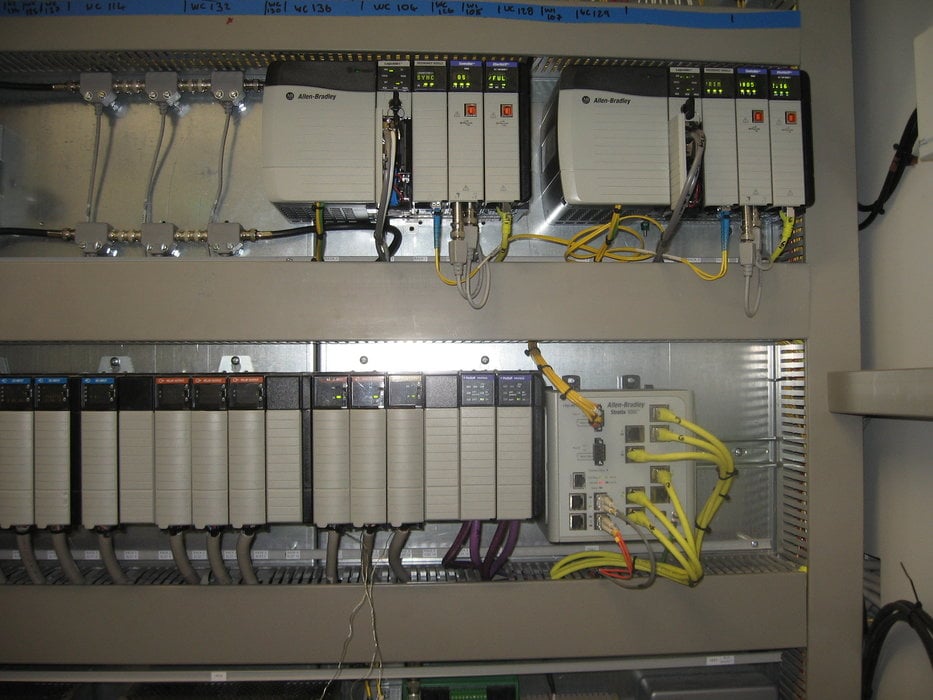
Deux tours de béton de 20 mètres de haut s'élèvent de chaque côté de l'embouchure de Dartford Creek au Royaume-Uni. C'est là, dans la région du Kent, que se trouve le système de protection contre les inondations de l’Agence Britannique pour l’Environnement. Celui-ci est régulièrement fermé en parallèle avec le plus grand barrage de la Tamise qui se trouve en amont, afin d'empêcher toute inondation dans la région de Dartford et de ses environs en cas de crue dans l'estuaire de la Tamise.
Deux portes en acier de 30 m de long et pesant plus de 160 tonnes, sont suspendues entre deux tours en béton. Une porte peut être abaissée sur le lit de la rivière afin d'empêcher le passage de l'eau, telle une guillotine géante installée sur l'embouchure de la crique. La seconde porte peut ensuite être abaissée pour reposer par-dessus la première. Quand les deux sont fermées, elles peuvent résister à une crue de 10,4 m.
Les portes sont actionnées via des moteurs hydrauliques. Le système de contrôle est composé de deux unités pompe/moteur de 18,5 kW, chacun avec capacité de service et de secours, qui permettent d'abaisser et de relever chaque porte en 15 minutes. Lorsqu'elles ne sont pas en service, la structure de chaque porte est maintenue en position totalement relevée et est verrouillée grâce à des mécanismes hydrauliques. Les bateaux peuvent ainsi circuler sous les portes le long de la crique.
En raison des changements climatiques, il a été calculé que le barrage devrait être actionné en moyenne 50 fois par an au cours des 25 prochaines années.
« Le système doit être très performant et disposer de plusieurs systèmes de secours en cas de panne », explique Andrew Garwood, Senior Contracts Manager de la division « Contrôles » de Qualter Hall & Co Limited, une société basée à Barnsley.
Il y a quelques années, le système de contrôle d'origine, qui avait plus de 30 ans, a commencé à montrer des signes de fatigue. Une mise à niveau du barrage devait être effectuée. La difficulté de se procurer les pièces de rechange a été à l’origine de la décision de remplacer ce système composé exclusivement de relais câblés.
Qualter Hall a réalisé les travaux de surveillance et d'évaluation pour le compte de l'entrepreneur principal Birse Civils, en qualité d'intégrateur système du projet et de sous-traitant en génie mécanique et électrique en charge du remplacement du système de contrôle. Plusieurs objectifs ont été établis, en premier lieu la fiabilité et la sécurité du projet. Une inondation aurait en effet provoqué des dégâts considérables dans les environs.
Qualter Hall, qui propose une multitude de solutions d'ingénierie, a décidé de faire appel à ProSoft Technology en raison de la fiabilité et de la rentabilité de sa solution, approuvée par Rockwell Automation. ProSoft Technology est en effet partenaire Encompass de Rockwell Automation.
Deux automates ControlLogix Rockwell Automation redondants sont situés à l'intérieur de chaque tour pour contrôler l'ouverture et la fermeture du barrage, mais la plupart des équipements avec lesquels le système de contrôle communiquait utilisaient le protocole PROFIBUS ou des automates programmables industriels Siemens. Deux modules maîtres de communication PROFIBUS (MVI56-PDPMV1) ProSoft Technology furent installés dans les automates ControlLogix pour faciliter les communications avec entre les processeurs Rockwell Automation et le système Siemens.
« Les modules de ProSoft Technology ont été utilisés pour permettre au rack ControlLogix d'utiliser le protocole PROFIBUS-DP. Ils permettent d'utiliser quatre segments PROFIBUS-DP distincts afin d'obtenir un fonctionnement redondant », précise Andrew Garwood.
De la fibre optique a été installée entre les deux tours dans le cadre du remplacement du système de contrôle. Pendant la construction des liaisons câblées, des radios points d'accès sans fil industriels 802.11 ProSoft Technology ont été utilisées pour la liaison de communication.
« Nous avons ensuite employé cette liaison sans fil comme connexion de secours automatique en cas de perte de la connexion fibre optique. Nous avons choisi les équipements ProSoft Technology en raison de leur fiabilité et leur prise en charge du protocole RSTP », ajoute Andrew Garwood.
Les solutions ProSoft Technology ont contribué à faciliter le travail de conception, en permettant au système ControlLogix de communiquer via un seul protocole.
Désormais, le système permet de consulter les données rapidement, de manière centralisée et à distance, et facilite l'accès aux informations de diagnostic.
Des milliers de foyers, de personnes et d'entreprises sont ainsi protégés de manière sûre.
Pour d'autres cas d’applications, consultez notre site web.