www.industrieweb.fr
09
'22
Written on Modified on
AVANTAGES DES TUBES COMPOSITES A PAROI FINE
Les tubes à paroi fine sont généralement en métal, afin d'assurer la rigidité et la résistance voulue pour certaines applications à un prix abordable. Jusqu'à présent, les composites en fibre de verre ne permettent pas de remplacer le métal, car bien que plus légers, ils n'offrent pas la rigidité voulue.
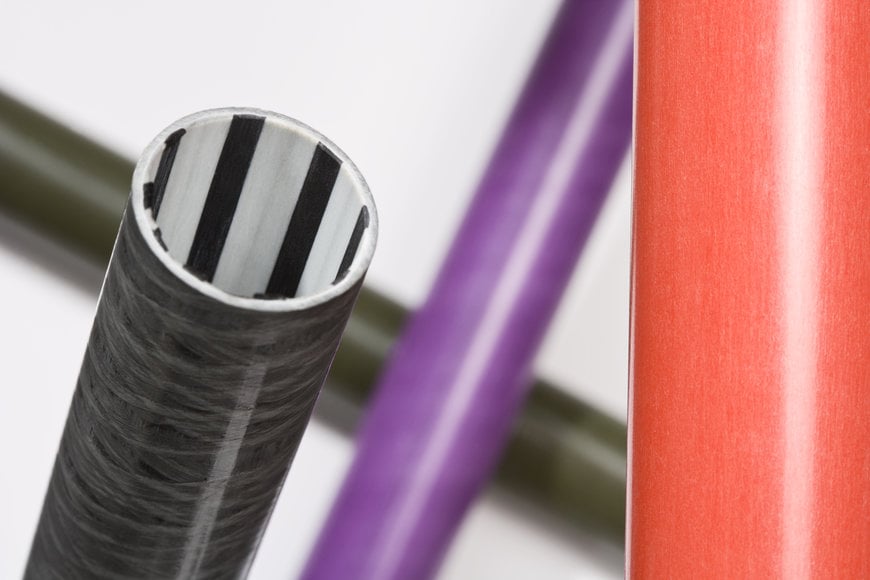
Les composites en fibre de carbone, quant à eux, offrent des capacités mécaniques comparables, mais sont considérés comme trop onéreux. Dans cet article, Patrick Loock, responsable commercial produits et applications chez le fabricant de tubes composites Exel Composites, explique pourquoi les fabricants doivent envisager d'utiliser des matériaux composites, notamment en raison des progrès réalisés dans les technologies hybrides personnalisées.
Le plus souvent, les matériaux composites à paroi fine ont une épaisseur comprise entre 0,9 et 2 mm, et interviennent dans de nombreuses applications appartenant à des secteurs très divers, tels que les tripodes d'appareils photo, les manches télescopiques pour lave vitre, les équipements d'IRM, les pieds télescopiques et les piquets de soutien de filets de camouflage.
Auparavant, ce type d'objet était fabriqué en acier ou en aluminium. Toutefois, les exigences de durabilité et de réduction du poids poussent les industriels à réaliser des gains d'efficacité permettant de réduire le poids sans compromis sur les propriétés mécaniques. Cela est particulièrement évident au stade de la conception, lorsqu'il nous est demandé comment remplacer les métaux pour ce type d'application.
Propriétés mécaniques réglables
La rigidité est un facteur clé pour les tubes à paroi fine destinés aux applications industrielles. L'aluminium, qui est le matériau le plus utilisé, a une épaisseur de 70 gigapascals (GPa). La fibre de verre, qui est le choix le plus courant pour les solutions composites en raison de sa légèreté et de son prix relativement faible, assure un gain de poids indéniable à dimensions égales, mais sa rigidité n'est que de 35 GPa. Par conséquent, pour obtenir une valeur de rigidité comparable à celle de l'aluminium, il faut des tubes plus épais et donc plus lourds.
Les composites en fibre de carbone cochent toutes les cases en termes de propriétés mécaniques. Ils sont non seulement beaucoup plus légers que le métal, mais aussi bien plus rigides, les tubes en fibre de carbone de base offrant une résistance de 120 Gpa, tandis que la version haut module peut atteindre 210 GPa. Cependant, les composites en fibre de carbone sont également environ cinq fois plus onéreux que les métaux. Et c'est là que les composites hybrides interviennent, car ils constituent un excellent compromis.
Les composites hybrides, ainsi appelés parce qu'ils combinent des fibres de verre et de carbone, permettent aux fabricants d'ajuster les propriétés mécaniques en fonction de l'application sans avoir à changer les dimensions des tubes ou poteaux, en modulant la proportion de fibres de verre et de carbone dans la structure. Par exemple, un manche de lave vitre peut être principalement en fibre de verre pour les bâtiments à deux étages ou surtout en fibre de carbone, pour plus de rigidité, en cas d'immeuble à cinq étages. Tout partenaire sérieux et expérimenté pourra vous conseiller comment produire les matériaux les mieux adaptés à votre application.
Avantages de la fabrication en pull-winding à grande échelle
Pour produire des matériaux composites en grande quantité à un prix abordable, des processus de fabrication continue, tels que la pultrusion et le pull-winding, sont avantageux, car ils garantissent une production haute qualité constante et une excellente répétabilité. Le pull-winding est particulièrement intéressant pour la fabrication de matériaux composites, car il assure un contrôle omnidirectionnel des propriétés mécaniques, ainsi qu'un renforcement sélectif des tubes composites à paroi fine, ce qui élimine les déchets et réduit les coûts autant que possible.
Pour ce faire, il combine l'alignement unidirectionnel des fibres à l'enroulement hélicoïdal des renforts, ce qui permet de contrôler les deux, que ce soit sur quelques degrés ou jusqu'à 90°.
D'autres techniques de fabrication sont possibles pour les tubes en composites à paroi fine, telles que l'enroulement filamentaire, toutefois elles nécessitent davantage d'étapes manuelles et sont mieux adaptées pour les tubes épais à grande section. D'autre part, parce qu'ils nécessitent davantage d'interventions manuelles et ne peuvent se réaliser qu'en faible volume, les tubes à paroi fine réalisés par enroulement filamentaire sont généralement plus chers.
En travaillant avec un partenaire expérimenté et compétent, qui comprend les exigences de votre application et les défis opérationnels, vous avez la garantie d'une solution optimale. Exel Composites a plus de 40 ans d'expérience dans la fabrication de tubes composite à paroi fine et se tient à votre disposition pour développer une solution composite hybride adaptée à votre application, afin de réduire le poids sans faire de compromis sur les performances mécaniques.
Pour plus d'informations sur les tubes en matériaux composites à paroi fine, voir https://exelcomposites.com/composite-solutions/equipment-and-other-industries/composite-tubes/
www.exelcomposites.com