3D Systems et Airbus Defence and Space créent des composants RF passifs inédits pour le premier satellite entièrement reconfigurable
3D Systems a annoncé aujourd'hui avoir été sélectionné par Airbus Defence and Space pour produire des composants essentiels destinés à son satellite innovant OneSat.
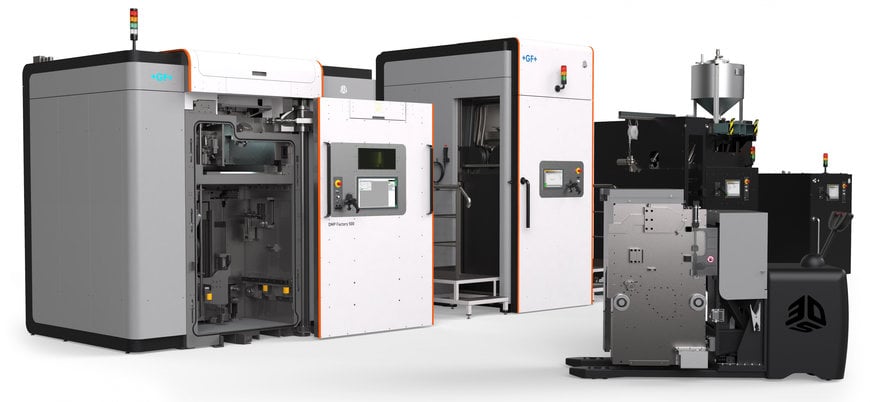
- Le savoir-faire et la technologie de 3D Systems autorisent le développement d'un vaste réseau d'antennes pour OneSat, le premier satellite entièrement reconfigurable en orbite
- Les entreprises signent un contrat de plusieurs années pour le développement d'antennes destinées à l'ensemble du parc de OneSat
3D Systems a été choisi pour cet important projet en raison de la qualité des pièces obtenues avec ses systèmes DMP ainsi que pour les performances et le savoir-faire apportés dans le cadre de sa collaboration avec Airbus Defence and Space au cours des sept dernières années. Cette collaboration de longue date a notamment débouché sur la production du premier filtre radiofréquence (RF) imprimé en 3D, testé et validé pour une utilisation dans des satellites de télécommunications commerciaux, ainsi que de systèmes innovants de réseaux d'assemblage de commutateurs destinés à deux engins spatiaux Eurostar Neo dans le cadre du premier déploiement à grande échelle de produits RF utilisant l'impression directe de métal.
Chaque satellite OneSat nécessite deux grands réseaux d'antennes, l'un pour transmettre les signaux et l'autre pour les recevoir. La solution DMP Factory 500 de 3D Systems sera utilisée pour la production en série des composants de l'antenne en LaserForm AlSi10Mg avec des paramètres spécialement développés par l'AIG pour atteindre l'épaisseur de couche requise de 30 µm. La DMP Factory 500 a été choisie pour ce projet en raison de son volume de fabrication (500 mm x 500 mm x 500 mm), de sa précision et de sa vitesse d'impression. La configuration multi-laser intelligente de cette imprimante permet de produire des pièces de grande taille sans soudure, avec une qualité de surface optimale et des propriétés de matériau exceptionnelles.
L'imprimante comprend une chambre à vide unique qui permet d'obtenir la plus faible teneur en oxygène possible (O2) dans la chambre de fabrication. Ceci a pour effet de préserver la composition chimique et de réduire la teneur en humidité des alliages de poudre métallique pendant la fabrication. Ceci garantit l'obtention de conditions de fonctionnement optimales pour des pièces de qualité constante (par exemple en termes d'uniformité des propriétés mécaniques et de la surface), une caractéristique indispensable dans un secteur aux exigences de qualité et de précision élevées. La DMP Factory 500 comprend également 3DXpert® qui prend en charge chaque étape du workflow de fabrication additive, de la conception jusqu'au post-traitement, pour passer rapidement et efficacement d'un modèle 3D à des pièces imprimées de qualité.
Outre son savoir-faire en matière de conception et de production, l'Application Innovation Group de 3D Systems assure aussi la gestion de projet. La société a identifié les sous-traitants en charge du post-traitement et du contrôle qualité pour apporter à Airbus Defence and Space la solution de bout en bout dont il avait besoin pour atténuer les risques et réduire les délais de commercialisation. L'AIG dirige également le processus de transfert technologique qui permettra à un autre fournisseur de niveau 1 de faire passer la production de ces composants entièrement qualifiés à la vitesse supérieure. Le fournisseur achète également une autre DMP Factory 500 pour compléter son parc et atteindre les niveaux de qualité exigés par Airbus.
« Notre partenariat de longue date avec Airbus Defence and Space est très important pour nous, et nous sommes heureux de constater que le travail que nous réalisons ensemble continue de porter ses fruits dans le secteur des satellites de télécommunications », déclare Michael Shepard, vice-président du segment aérospatial et défense de 3D Systems. « Comme c'était déjà le cas lors de notre première collaboration avec Airbus pour produire le premier filtre RF par fabrication additive, nous sommes une nouvelle fois en mesure de réaliser une « première » qui changera le secteur des télécommunications. Notre AIG a réalisé le travail préparatoire nécessaire au développement de l'application de ce composant et au transfert technologique. Nous sommes fiers que la technologie de 3D Systems puisse contribuer à la mise en place par Airbus d'une solide chaîne d'approvisionnement dédiée à la production en série de matériel RF passif ».
« OneSat est un produit véritablement révolutionnaire, et nous voulions que notre processus de conception et de fabrication présente ce même niveau d'innovation », déclare Stephen Phipps, responsable du programme d'antenne OneSat chez Airbus Defence and Space. « Notre entreprise entretient un solide partenariat avec 3D Systems et a pu s'appuyer sur son équipe d'ingénieurs en applications pour donner vie aux conceptions les plus avancées. Tous les aspects, de la qualité des pièces imprimées jusqu'à la qualification des pièces, en passant par la gestion de la qualité et la gestion globale du projet, ont aidé Airbus Defence and Space à conserver sa position de leader. »
www.3dsystems.com