www.industrieweb.fr
25
'22
Written on Modified on
AddUp et Dassault Aviation : vers un atelier automatisé de fabrication additive pour l’aéronautique
AddUp et Dassault Aviation collaborent pour faire passer les procédés de fabrication additive métallique d’un statut de « prototypage » à celui de « production en série » pour l’aéronautique. Pour y parvenir, la technologie additive doit être optimisée afin de démontrer ses capacités en termes de qualité, de reproductibilité et de productivité, pour envisager une production en série de pièces métalliques qui seront ensuite intégrées dans des avions.
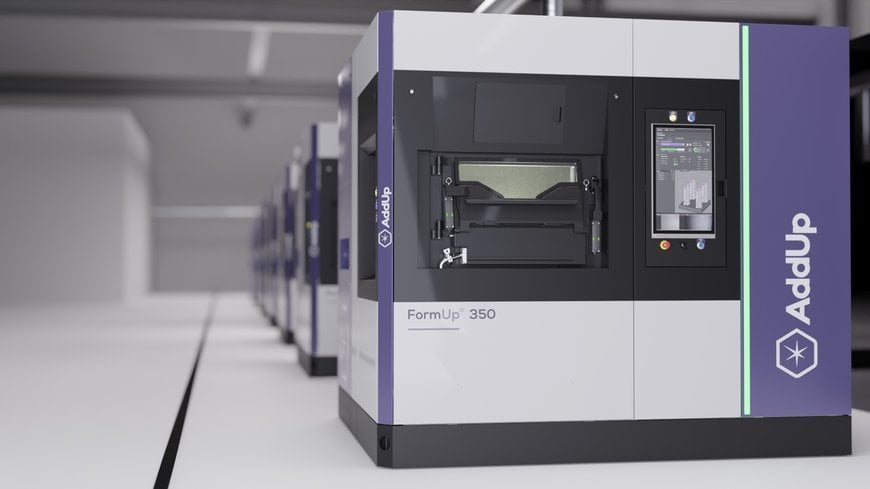
Nombreux sont les défis que la filière aéronautique doit relever afin de maintenir et accroître sa compétitivité : trafic aérien mondial croissant, raréfaction des matériaux, allégement et optimisation des pièces, recherche de fiabilité pour une meilleure qualité et respect des réglementations de plus en plus exigeantes, sont autant de problématiques à résoudre actuellement. Une des réponses à ces enjeux est l’utilisation de l’impression 3D métallique dans des conditions de production à l’échelle industrielle.
C'est dans ce contexte qu’est né le projet collaboratif de R&D « AEROPRINT », coordonné par Dassault Aviation, a été mis en place, avec l’aide de nombreux partenaires, centres de recherches, universitaires et industriels, dont AddUp fait partie. Structuré sur 5 ans, ce projet vise à développer, qualifier et mettre en place un démonstrateur préindustriel compétitif de fabrication additive métallique multi-matériaux (Titane et Aluminium), dans le but de fabriquer des pièces aéronautiques complexes certifiées de classe 2 et 3. Le site Dassault Aviation d’Argonay en Région Auvergne-Rhône-Alpes (France) a été identifié comme pilote pour la mise en place de cette filière.
C’est AddUp, fabricant de machines et de pièces additives, qui est en charge du développement d’un nouveau système de production basé sur l’interopérabilité et la robotisation des procédés. Un véritable atelier automatisé qui permettra grâce à la technologie additive, de produire en série et dans deux matériaux différents des pièces pour l’aviation. L’objectif est de mutualiser les équipements tout en assurant la séparation et la bonne circulation des deux matériaux choisis. Les experts d’AddUp travaillent sur un nouveau type d’enceinte fermée qui permet de faire entrer de la poudre d’un côté pour sortir un plateau de pièces métalliques de l’autre. Ce futur atelier sera composé de 2 unités de production de 4 machines FormUp® 350 basée sur technologie de fusion sur lit de poudre (L-PBF : Laser Powder bed fusion) ainsi que les moyens de parachèvement nécessaires.
Après une phase de recherche et développement commune permettant d’explorer toutes les exigences de ce projet, AddUp travaille à présent sur la maquette taille réelle afin de vérifier et valider les principes retenus, de la conception mécanique à l’autonomisme sans oublier l’informatique, tout étant géré par ordinateur. AddUp Manager, avec son interface ergonomique et intuitive, équipé d’un moteur de génération de trajectoires ultra rapide, permet de préparer les fichiers de production en accédant à plus de 250 variables modifiables et aux stratégies de fusion personnalisables.
Le monitoring, sujet primordial pour un tel projet, sera réalisé à l’aide du logiciel déjà disponible AddUp Dashboards, et augmenté par des briques développées à cet effet. AddUp Dashboards permet de visualiser en temps réel l’intégralité des données de production, de surveiller l’atelier et d’analyser rapidement tout événement machine. Retenons parmi les nombreuses vues préconfigurées et proposées dans le logiciel une cartographie personnalisable qui expose en temps-réel progressions, temps de production restant et statut courant. Les utilisateurs peuvent ainsi accéder aux données d’une production réalisée quelque mois plus tôt et suivre via le même outil une production en cours.
Comment fonctionne cet atelier automatisé ?
Les deux poudres métalliques, conditionnées en conteneurs industriels, sont chargées par un opérateur sur un poste de livraison situé à l’extérieur de l’atelier. A l’intérieur, le plateau de production est pris en charge par une station de conditionnement automatisée qui va l’insérer dans une chambre mobile, appelée « chemise ». Le tout est transporté dans une navette inertée par un Véhicule à Guidage Automatique (VGA), puis placé dans chaque machine PBF, en fonction du matériau souhaité. Lorsque l’impression est terminée, la navette récupère la chambre mobile pour l’amener vers une station de dépoudrage.
Cette même station permet de retirer la majorité de la poudre non fusionnée lors de l’impression, et de la renvoyer pour l’impression suivante, après une phase de recyclage. Ce dépoudrage terminé, la navette se dirige vers la station de conditionnement où le plateau portant les pièces est extrait de la chambre pour se diriger vers la station de lavage et de séchage des pièces. Cette dernière accueille un nouveau plateau et repart en impression. Le plateau portant les pièces est quant à lui nettoyé plus finement avant d’être autorisé à ressortir de l’atelier où il est pris en charge par l’opérateur.
Nombreux sont les avantages d’un atelier automatisé. D’un point de vue HSE, les opérateurs n’ont pas du tout de contact avec la poudre. Ils pénètrent dans l’enceinte robotisée uniquement pour des opérations de maintenance et leurs opérations se font à l’extérieur de celle-ci. D’un point de vue industriel, une fois le process validé et qualifié, la répétabilité des productions est assurée.
Cet atelier automatisé précurseur sera la base d’une solution industrielle prête à l’emploi pour le déploiement de machines de fabrication additive dans des ateliers existants, en garantissant le meilleur niveau de productivité et de sécurité.
www.addupsolutions.com