www.industrieweb.fr
24
'23
Written on Modified on
La société Les Volailles de Keranna optimise la consommation énergétique de son installation d’air comprimé grâce à Beko Technologies
Les Volailles de Keranna, filiale du Groupe LDC basée à proximité de Quimper, souhaitait renouveler son installation d’air comprimé, optimiser sa consommation énergétique et obtenir une certification ISO50001. Elle s’est tournée vers Beko Technologies.
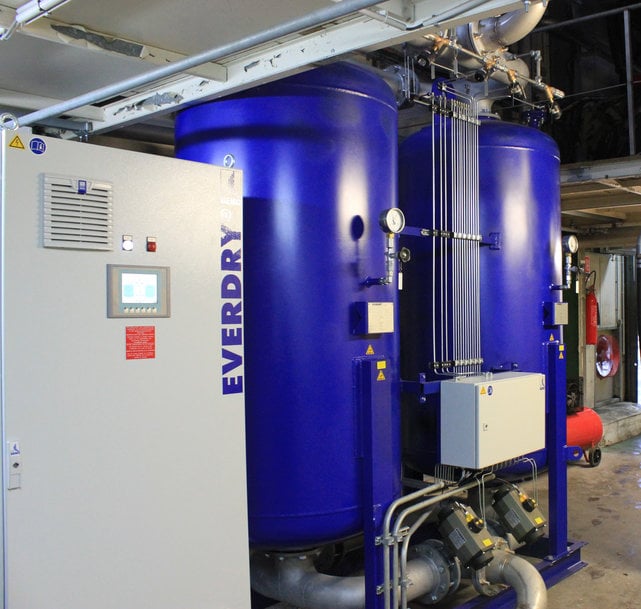
L’usine des Volailles De Keranna, basée à proximité de Quimper, découpe environ 600 000 poulets et dindes par semaine, soit plus de 31 millions d’unités à l’année. Élevées en Bretagne, les volailles sont destinées à la vente en grande distribution, soit en produit entier ou pour transformation.
Le responsable maintenance du site explique dans quelles circonstances son choix s’est tourné vers Beko Technologies : « nous avons reçu une documentation présentant l’expertise de Beko Technologies dans l’analyse d’hydrocarbures sur les réseaux d’air comprimé au bon moment. Nous venions d’entamer une démarche d’acquisition d’un nouveau système de traitement d’air comprimé pour notre installation, nous avions commencé à discuter avec nos prestataires habituels quand Beko Technologies est entré dans la compétition. »
La modification des capacités du système de traitement d’air comprimé s’avérait nécessaire
Pour la partie traitement de l’air, le sécheur par adsorption en place depuis plus de 10 ans commençait à montrer de sérieux signes de fatigue. Compte tenu de la vétusté des matériels, il n’était pas envisageable de remettre à niveau cette installation. Quant au réseau d’air comprimé, les nombreuses fuites entamaient un potentiel déjà mis à mal par la présence d’eau, dangereuse pour l’outil de production. Pire, le process du sécheur adsorption consommait de l’air comprimé (phase de refroidissement) et par conséquent de l’énergie, engendrant ainsi des coûts d’exploitation supplémentaires.
Un besoin clairement défini
L’industriel avait constaté que le sécheur adsorption en place engendrait une consommation énergétique et des coûts d’entretien importants sans pour autant assurer la performance attendue. Pour le responsable maintenance, il était donc devenu impératif d’optimiser l’installation et cela passait par le remplacement du système de séchage. L’objectif était clair : moderniser le système de traitement d’air comprimé pour réduire et maîtriser les consommations énergétiques et obtenir la certification ISO50001 orientée vers le management de l’énergie et l’environnement.
Des économies d’énergies garanties par Beko Technologies
À partir des constats effectués, les experts de Beko Technologies ont présenté une solution au responsable de maintenance du site qui avait en charge la réalisation du projet. Déjà présent avec des purgeurs de condensats, Beko Technologies a préconisé une installation de traitement d’air comprimé ayant le double avantage d’être sur-mesure et évolutive dans le temps sans avoir à remettre en cause l’existant ou nécessiter de modifications importantes. Alimentée par 5 compresseurs : trois de 90 kW et deux de 55kW à vis lubrifiées refroidis par air pour une capacité utile de 3 600 m3/h, le moindre arrêt est préjudiciable. « Notre production n’impose pas une classe de qualité d’air comprimé très pointue (classe : 2-2-2 selon la norme ISO 8573-1) explique le responsable de maintenance, en revanche elle ne tolère pas la présence d’eau, ce que Beko Technologies nous garantit ». Cet engagement n’est pas le seul point à l’origine de la décision des Volailles De Keranna. « Côté matériels, la réputation de Beko Technologies n’est plus à faire et, côté gains énergétiques, les chiffres avancés étaient nettement supérieurs à ceux des concurrents ». D’ailleurs chez nous le poste concernant les économies d’énergies a été déterminant dans le choix final. Le site s’est engagé dans une démarche ISO 50001 fortement orientée vers la préservation de l’environnement. »
Monté puis démonté en usine par les techniciens SAV de Beko Technologies pour en connaître toutes ses composantes, le sécheur a été réassemblé en deux jours sur le site de Bretagne, malgré les difficultés induites par l’exiguïté du lieu d’implantation du sécheur, contraint de passer par le toit. Le temps d’installer le nouveau sécheur et de le rendre opérationnel, les lignes de production n'ont eu à souffrir d’aucun arrêt puisque Beko Technologies avait mis à la disposition de son client un sécheur frigorifique d’air comprimé DRYPOINT RA 4400 en prêt pendant toute la durée de l’intervention.
Satisfaction des exigences formulées par Les VOLAILLES De KERANNA grâce à une solution sur-mesure innovante
La solution sur mesure est composée de sous-ensembles standards parfaitement adaptés entre eux, comportant un séparateur cyclonique CLEARPOINT, un ensemble de filtration CLEARPOINT composé de filtres dévésiculeur, déshuileur et antipoussières, un sécheur par adsorption avec régénération par apport de chaleur EVERDRY modèle FRA « Zéro Purge », plusieurs purgeurs capacitif de condensats BEKOMAT, un hygromètre METPOINT DPM et un débitmètre METPOINT FLM.
Au bout de plusieurs années d’utilisation, le responsable maintenance tire un bilan très positif et souligne les économies réalisées : le process de séchage utilisé « Zéro Purge » a permis de supprimer la consommation d’air comprimé « process » du sécheur permettant l’arrêt du compresseur de 75 kW.
Le ratio W/m3 est en forte baisse : le sécheur adsorption FRA « Zéro Purge » n’effectue plus qu’environ 4 cycles de régénération par semaine contre plus de 28 pour la précédente installation. Ces avantages, couplés à de la prime CEE (Certificat d’Economie d’énergie), doublée dans le cadre d’une certification ISO50001, ont permis un amortissement de l’installation en seulement un an.
www.beko-technologies.com