www.industrieweb.fr
20
'16
Written on Modified on
PECM EMAG : passer à la vitesse supérieure pour l’usinage de Blisk
Le nombre de pièces BLISK (Blade Integrated Disk) augmente massivement dans l’industrie aéronautique. Les gros réacteurs comptent désormais plusieurs de ces compresseurs haute pression, qui sont fabriqués en une seule pièce en matériaux haute performance extra-durs. Par conséquent, leur usinage efficace est désormais au centre des attentions du planificateur de production - mais il existe une variété de procédés et combinaisons envisageables, de l’usinage par enlèvement de matière à la découpe par jet d’eau. Une étude récente du Fraunhofer Institute for Production Technology (IPT) et du laboratoire des machines-outils (WZL) de l’université technique de Rhénanie-Westphalie à Aix-la-Chapelle montre que pour la finition des surfaces, l’usinage électrochimique de précision (PECM) EMAG entraîne d’énormes avantages en termes de coûts pour l'utilisateur.
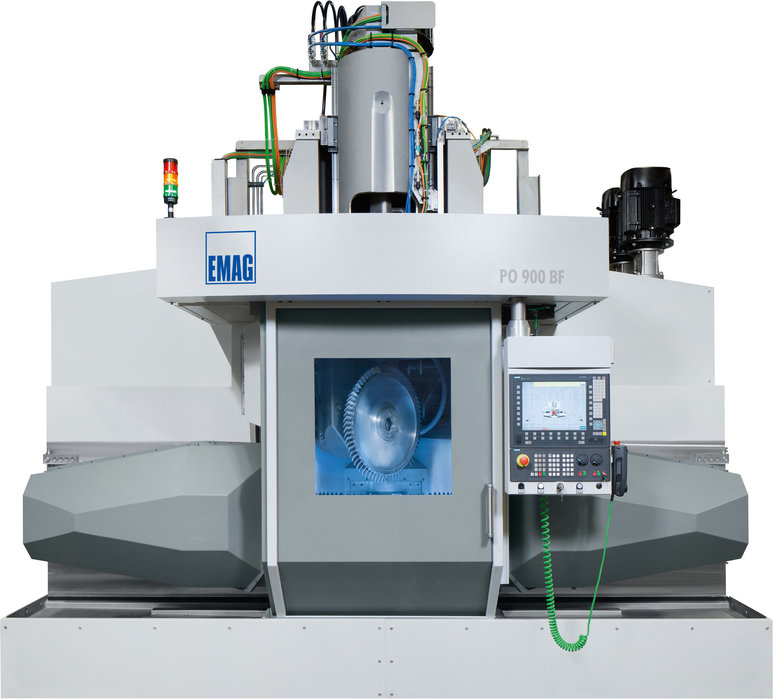
Enlèvement plus doux - processus rapides
Dans ce contexte, la technologie PECM EMAG ECM basée à Gaildorf est désormais au centre des attentions de nombreux OEM et de leurs fournisseurs. Le procédé électrochimique assure un enlèvement de matière particulièrement doux avec une usure minimale des outils. De plus, il est rapide et sécurisé. Le principe de base peut être expliqué de façon simple : pendant le processus, la pièce est sur une anode positive, l’outil sur une cathode négative. Entre les deux, se trouve une solution électrolytique et cela dissout les ions métalliques de la pièce. La forme de la cathode ou de l’outil avec les zones actives et conductrices est choisie de telle sorte que l’enlèvement de matière sur la pièce suit le contour souhaité. Les contours, canaux annulaires, rainures et cavités en forme de dôme se font sans contact - et ce avec la plus grande précision et la plus grande qualité de surface. Avec leur technologie PECM, les experts EMAG ECM ont développé et perfectionné ce procédé de façon ciblée. Deux facteurs jouent là un rôle décisif : premièrement, l’écart entre la pièce et l’outil, par lequel la solution électrolytique passe, est particulièrement étroit. Deuxièmement, l’alimentation en solution électrolytique est optimisée par un mouvement oscillatoire mécanique. Ces deux facteurs assurent un enlèvement encore plus efficace et précis de matière.
Des aubes de turbines individuelles aux BLISK
Pour différentes tâches d’usinage dans la construction de réacteur, EMAG ECM dispose de deux types de machines : alors que le petit modèle PO 100 SF est conçu pour l’usinage de petites aubes de turbines, la grande machine PO 900 BF sert à l’usinage de BLISK complets (et beaucoup plus grands). En conséquence, les machines diffèrent en termes de dimension de zone de travail, d’empreinte, de puissance du générateur et du nombre d'axes d'usinage - la technologie PECM précise et les composants haute performance EMAG sont bien évidemment disponibles dans les deux cas. « En 2011, nous sommes arrivés sur le marché avec la PO 900 BF destinée à la fabrication de BLISK. Le développement de la PO 100 SF s’est fait dans un deuxième temps en 2013, alors qu’une clientèle sans cesse croissante demandait une solution de machine électrochimique pour les pales uniques. Maintenant, nous disposons d’une base idéale pour développer des solutions de production sur mesure et rentables pour les petits et grands composants de réacteurs » a déclaré Richard Keller, membre de la direction chez EMAG ECM GmbH. Sur les deux types de machines, les utilisateurs bénéficient en outre des innovations centrales EMAG, comme la base en Mineralit, les interfaces logicielles et matérielles intelligentes ou les solutions d’automatisation efficaces.
Composants certifiés pour une utilisation pratique
Dans la pratique, cette approche conduit petit à petit au succès espéré. Par exemple, en 2014, un fabricant de réacteur renommé a certifié la pale unique fabriquée sur une PO 100 SF pour utilisation dans les avions - exceptionnellement rapidement après le début de la production de la machine chez un fournisseur. Une démarche similaire a actuellement lieu dans le domaine de la fabrication de BLISK. Diverses entreprises de technologie de réacteur sont actuellement en phase de qualification pour l’utilisation pratique de leurs composants. « La technologie est actuellement dans plusieurs programmes d’essai en phase de validation » c'est ainsi que Keller résume le travail actuel d'EMAG ECM. « La mise au point stratégique à long terme de ces composants et techniques d'utilisation porte ses fruits et entraîne un succès commercial à chaque nouvelle certification des composants fabriqués par PECM. »
La précision d’usinage géométrique est un facteur de réussite tout particulièrement décisif. En outre, les qualités de surface élevées présentent une faible rugosité. Les procédés de finition ultérieurs sur les pales, comme par exemple la tribofinition, peuvent donc être délaissés ou considérablement réduits - au final, ils sont équivalents avec une réduction supplémentaire des coûts. Pour un composant, qui est de plus en plus important et dont la quantité augmente considérablement, c'est un excellent argument.
www.emag.com
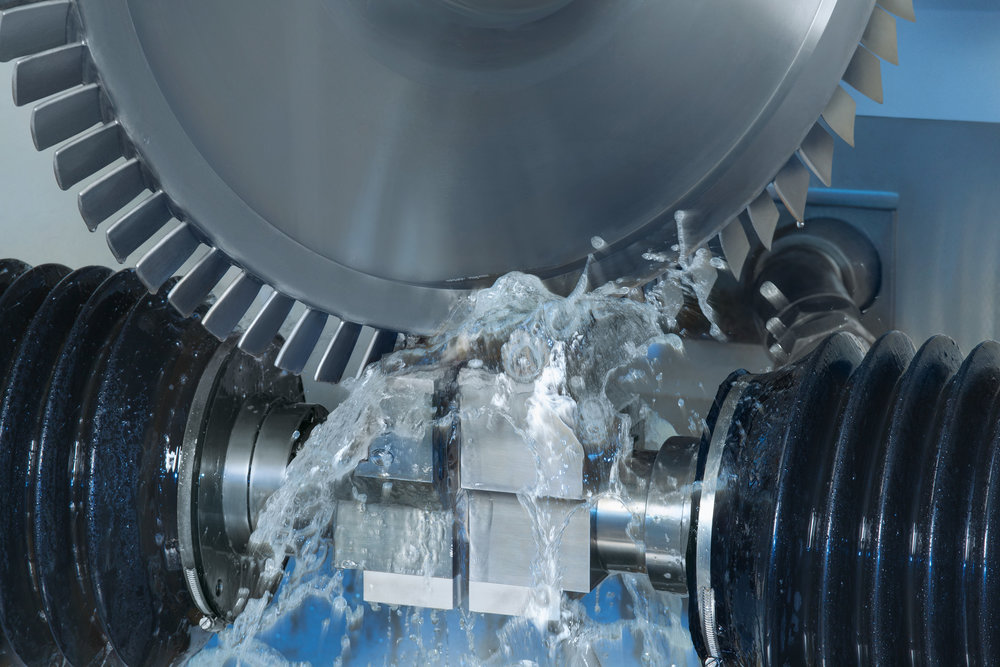
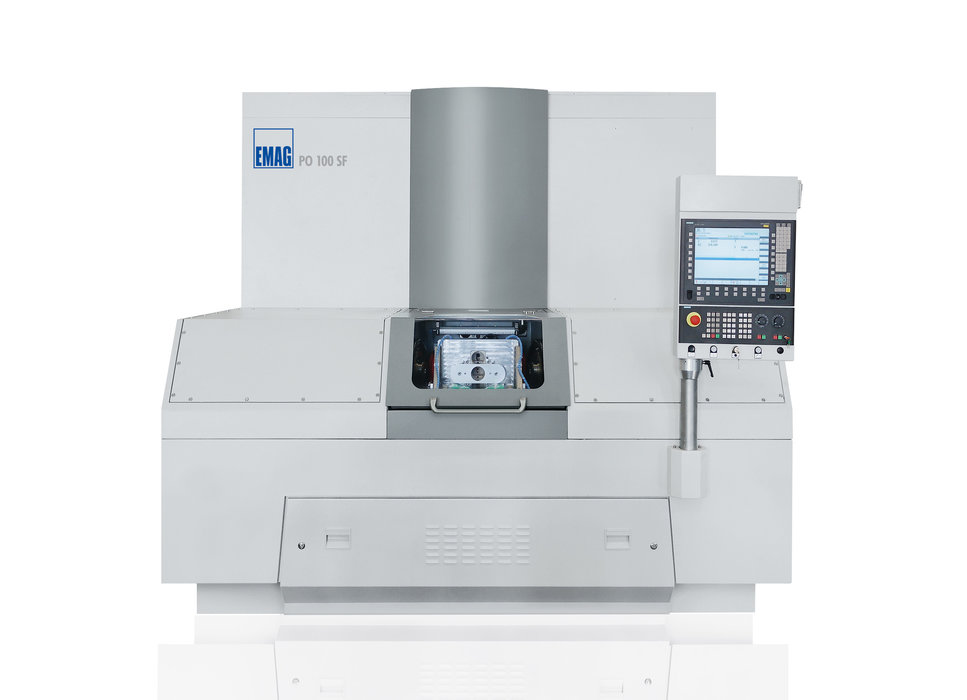