www.industrieweb.fr
18
'17
Written on Modified on
Approche pratique du contrôle du gaspillage pendant la fabrication
Les fabricants cherchent constamment à atteindre une performance et une productivité optimales. Ces efforts impliquent souvent des programmes de haut niveau qui utilisent des expressions à la mode telles que le cloud computing, la fabrication guidée par les données, les systèmes cyber-physiques et l'Industrie 4.0. Ces initiatives sont d'excellents concepts qui peuvent produire des résultats impressionnants. Cependant, la réalité de la fabrication interfère souvent avec la mise en œuvre de ces plans ambitieux, et le gaspillage non contrôlé pendant le processus de fabrication en est la preuve. Avant de réfléchir à la numérisation et l'optimisation, un fabricant se doit d'examiner ses opérations, de déterminer où se produit le gaspillage et de mettre au point des méthodes pour le réduire ou l'éliminer. Le contrôle du gaspillage constitue la première étape dans la préparation de l'adoption de stratégies de fabrication sophistiquées et intelligentes. Figure 1 - Vue d'ensemble des éléments de production et de leurs interactions dans une usine (concept et modèle NEXT STEP).
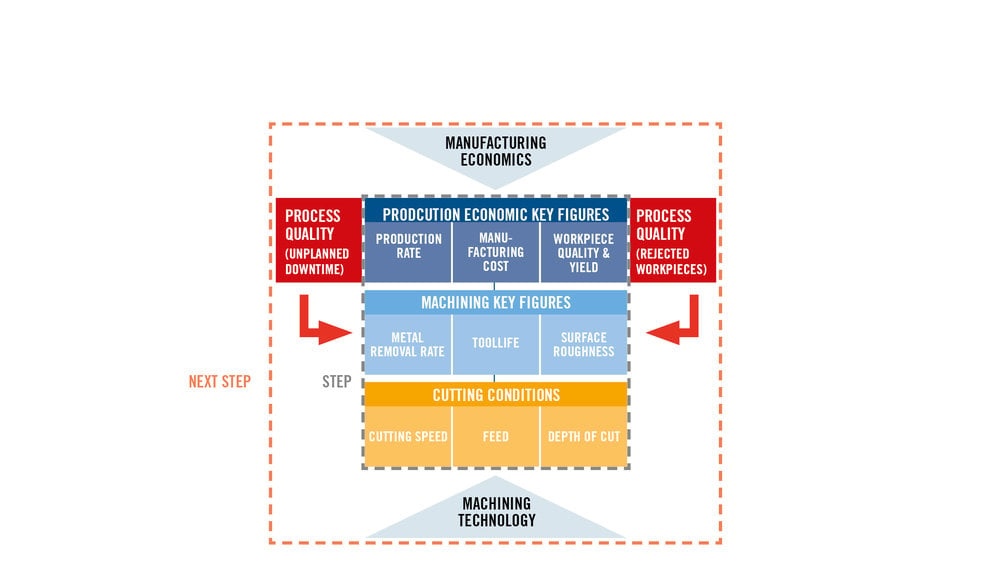
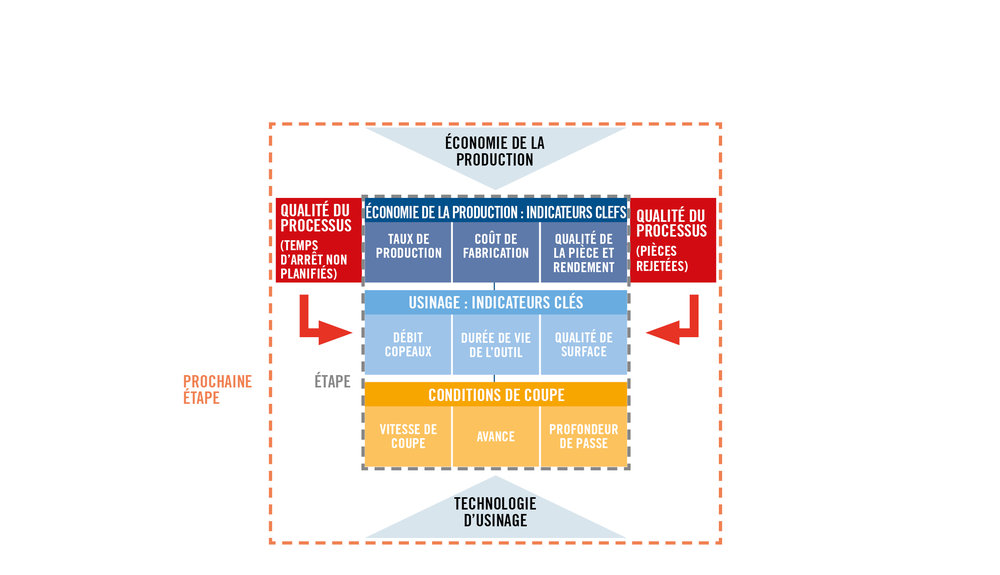
Les bases de l'économie de production
La fabrication consiste en une série de processus de transformation. L'atelier transforme les matières brutes en pièces finies ou semi-finies par le biais d'une série d'opérations de transformation en forge, soudure ou usinage. Un certain nombre d'éléments individuels composent chaque opération. Pour l'usinage, par exemple, ils incluent l'outil coupant, la machine-outil, les fixations et l'arrosage. Ensemble, ces éléments forment un système d'usinage qui s'appuie sur l'équipement et les composants associés dans un système de production.
Les fonctions de planification, de programmation et de gestion économique encadrent le système de production de façon à former un environnement de production. L'élément clé d'un environnement de production est le personnel. Bien que le processus de fabrication utilise largement des ordinateurs, robots et autres technologies avancées, le personnel prend les décisions assurant le contrôle de l'environnement dans son ensemble.
Le processus d'usinage est basé sur les particularités de l'application technique comme le choix de l'outil, des conditions de coupe, de la programmation, la matière à usiner et les fixations. Parmi les autres détails clés figurent les exigences en matière de volume de production et la qualité spécifiée des pièces finies.
L'économie de production consiste à établir le lien entre les particularités de l'application technique et les préoccupations d'ordre économique. L'objectif de l'économie de production est d'équilibrer tous les facteurs en jeu. Même si les éléments techniques produisent les résultats escomptés en termes de qualité de pièce, de quantité et de rapidité d'exécution, les opérations doivent être réalisées à un coût permettant à l'entreprise de prospérer.
Pour trouver l'équilibre entre le rendement et le coût pendant l'usinage, trois phases sont nécessaires. La première phase consiste à établir un processus d'usinage fiable. Il est essentiel de limiter les événements imprévus tels que les outils cassés, les copeaux non contrôlés et les destructions de pièces. L'atelier assure la fiabilité opérationnelle en choisissant des outils dont la capacité de charge atteint ou dépasse les charges mécaniques, thermiques, chimiques et tribologiques générés pendant le processus d'usinage.
Figure 2 - Modèle d'usinabilité globale développé dans STEP.
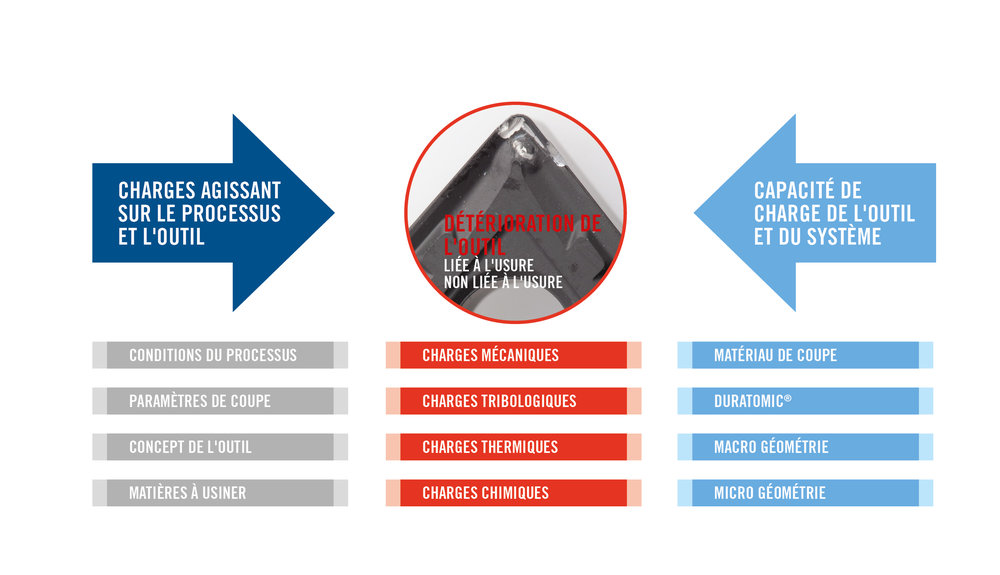
HQ_ILL_Machinability _model
La deuxième phase de la mise en œuvre d'une économie de production équilibrée implique de choisir des conditions de coupe qui reflètent les contraintes du marché sur le processus d'usinage. Les capacités théoriques d'un outil coupant sont larges. Mais dans les faits, l'atelier limite la plage effective des paramètres d'application.
Par exemple, les capacités et les performances d'un outil varient en fonction de la puissance de la machine-outil, des caractéristiques d'usinage de la matière ou de la configuration d'une pièce susceptible de vibrer ou de se déformer. Bien qu'un grand nombre de conditions de coupe puisse fonctionner en théorie, des contraintes d'ordre pratique imposées dans la réalité réduisent considérablement le champ des possibles.
La figure 3 illustre le vaste choix de possibilités au départ entre vitesses de coupe, de profondeurs de passe et d'avances, combinaisons qui se réduisent suite à l'arbitrage effectué entre les conditions de coupe lorsque les diverses contraintes réelles d'une application spécifique sont prises en compte.
Figure 3 - Illustration 3D qui représente l'ensemble des combinaisons de conditions de coupe possibles en fonction des contraintes imposées par l'environnement.
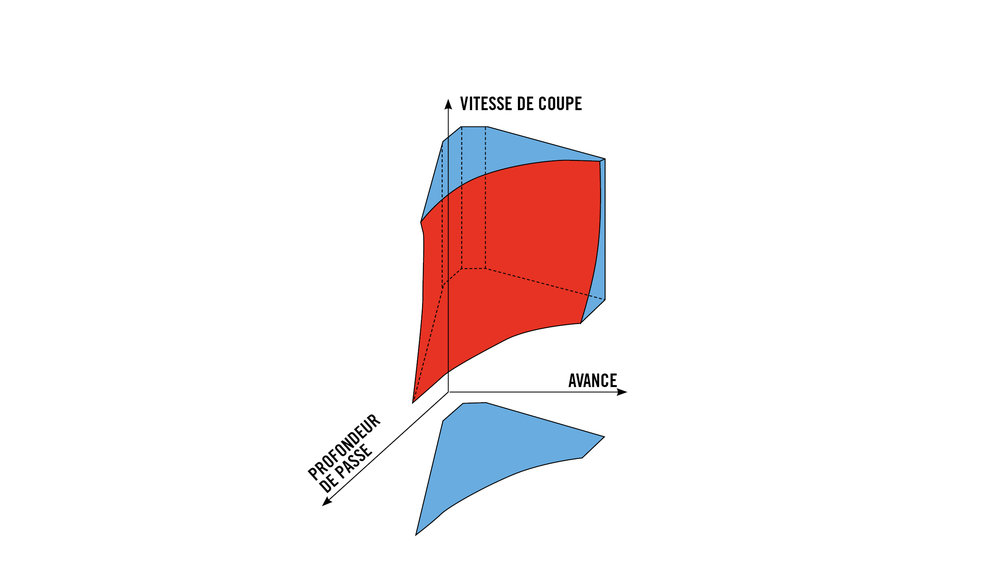
HQ_ILL_Machining_Process_cutting_conditions
Le non-respect des contraintes d'application des conditions de coupe liées à une situation particulière a des conséquences économiques néfastes, parmi lesquelles la hausse des coûts et la baisse de la productivité. Environ 90 % des problèmes rencontrés pendant l'usinage sont dus au non- respect de ces contraintes imposées par les réalités de l'atelier sur le processus de coupe.
Lorsque les conditions de coupe ne dépassent pas les contraintes imposées par les réalités de l'atelier, l'opération est sûre d'un point de vue technique. Cependant, toutes les combinaisons de conditions de coupe techniquement sûres ne produiront pas le même résultat économique. En effet, la modification des conditions de coupe entraîne la modification du coût du processus d'usinage. Opter pour des conditions de coupe plus agressives mais toujours sûres d'un point de vue technique augmentera le volume de pièces finies, mais au bout d'un certain temps, la productivité diminuera car les paramètres de coupe agressifs réduiront la durée de vie de l'outil. La production de pièces finira par diminuer au fil du temps car le temps consacré au remplacement des outils usés sera plus important.
Toutefois, il existe une combinaison des conditions de coupe qui permet d'aboutir à un équilibre entre le rendement productif et le coût de fabrication. La figure 4 montre la relation entre les conditions de coupe, la productivité et le coût des outils et des machines. Remarque : le graphique se concentre uniquement sur les éléments qui varient en fonction des conditions de coupe. Les coûts des matières, les frais généraux et les coûts d'administration et d'ingénierie ne sont pas inclus. Les conditions de coupe plus agressives sont représentées à droite des axes et la productivité la plus élevée dans le haut. La zone bleu clair au milieu du graphique indique la plage dans laquelle les conditions de coupe atteignent un équilibre entre productivité (production maximale) et économie (coût minimum).
Figure 4 - Relation entre les conditions de coupe, la productivité et les coûts d'usinage. Cette figure représente un modèle simplifié, ne tenant pas compte des facteurs de gaspillage.
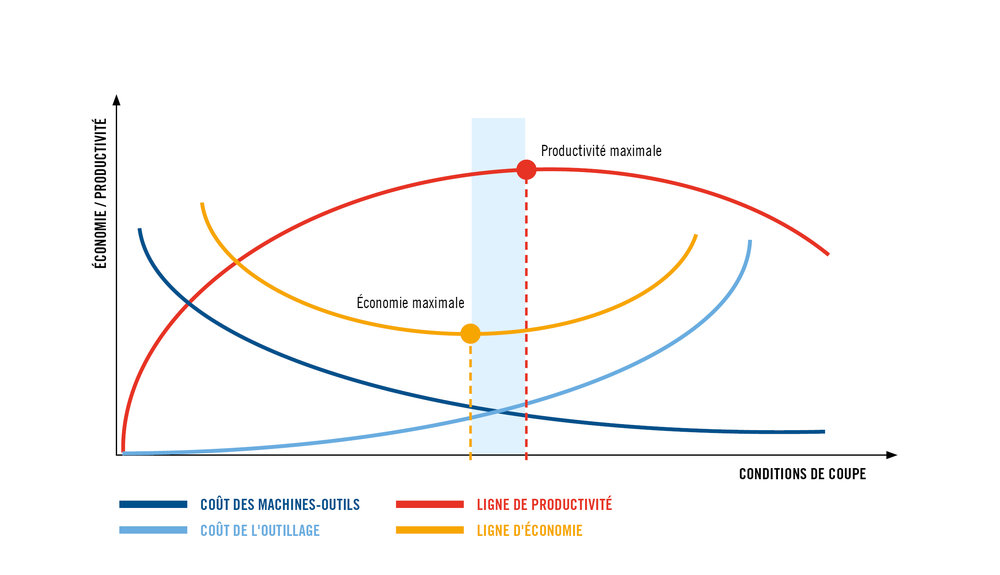
HQ_ILL_Machining_Process_relationship_cutting_conditions_productivity_machining_costs
En conséquence, la troisième phase de la mise en œuvre d'une économie de production équilibrée consiste à déterminer la combinaison optimale des conditions de coupe pour une situation donnée. Il est indispensable de prendre en compte tous les facteurs qui entrent en jeu lors de l'usinage pour établir un domaine d'application dans lequel les paramètres de coupe fournissent les niveaux de productivité et d'économie désirés.
L'effet du gaspillage sur l'économie de production
Malheureusement, ces méthodes scientifiques d'économie de production équilibrée sont à la merci du gaspillage dans le process de fabrication. Le gaspillage détruit l'équilibre et prend différentes formes. Utiliser par exemple une machine-outil de 60 kW pour une application qui ne nécessite que 15 kW est un gaspillage d'énergie et de puissance. Autre cas : lorsque des pièces finies ne répondent pas aux niveaux de qualité requis ; le temps, l'argent et les ressources investis dans le processus ont été gaspillés pour obtenir un résultat non-acceptable. De même, la fabrication de pièces qui dépassent inutilement les niveaux de qualité requis constitue une dépense inutile car l'amélioration de la qualité engendre une augmentation des coûts.
Bien que moins évident et moins bien compris, la sous-utilisation ou la mauvaise utilisation des ressources intellectuelles est aussi un cas de gaspillage. Certaines personnes au sein de leur entreprise possèdent des connaissances ou compétences qui peuvent l'aider à atteindre ses objectifs, mais pour des raisons allant du manque de communication aux politiques propres à l'entreprise, ces qualifications ne sont pas partagées et donc gaspillées.
Outils de réduction du gaspillage
Une fois le gaspillage identifié et classé en différentes catégories, l'atelier se doit de mettre au point un plan pour le réduire ou l'éliminer. Il existe alors une vaste gamme d'outils permettant à un fabricant d'identifier, de quantifier et de réduire au minimum les pratiques inutiles. Par exemple, l'analyse de l'utilisation, de la manipulation et de la détérioration de l'outil mettra en évidence certains problèmes.
Dans certains cas, ces analyses ont montré que 20 à 30 % des outils considérés comme usés par le personnel étaient en réalité encore utilisables. La durée de vie restante des outils était donc gaspillée. La mise en place de critères d'usure d'outil clairs et la communication des normes au personnel de l'atelier réduiront considérablement le gaspillage de la durée résiduelle des outils.
De même, les analyses des temps d'arrêt machine évaluent le temps consacré aux activités telles que la configuration, la programmation et le changement d'outil. Ces analyses indiquent souvent que 50 à 60 % des arrêts machine sont évitables grâce à une meilleure compréhension, exécution et coordination de ces activités chronophages mais nécessaires.
La mise en place d'entretiens, d'enquêtes et de programmes de formation peut révéler un grand nombre d'informations utiles au traitement des problèmes de personnel qui mènent au gaspillage des ressources intellectuelles ainsi que des connaissances et des compétences non connues. Les employés sont ainsi plus performants et renforcent leurs capacités, ce qui maximise la productivité du personnel.
Gestion des activités à valeur ajoutée, des activités sans-valeur ajoutée immédiate et des activités inutiles
Au début du 20ème siècle, l'ingénieur industriel américain Fredrick Taylor a étudié les opérations dans l'atelier et a proposé que l'amélioration de la productivité passe par l'élimination de toutes les activités dans le processus qui n'ajoutent pas de valeur au produit final. Les lignes directrices du « lean manufacturing » moderne suivent cette même ligne de pensée.
Dans les opérations d'usinage, la seule véritable activité à valeur ajoutée est celle où l'outil coupe le métal et produit des copeaux. D'autres actions comme le chargement et la fixation des pièces, appelées activités sans valeur ajoutée immédiate, sont pourtant essentielles à l'exécution de l'activité qui elle, apporte de la valeur ajoutée.
Le troisième groupe d'activités du système d'usinage rassemble les activités inutiles. Ces activités ne créent pas de valeur, ni ne contribuent à la création de valeur, et consomment des ressources sans engendrer aucun bénéfice. Il s'agit là d'un gaspillage pur et simple. La résolution des problèmes est un exemple d'activité inutile. Lorsqu'un processus est correctement conçu et contrôlé dès le départ, il n'y aura pas de problème, ce qui élimine ainsi la perte de temps associée à la résolution des problèmes.
Figure 5 - Schéma représentant un atelier d'usinage et tous les éléments s'y rapportant.
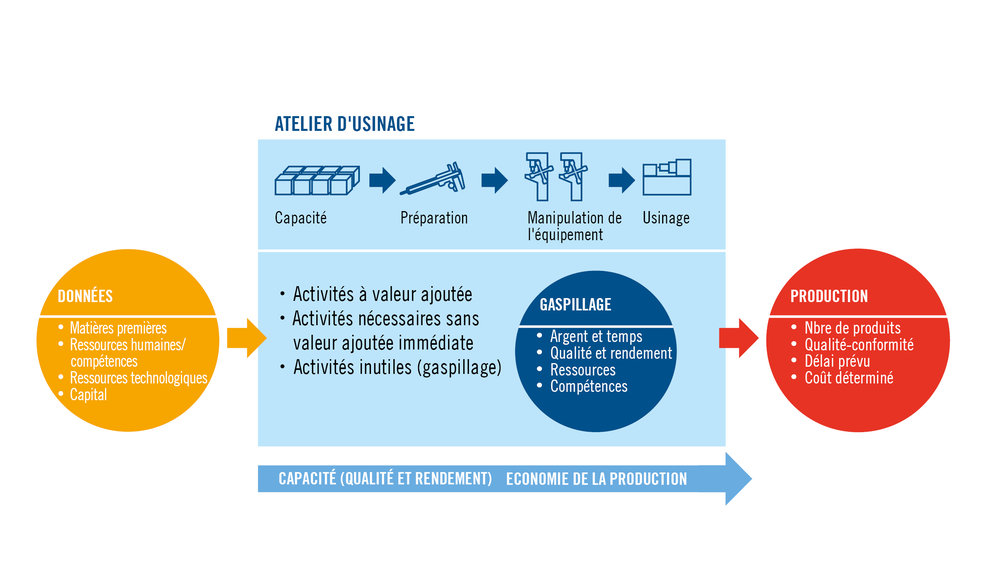
HQ_ILL_Machining_process_workshop
Conclusion
Par le passé, les activités inutiles étaient considérées comme faisant partie du processus de fabrication et n'étaient pas reconnues comme des obstacles à la réalisation d'une économie de production équilibrée. Actuellement, l'attention se tourne vers l'élimination ou du moins la réduction des activités inutiles. La planification des capacités ou de la productivité s'attache désormais à éliminer les activités inutiles, à limiter les activités sans valeur ajoutée mais nécessaires et à optimiser les activités à valeur ajoutée (voir la figure 6).
Figure 6 - Vue d'ensemble des activités à valeur ajoutée (orange), des activités sans valeur ajoutée pourtant nécessaires (bleu) et des activités inutiles (rouge). Le facteur humain (gris) est le facteur clé pour parvenir à la réalisation de performances de production optimales.
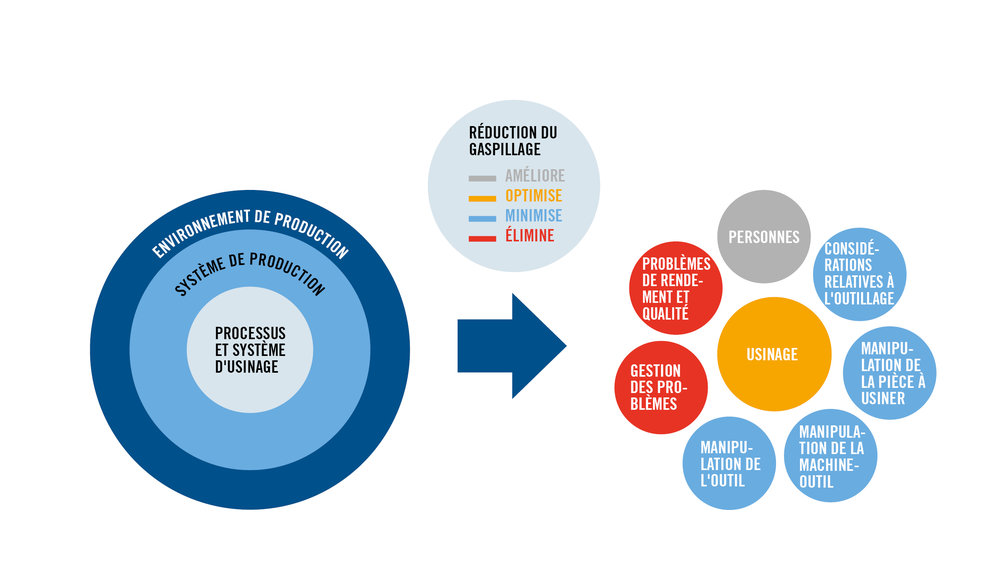
HQ_ILL_Machining_system_process
Une fois le gaspillage éliminé, l'économie de production théorique se transforme en économie de production pratique. À ce stade, les progrès réalisés en économie de production peuvent être appliqués directement au profit de la réussite de l'entreprise. Toutefois, dans cette recherche d'élimination totale du gaspillage, il convient de rester prudent. Il est important d'évaluer le retour sur investissement des activités relatives à la réduction du gaspillage. L'élimination de certains types de gaspillage peut impliquer un investissement si important qu'il peut être préférable d'un point de vue économique de tolérer ce gaspillage, tout ou partie seulement, et de continuer ainsi. Ces décisions doivent être prises à la suite d'analyses quantitatives appropriées, des discussions doivent avoir lieu au sein de l'entreprise concernant l'incidence de ces décisions au regard des objectifs et de l'éthique de l'entreprise.
Encadré :
Services Conseil Seco
Plus les produits/pièces sont sophistiqués, plus les utilisateurs ont besoin d'aide sur les applications permettant de tirer pleinement profit des nouvelles technologies. En ce qui concerne l'usinage, le niveau initial d'assistance consiste en une aide à la sélection de l'outil le plus adapté à une opération donnée. Une fois l'outil sélectionné, des informations complémentaires sont fournies pour faciliter la sélection des conditions de coupe optimales, l'utilisation d'arrosage, etc. Ensuite, si l'outil ne fonctionne pas comme prévu pour cette opération, le fournisseur de l'outil peut assurer une aide au dépannage. Ces trois modes d'assistance constituent les services d'outillage traditionnels.
Lorsque le service d'outillage ne se limite pas à une seule application mais couvre un processus entier au cours duquel une pièce est soumise à plusieurs opérations sur une ou plusieurs machines, les utilisateurs finaux requièrent des conseils sur l'organisation de la séquence des opérations, la manipulation des pièces à usiner ainsi que d'autres facteurs de façon à maximiser l'efficacité et la productivité. Ce niveau d'assistance est fourni par les services d'ingénierie.
De plus en plus souvent, les fabricants cherchent à être conseillés sur l'amélioration des fonctions, du contrôle des coûts et de la production pour l'ensemble de l'atelier ou de leur organisation. Des sociétés de conseil indépendantes effectuent alors ce qu'elles décrivent comme du conseil en gestion ou en fabrication. Cependant, pour réaliser une véritable évaluation d'une entreprise, il est indispensable de bien comprendre les opérations de base réalisées dans l'entreprise.
Forte de sa longue expérience et de sa compréhension approfondie des processus d'usinage et de l'outillage, Seco fournit des services d'outillage traditionnels, des services d'ingénierie et, dans une certaine mesure, des services de conseil à plus grande échelle depuis plusieurs décennies. Ces services étaient proposés ponctuellement ou en fonction des situations données, mais en 2016, Seco a lancé les Services de Conseil afin de proposer à ses clients une gamme de services plus simple et plus réactive.
Les Services de Conseil Seco incluent un large éventail de ressources spécifiques et de prestations. L'assistance au choix de l'outil et sur les applications est disponible en ligne 24 heures sur 24 pour répondre aux besoins de productivité immédiats de l'atelier.
Les services d'ingénierie peuvent commencer par des échanges électroniques et se poursuivre par des visites sur site si nécessaire. Les services Conseil Seco peuvent également inclure une analyse complète et des conseils portant sur les opérations pour chaque fonction dans l'atelier. Ces services peuvent comprendre des conseils sur la maintenance de la machine-outil, l'agencement de l'atelier, la logistique et les fonctions organisationnelles. Ils peuvent aussi porter sur les compétences et les connaissances du personnel ainsi que la relation entre les techniques de fabrication utilisées et les stratégies de production de l'entreprise ; les considérations financières peuvent également être incluses.
Chaque relation de conseil Seco est basée sur le concept NEXT STEP mais elle est également adaptée aux besoins spécifiques du client. Il s'agit d'un échange entre Seco et ce dernier visant à atteindre des objectifs communs.