www.industrieweb.fr
07
'17
Written on Modified on
Succès au rendez-vous pour De Dietrich Process Systems avec le séchage hygiénique par sécheur sphérique sous vide destiné à la production de PAP Séchage rapide. Extraction complète. Nettoyage en un éclair.
Une fois fabriqués au moyen de procédés chimiques par voie humide, les principes actifs pharmaceutiques (PAP) sont précipités ou cristallisés à partir du solvant. Les étapes suivantes sont en général l’isolation et le séchage. Le séchage hygiénique sous vide requiert énormément d’attributs. L’innovant sécheur sphérique offre des performances de pointe selon le contrôle des processus et les dernières normes BPF. De Dietrich Process Systems fournit actuellement plusieurs unités dans ce domaine.
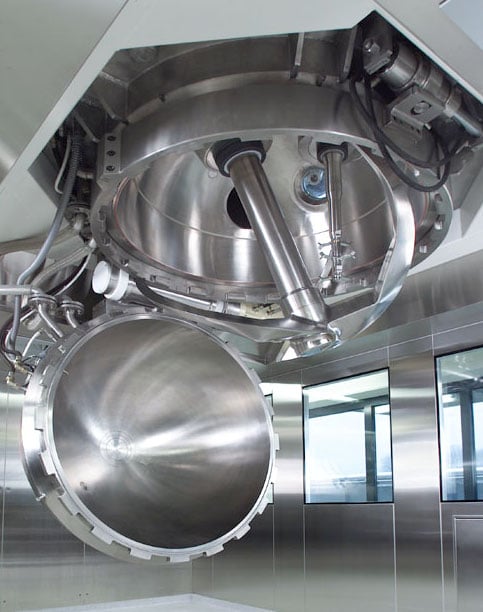
Avantages importants en un coup d’oeil
- Rapidité du séchage, du mélange et de la granulation
- Facilité de nettoyage (WIP/CIP)
- Extraction complète du produit
- Temps de séchage réduit grâce à un transfert de chaleur élevé
- Facilité d’inspection par ouverture à verrouillage rapide
- Résistance aux chocs engendrés par la pression d’une déflagration
- Compacité facilitant l’installation au sein des bâtiments de production existants
Le sécheur sphérique s’ouvre facilement, en faisant pivoter et en dégageant la moitié inférieure de la sphère. On dispose ainsi d’un accès visuel et manuel plein et entier à la zone de traitement ; l’accessibilité, la nettoyabilité et l’évacuation rapide exempte de résidus constituent les conditions préalables les plus importantes pour la production de produits de haute qualité. Un lavage et un nettoyage impeccables (WIP/CIP) sont indispensables pour maintenir les systèmes en parfait état de façon à satisfaire aux normes d’hygiène strictes.
Ces conditions posent un véritable problème pour les sécheurs à agitation sous vide, auxquelles répondent les caractéristiques de conception du sécheur sphérique breveté à entraînement par le haut Rosenmund®.
Mélange remarquable au moyen d’un agitateur à trois pales
Le sécheur sphérique assure un degré élevé de mélange grâce à un agitateur à trois pales spécifiquement conçu en adéquation avec la paroi sphérique. L’entraînement de l’agitateur avec le joint de l’arbre est monté sur la partie supérieure de la sphère. Pour l’étanchéité de la rotation, des joints mécaniques à double effet, lubrifiés par gaz ou liquide, sont fournis.
En chauffant l’agitateur et avec une vitesse rationnelle élevée, il est possible d’accroître l’échange thermique. Le jeu réduit entre le corps et l’agitateur améliore le transfert de chaleur et empêche les matériaux humides d’être cuits sur le moyeu ou les lames. Ce sont des conditions propices à un excellent mélange solide en contact avec la surface de paroi chauffée, qui se traduit par des temps de séchage courts et des résultats reproductibles.
Pour éviter la formation d’agglomérats, un hacheur à grande vitesse brise les grumeaux et contribue de l’intérieur à l’élimination de l’humidité.
Evacuation complète
Au centre et au point le plus bas de la sphère, un espace libre de vanne assure l’écoulement du produit sans restriction et sans risque de formation de ponts de matière en vrac. Grâce à ce passage libre et à un agitateur en légère rotation, des produits utiles peuvent être totalement évacués sans rester coincés.
Système d’étanchéité
Aux fins de conditionnement du produit extrait, le sécheur est livrable avec un système d’étanchéité. Ces systèmes sont souvent livrés avec une doublure continue pour éviter l’exposition des principes actifs au milieu ambiant. Grâce à une balance et à une vanne de vidange ouverte en continu, le produit peut être dosé selon une valeur préétablie. Un broyeur peut être inséré entre la vanne de vidange et le système d’étanchéité comme élément intégré pour obtenir des particules de dimensions inférieures.
Nettoyage en un éclair
Dans les industries pharmaceutiques, les organismes fédéraux fixent des critères en matière d’équipements de traitement de nettoyage. Ces bonnes pratiques industrielles sont des règlementations mises en place pour garantir le maintien d’un parfait état et de la propreté de l’équipement. Le souci principal est d’éviter la contamination du produit et la contamination croisée (par un nettoyage incorrect ou un entretien défectueux) pouvant dans les deux cas se traduire par des rappels de produits.
Grâce à la conception sphérique et à la disposition des pièces critiques comme le joint d’étanchéité mécanique au-dessus du niveau du produit, les procédures de lavage et nettoyage mises en place (WIP/CIP) peuvent être effectuées efficacement avec une quantité minimale de détergents. Les buses ARD (dispositif à rétraction automatique) mobiles et rétractables dotées de têtes gicleuses rotatives passent, sous l’effet de la pression exercée par le liquide de refroidissement, de la paroi de la cuve au centre de la sphère, assurant ainsi une bonne couverture des détergents sur les surfaces en contact avec le produit. Une fois la pulvérisation terminée, les buses ARD se rétractent sous la charge d’un ressort au ras de la surface interne de la cuve, en se refermant sans laisser d’espaces libres. En raison de la pente en direction de la vanne de sortie, les liquides nettoyants et les résidus de produit dissous s’écoulent au point le plus bas de la cuve.
Il est possible, pour les besoins d’un essai de couverture qualitatif des buses de pulvérisation, de réaliser un test à la riboflavine afin de mesurer la précision du nettoyage. Les résultats de cette procédure peuvent servir à l’élaboration de protocoles de validation du nettoyage.
Accès aisé pour les inspections
Pour permettre un accès aisé à tout moment, le sécheur sphérique à entraînement par le haut Rosenmund® s’ouvre facilement en faisant pivoter la moitié inférieure de la sphère. Cette opération s’effectue tout simplement, grâce à une baïonnette hydraulique à fermeture rapide placée au niveau de la bride principale et à une charnière à la jonction des deux sphères.
Avantage supplémentaire de cette partition en deux moitiés : la possibilité d’installer le sécheur entre deux étages : la zone d’extraction du produit avec la partie inférieure de la sphère disposée dans une salle blanche classifiée et la partie supérieure, placée séparément dans l’espace technique.
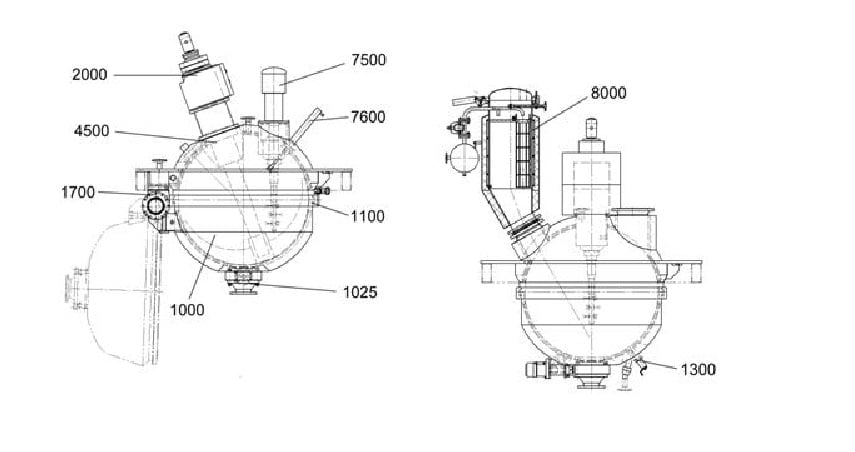
Description du module
1000 Sphère
1025 Vanne de vidange
1100 Fermeture rapide (baïonnette)
1300 Vanne d’échantillonnage
1700 Charnière à commande hydraulique
2000 Unité d’entraînement/agitateur
4500 Garniture mécanique
7500 Hacheur
7600 Boules de lavage (tuyères ARD)
8000 Filtre anti-poussières
Caractéristiques polyvalentes et dimensions
Les sécheurs étant en général destinés à un fonctionnement sous vide, les risques de décomposition thermique ou de déflagration de poussières obligent bien souvent à les concevoir pour des pressions plus élevées. La forme sphérique avec un volume maximal et une surface minimale constitue la géométrie idéale pour résister au choc engendré par une déflagration.
Le sécheur est fabriqué soit en acier inoxydable soit, pour les applications fortement corrosives, en alliages de nickel à haute résistance aux acides. Les capacités nettes vont de 100 à 4000 L. La cuve est entièrement gainée, isolée et recouverte d’une feuille métallique soudée. Le sécheur s’accompagne généralement de patins de chauffage / refroidissement et vide avec condensateur de vapeurs. Les particules fines fluidisables lors du séchage sont retenues par un filtre anti-poussières à cartouche, avec média filtrant constitué soit d’un tissu textile, soit d’un treillis métallique fritté.
Pour optimiser les résultats, il est important de régler les équipements périphériques (chauffage / refroidissement et condensation / vide) en fonction des exigences spécifiques des performances de séchage.
Pour le chauffage et le refroidissement, on utilise essentiellement des systèmes à boucle indirecte dans lesquels un liquide thermique (eau, mélange eau-glycol ou l’huile thermique) circule dans l’enveloppe du sécheur. Ce liquide passe à travers un échangeur thermique qui transfère la chaleur de la source calorifique (vapeur par ex.). Les produits sensibles peuvent nécessiter un refroidissement rapide en fin de séchage pour ne pas altérer leur qualité ; il convient donc de veiller à évacuer la chaleur du produit du liquide de refroidissement.
Des condensateurs, en général à coquille et à tubes, servent surtout à la récupération des précieux solvants de process qui se sont évaporés lors du séchage. Les condensateurs utilisés avec les sécheurs sont exploités de manière à condenser les vapeurs à l’intérieur des tubes plutôt qu’à l’extérieur. Avantage : les faisceaux de tubes droits peuvent être nettoyés plus efficacement.
Pour un séchage rapide et efficace à température d’évaporation réduite, un système de vide est indispensable. Un large éventail de pompes est proposé sur le marché, où l’on fait généralement appel à des pompes sous vide à vis ou à anneaux liquides.
Optimisation et adaptation du processus de séchage
Qu’il s’agisse d’optimiser des processus existants ou de développer les meilleurs paramètres de processus possibles pour des produits nouveaux ou modifiés, des essais sont recommandés. Les sécheurs sphériques Rosenmund® couvrent un large éventail d’applications. Du simple séchage aux processus combinés avec mélange et granulation, les résultats en matière de séchage et qualité produit peuvent être optimisés. Des machines pilotes sont par conséquent installées sur le site du fabricant pharmaceutique pour intégrer le sécheur sphérique dans le processus de fonctionnement.
En résumé : les sécheurs sphériques constituent la solution idéale pour la production de produits précieux comme les principes pharmaceutiques. La conception sphérique assure une évacuation complète et le nettoyage est facilement réalisable pour éviter tout risque de contamination croisée. Le sécheur sphérique Rosenmund® est à même de couvrir une large palette d’applications, du simple séchage au mélange et à la granulation. Grâce au transfert de chaleur élevé et à un équipement périphérique optimisé, le temps de séchage est sensiblement réduit.
Rosenmund® est une marque de De Dietrich Process Systems, dédiée aux solutions de filtration, séchage et confinement :
https://www.dedietrich.com/en/solutions-and-products/liquid-solid-separation
https://www.dedietrich.com/en/solutions-and-products/vacuum-drying-solutions
https://www.dedietrich.com/en/solutions-and-products/containment
De Dietrich Process Systems conçoit, produit et commercialise des solutions fondées sur des équipements faisant appel à des technologies d’acier vitrifié, acier inoxydable, alliages spéciaux et verre borosilicate destinées aux industries chimiques et pharmaceutiques.
Les activités de De Dietrich couvrent également l’ingénierie, la planification, l’installation et la mise en service d’unités chimiques dans des matériaux résistants à la corrosion et l’entreprise fournit les prestations de services correspondantes. Fondé in 1684, De Dietrich Process Systems bénéficie d’une forte présence internationale avec des bureaux implantés dans quinze pays.
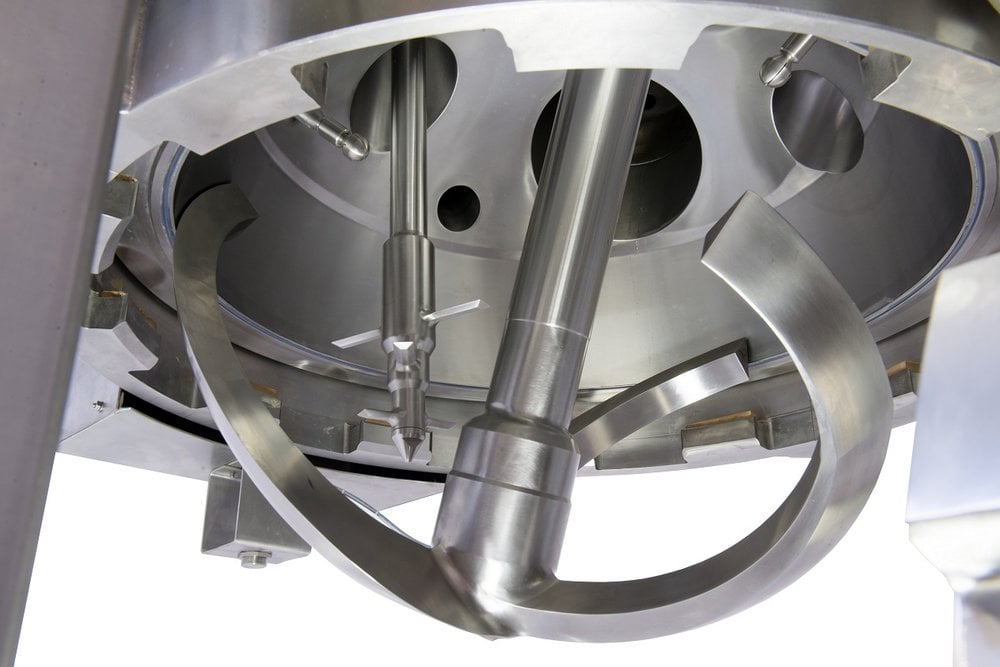
Agitateur à trois pales avec transfert de chaleur renforcé et hacheur à grande vitesse
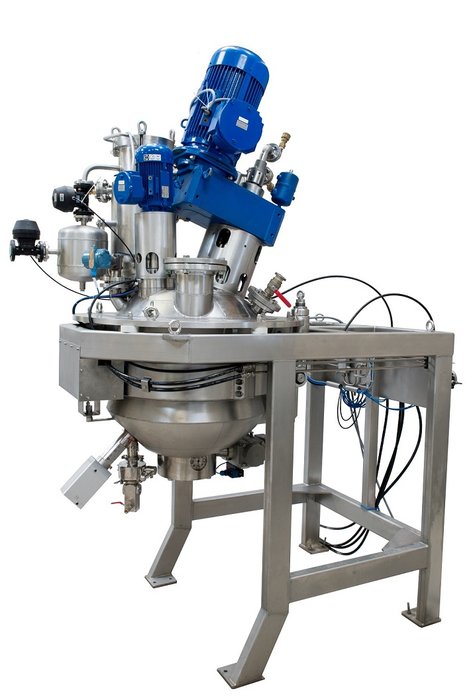
Machine pilote à sécheur sphérique Rosenmund®