Comment des composants standardisés peuvent-ils réduire les temps morts et permettre une continuité des opérations?
David Messant, Directeur de Production chez le spécialiste des composants standardisés norelem, étudie comment des composants standard peuvent être choisis pour mettre en place des solutions numériques, de chaîne logistique ou robotisées pour réduire les temps improductifs et optimiser la productivité.
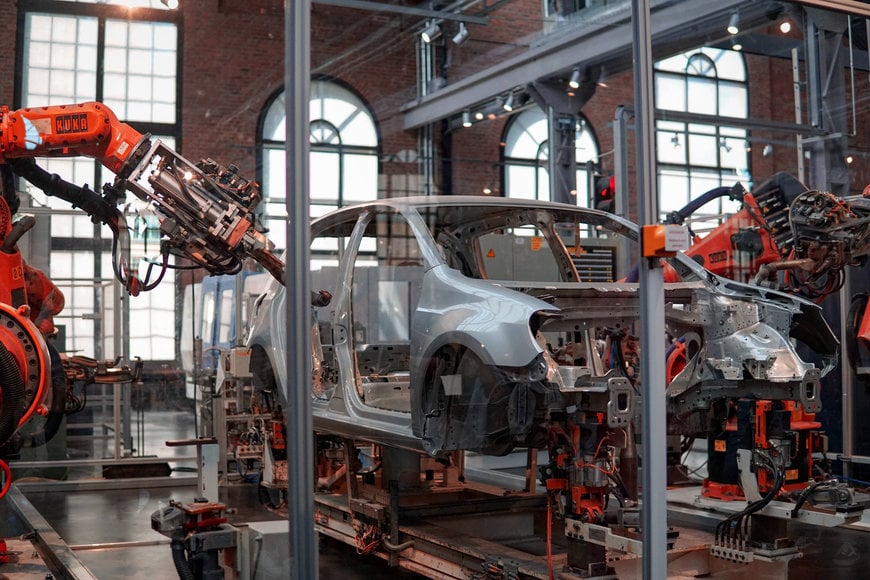
Traditionnellement, la conception et la production sont dépendantes du travail des hommes et des machines. Toutefois, cette dépendance crée aussi un risque- si la machine connait un arrêt non planifié, ou si son opérateur n’est pas disponible, toute la ligne de production s’arrête. En conséquence, les recettes et les bénéfices en souffrent, et si une solution n’est pas rapidement adoptée, c’est toute l’entreprise qui se trouvera en danger.
Pour nombre de fabricants, augmenter leur résilience à ces questions est crucial pour survivre, mais peut aussi devenir la clé pour déverrouiller un potentiel de productivité toujours plus grand. Les technologies baptisées « industrie 4.0 », comme l’automatisation, l’intelligence artificielle et la numérisation permettent aux entreprises de rester dans la course, les aidant à booster leur productivité et optimiser leur production.
Cependant, pendant que ce bouleversement technologique a lieu dans les ateliers et les usines, en pratique, cela peut prendre des mois sinon des années pour une mise en œuvre complète, voir ne jamais être réalisable. C’est la raison pour laquelle des fabricants peuvent se tourner vers des composants standardisés, ce qui offre la possibilité de réduire les coûts, d’optimiser l’efficacité de la production et rendre les ateliers plus résilients à des évènements imprévus.
Résilience et flexibilité
Un bon exemple de la contribution des composants standard à l’amélioration de la résilience est qu’ils assurent une bonne flexibilité. Cette souplesse est en phase avec un des mantras de ces dernières années, « l’usine du futur ».
Ces ateliers sont définis par leurs technologies de production avancées et ont certaines caractéristiques, l’une d’entre elles étant l’agilité à changer de production et à s’adapter à la demande. Pour ce faire, les ingénieurs doivent reconfigurer rapidement les lignes de production.
C’est ici que les composants standardisés interviennent. Au lieu d’investir dans des machines complexes et sur mesure et des composants coûteux et personnalisés, les concepteurs peuvent recourir à des éléments standard pour modifier rapidement et facilement la configuration de l’atelier.
Des pièces comme les engrenages, les vis sans fin, glissières guides, systèmes de positionnement motorisés et bien plus, sont disponibles dans une offre standardisée de dimensions et de matériaux chez norelem. Il s’agit simplement d’avoir les connaissances, le savoir-faire et d’en assurer l’accès aux entreprises pour assembler de nouvelles machines.
Des unités de production réalisées avec des éléments standard, offrent la garantie de pouvoir approvisionner et remplacer rapidement un élément si un composant tombait en panne, aidant ainsi à minimiser la probabilité d’un aléa qui augmenterait le temps de production.
Le rôle de l’automatisation dans l’optimisation de la productivité
L’automatisation a transformé le secteur manufacturier au long des deux dernières décennies. Les grands bras robotisés qui dominent les ateliers sont monnaie courante aujourd’hui. En même temps, les petits robots collaboratifs (ou cobots) travaillent de façon sécurisée à côté de leur partenaire humain pour exécuter avec efficacité les tâches répétitives, pénibles et salissantes. Il est clair que l’automatisation est la clé de la mise en fabrication moderne.
Cependant, personne n’est en mesure de prédire les prochaines étapes, c’est la raison pour laquelle les industriels peuvent commencer à examiner comment la robotique et l’automatisation peuvent les aider dans leur production - aussi bien en termes d’accroissement de production que pour permettre la poursuite des opérations dans le cas d’un manque de personnel. Bien que beaucoup de gens craignent que les robots prennent leur travail, franchir cette étape n’implique pas nécessairement de se passer d’humains, ceux-ci étant essentiels pour coordonner les opérations et interpréter les données.
Toutefois, l’obstacle rencontré par beaucoup de petites et moyennes entreprises est que l’investissement initial, la maintenance et l’entretien de nouveaux équipements les empêche de s’équiper de robots.
C’est sur ce point que les éléments standardisés peuvent rendre l’automatisation accessible. Avec des entraînements, des contrôleurs, courroies, poulies, engrenages et bien plus, disponibles dans des dimensions et matières variées et standardisées, les industriels peuvent rapidement et aisément automatiser différentes étapes de leur process, sans avoir recours à des composants spéciaux, coûteux et des ingénieurs extérieurs.
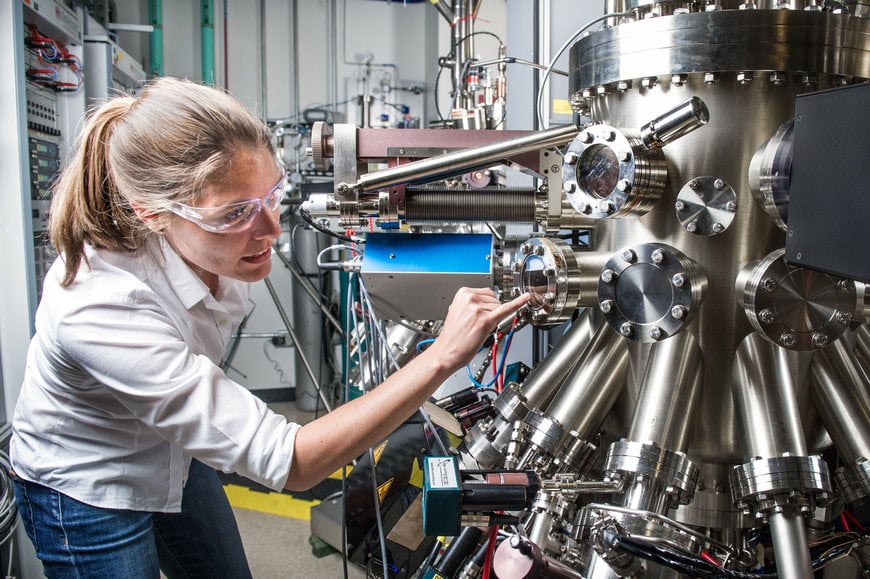
Adopter le passage au numérique et le travail à distance
Pour remédier à cette faiblesse, il est impératif que le secteur productif soit à même de s’adapter à différentes conditions de travail, comme celle de devenir capable de contrôler des robots à distance. Néanmoins, alors que la technologie commence à permettre aux opérateurs de contrôler les machines hors-site, le volet maintenance de la production devient plus délicat.
La cause en est que le besoin de maintenance est habituellement déclenché par des inspections visuelles mais être hors site ne permet plus cette option. S’il n’y a pas de mise en place d’une maintenance délocalisée en parallèle, cela peut amener le risque que des composants détériorés sans remise en état possible causent une panne inattendue.
Pour éviter cela, la solution est de numériser les éléments de la machine pour permettre aux ingénieurs d’effectuer une maintenance et de diagnostiquer les problèmes pour les résoudre rapidement.
A titre d’exemple, par l’ajout de capteurs aux équipements, les ingénieurs peuvent suivre les paramètres physiques tels que la température et les vibrations. Ceci élimine le recours à des tests de diagnostic longs et fastidieux, tout en augmentant la probabilité d’une première correction par rapport à plusieurs visites sur site. Avoir accès aux données assure que la bonne pièce et l’élément standard peuvent être commandés et la machine remise en état aussi vite que possible.
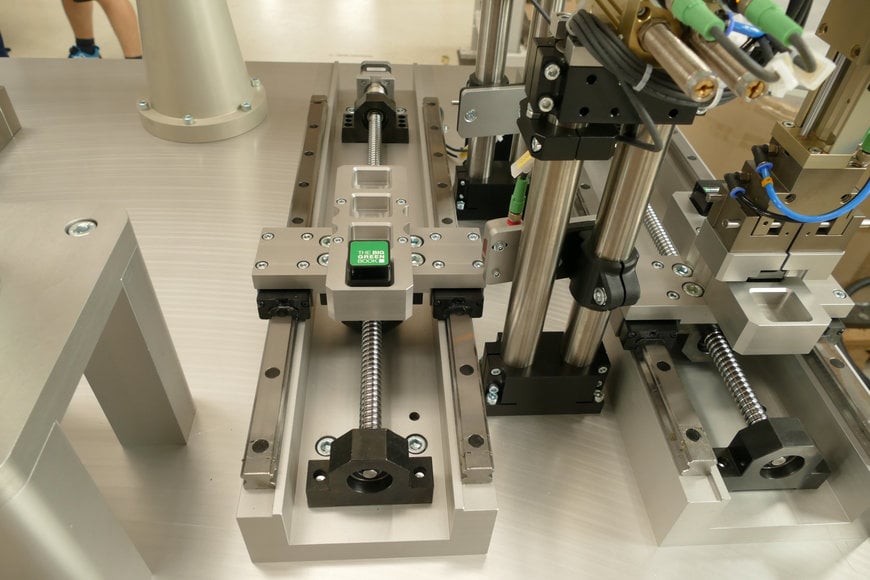
Eléments standardisés - le pilier de l’ingénierie
Des périodes difficiles peuvent impacter n’importe quelle entreprise, mais avec le caractère particulier de la conception et de la fabrication, les effets en sont démultipliés. Pour pouvoir surmonter toutes les tempêtes à venir, les industriels doivent être plus flexibles. La capacité à surveiller, contrôler, régler et adapter les process de fabrication est vitale pour réduire les temps improductifs, augmenter la productivité et assurer la pérennité de l’entreprise.
Alors qu’il y a débat autour des bénéfices à attendre des nouvelles technologies de rupture souvent déroutantes, dans les périodes de crise, beaucoup trouvent des solutions dans ce qu’ils maitrisent. Les éléments standardisés sont l’épine dorsale de la fabrication, simplifiant le process et assurant que l’entreprise puisse se focaliser sur un retour rapide à une productivité maximale.
Pour en savoir plus sur norelem, rendez-vous sur www.norelem.fr
Biographie de l’auteur- David Messant, directeur de production chez norelem
David Messant est Directeur de Production chez norelem. Très expérimenté dans l’ingénierie de production, il est entré chez norelem en 2007 en tant que Chef d’atelier. Son rôle et ses responsabilités incluent la Direction de la Production et de l’équipe de maintenance chez norelem, le recrutement et la formation, le développement des projets techniques et la stratégie d’investissement en machines.
En dehors du travail, David est un cycliste et sportif reconnu. Faisant partie de l’équipe de l’UV Aube Troyes depuis des années, dont il a pris la présidence et a été aussi choisi pour diriger la course Paris-Troyes de 2020.