www.industrieweb.fr
22
'20
Written on Modified on
Sur la voie de l'automatisation robotique des processus : commencer petit tout en anticipant l'avenir
L'introduction de l'automatisation robotique dans un flux de travail déjà bien établi peut sembler compliquée et coûteuse. Grâce aux dernières technologies modulaires et aux outils de configuration intuitifs, les entreprises peuvent pourtant en récolter les fruits rapidement et simplement, en faisant évoluer leurs systèmes au fur et à mesure.
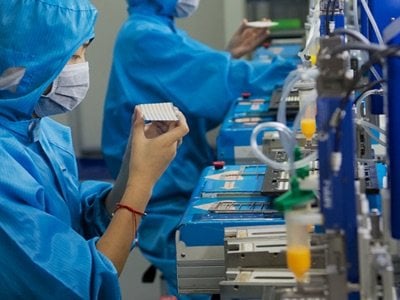
Les processus industriels reposent de plus sur l'automatisation pour atteindre leurs objectifs de productivité et assurer à la fois une qualité de production régulière et un rendement soutenu. Un processus peut être intégralement automatisé, de bout en bout, sans aucune intervention humaine, ou bien partiellement automatisé en prenant le meilleur des machines et des hommes.
Imaginons que les hommes et les machines coopèrent au sein d'un même espace : nombre de nos contemporains vont imaginer une multitude de robots collaboratifs multiarticulés (« cobots ») programmés pour effectuer les tâches les plus répétitives ou physiques tandis que les hommes feront preuve de dextérité ou de créativité pour finaliser le processus. Mais l'introduction des cobots dans une usine requiert une ré-optimisation significative des processus et une réorganisation physique de l'espace de travail.
Le premier niveau d'automatisation robotique des processus
Les fabricants peuvent commencer à bénéficier des avantages de l'automatisation robotique des processus de façon plus simple et moins invasive. De nombreuses lignes de production sont opérées par des hommes, qui effectuent diverses tâches sur des pièces de travail apportées par un convoyeur. On pourrait penser qu'en augmentant la vitesse de convoyage, les pièces transitent plus rapidement et la productivité s'améliore, mais ce n'est pas toujours le cas. Même si les opérateurs parviennent à suivre le rythme plus soutenu du convoyage, les problèmes se produisent en fin de ligne, où les pièces de travail arrivent à une vitesse supérieure et peuvent bouger voire tomber au sol. La productivité s'en trouve alors réduite malgré l'accélération des convoyeurs.
La technologie robotique permet d'éviter ce problème. Les robots linéaires sont capables de remplacer les convoyeurs traditionnels et sont faciles à programmer d'un point de départ à un point d'arrivée définis numériquement, sans qu'une butée mécanique ne soit nécessaire Les accélérations et décélérations se produisent en douceur et à des distances prédéfinies, d'où une vitesse de transit élevée. Plusieurs modules peuvent fonctionner indépendamment les uns des autres sur la même ligne de production, en remplacement d'un convoyeur standard, dont la vitesse est fixe. Cette flexibilité permet d'optimiser la vitesse de transport à différents points de la ligne en fonction des exigences de chaque processus, pour équilibrer le flux de travail.
En outre, la possibilité d'aller en avant et en arrière ouvre de nouvelles opportunités pour atteindre une efficacité maximale. Yamaha permis à plusieurs clients de profiter de tels avantages en intégrant son module de convoyage linéaire robotique LCM200 sur les lignes de production. Ce modèle est rapide, efficace, mais aussi moins exigeant en termes de réorganisation des flux de travail que la mise en place de cobots articulés à plusieurs axes.
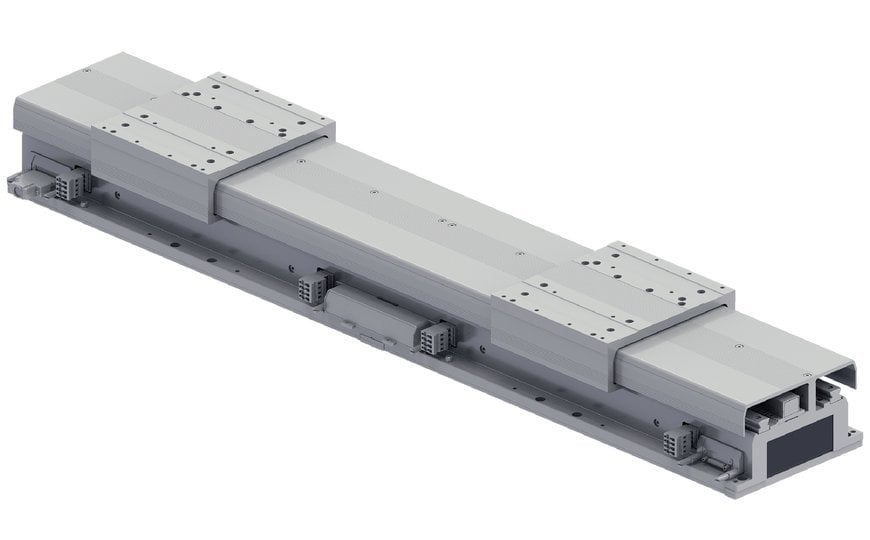
Ce module linéaire remplace les convoyeurs traditionnels et comporte les avantages des robots : vitesse et souplesse.
Ce robot linéaire modulaire ouvre la voie à l'automatisation robotique des processus, qui va du simple remplacement d'un convoyeur ou d'une table tournante à l'automatisation complète des processus dans une cellule d'assemblage robotique dédiée.
Pour créer des flux de process complexes, automatisés par des robots, pour la fabrication de produits de petite taille, comme des enceintes ou des modules automobiles composés de divers composants, les intégrateurs de solutions doivent souvent recourir à des robots de plusieurs types pour réaliser chacun des gestes d'assemblage en limitant le coût et l'empreinte au sol. C'est pour les y aider que Yamaha propose une gamme unique et complète regroupant l'ensemble des robots industriels les plus couramment utilisés, du LCM200 modulaire aux robots cartésiens et SCARA, en passant par d'autres modèles à axe unique. Grâce à eux, les intégrateurs de solutions disposent de toutes les options dont ils ont besoin pour créer un flux de travail efficace, y compris lorsque la surface de travail est restreinte, tout en tenant compte de considérations importantes comme l'entretien, la programmation et la facilité d'utilisation.
L'évolution vers un gain de place supérieur
La gamme de robots de Yamaha contribue largement à économiser de l'espace, en particulier les robots SCARA orbitaux montés au plafond de la série YK-TW, qui permettent un mouvement par le dessous, quand leur pointe passe sous l'unité principale (Schéma 3). Réussir à rendre les processus plus compacts est un avantage non négligeable, notamment pour les équipementiers qui veulent relocaliser ou reprendre à leur compte des processus auparavant externalisés. Même si les changements économiques mondiaux indiquent que la tendance est à la relocalisation, peu d'usines locales disposent de biens immobiliers suffisants pour héberger de nouveaux processus. Lorsque chaque centimètre carré compte, les robots SCARA orbitaux ont montré qu'ils sont capables de fonctionner dans des espaces particulièrement exigus. Avec une longueur de bras de 350 mm et une charge utile de 5 kg, la largeur d'installation peut se réduire à seulement 492 mm.
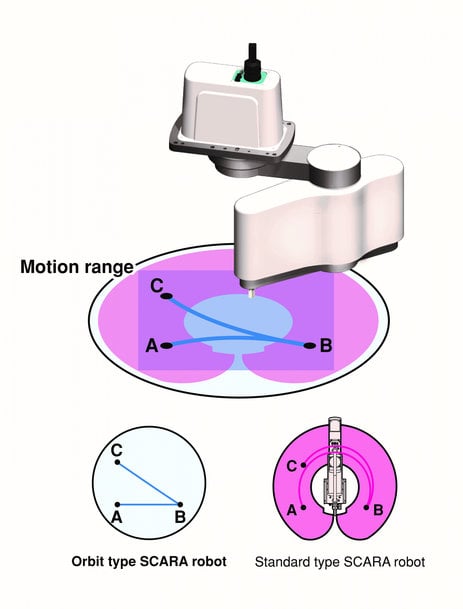
Les robots montés au plafond à mouvement par le dessous utilisent l'espace disponible très efficacement.
Les principaux atouts des robots SCARA sont la vitesse à laquelle ils récupèrent et déplacent les pièces de travail et leur capacité à réaliser des assemblages comme le vissage et la dépose d'adhésifs, de joints ou d'autres matériaux d'interface thermique. La dimension du bras des robots SCARA oscille entre 120 mm pour une charge utile de 1 kg, et 1 200 mm pour les modèles capables de soulever jusqu'à 50 kg. La famille YK-XG de Yamaha propose des entraînements sans courroie et sans entretien qui permettent un mouvement haute vitesse et haute précision sur quatre axes. Par ailleurs, le moment d'inertie est optimisé de façon à permettre une rotation rapide des objets lourds, contrairement aux machines conventionnelles qui doivent réduire leur vitesse et dont le temps de cycle est plus long.
Forte de sa longue expérience et de son ancrage dans le secteur des robots industriels destinés à l'automatisation de l'assemblage de gros volumes de composants moto dans les années 1970, Yamaha a mis au point ses robots hautement sophistiqués et les a dotés de fonctions innovantes telles que le TRANSERVO, qui permet aux moteurs pas-à-pas d'allier haute vitesse et couple élevé.
Parmi les autres caractéristiques fortement appréciées des intégrateurs pour simplifier la conception de solutions, citons la lubrification à faible maintenance, l'efficacité des barrières anti-pollution, les pièces mécaniques innovantes haute rigidité qui offrent une meilleure précision, y compris en cas de forte pression, ou encore l'utilisation généralisée des résolveurs de position, plus robustes et plus fiables que les détecteurs optiques de position traditionnels.
Grâce aux différents systèmes de contrôle à leur disposition, les intégrateurs peuvent configurer une solution abordable pour répondre aux principaux défis d'automatisation, tout en laissant la porte ouverte à de futures évolutions et adaptations. Équipés d'unités de contrôle simples pour le positionnement et l'entraînement, les robots à axe unique peuvent être facilement commandés à l'aide des points de coordonnées ou de l'entrée de trains d'impulsion de manière à limiter la programmation.
D'autre part, les contrôleurs à plusieurs axes peuvent servir à diriger simultanément un ou plusieurs robot(s) à simple ou double accès. Il est possible de lier un maximum de quatre robots à 4 axes en configuration maître/esclave pour gérer jusqu'à 16 axes et renforcer le contrôle dans un programme écrit en langage robotique Yamaha, qui est une extension du langage BASIC de programmation.
Une évolution en toute confiance
La réussite d'un premier projet d'automatisation incite souvent les opérateurs à vouloir faire évoluer ou renforcer leurs systèmes pour gagner en productivité et en qualité de fin de ligne. L'introduction de la vision automatisée fait partie des évolutions courantes, même si cette technologie nécessite des compétences précises et des processus de configuration traditionnels qui peuvent s'avérer compliqués et chronophages. L'établissement de communications entre le système de vision, le robot et les autres sous-systèmes, notamment de suivi, figure parmi les obstacles les plus fréquemment rencontrés, avec le calibrage du système de vision et l'enregistrement précis des données relatives aux pièces de travail.
C'est pour faciliter la vision robotique que Yamaha a créé son système RCXiVY2+. Dans les systèmes robotiques traditionnels de vision, les caméras sont connectées à un processeur de vision dédié, qui communique ensuite avec le contrôleur principal via une liaison de données en série. Avec le RCXiVY2+, le contrôle de l'éclairage et le traitement des images et des données de suivi du convoyeur sont effectués par le programme du robot en utilisant des instructions de vision dédiées créées par Yamaha et ajoutées au jeu d'instructions BASIC étendu. Ce jeu d'instructions de vision simplifie la recherche et le suivi des composants, d'où une réduction de moitié du temps de recherche. Une recherche plus rapide permet alors une meilleure détection des pièces à une vitesse de convoyage supérieure, d’où une prise améliorée et un temps de cycle raccourci.
Le matériel comprenant une carte de vision dotée d'une interface de caméra GigE, une carte de contrôle de l'éclairage et une carte de suivi, toutes faciles à installer directement dans le contrôleur de robot à axes multiples de la série RCX3, de nombreux problèmes d'intégration sont évités et la compatibilité avec les périphériques est assurée. Dans la mesure où la vision est gérée à partir du programme du robot, il n'est pas nécessaire de créer une routine de conversion des coordonnées. En outre, le système intégré de Yamaha affiche des performances supérieures en supprimant les retards caractéristiques des systèmes de vision conventionnels, où les données de la caméra doivent passer par un processeur de vision séparé avant d'arriver au contrôleur de robot.
Pour accélérer l'installation du système, un processus de calibrage simple facilité par un assistant aide à aligner rapidement les coordonnées des caméras et un outil graphique réduit l'enregistrement des pièces de travail à seulement trois étapes : la capture d'images, le paramétrage du contour et l'enregistrement de la position de détection. Finalement, le temps de configuration est raccourci de 80 % par rapport à un système machine-vision conventionnel.
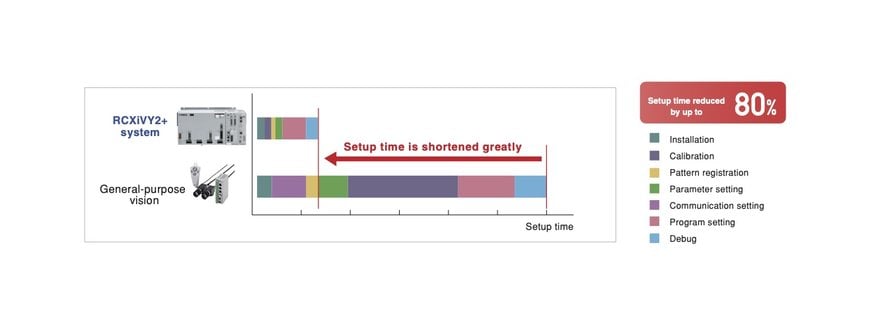
Le RCXiVY2+ aide les utilisateurs à être plus productifs, plus vite
Lorsqu'il entre en action, un moteur puissant recherche les contours de l'image et améliore la détection des pièces. Le système peut détecter les vis et les rondelles qui fixent les pièces, des articles dans un emballage ou sur une carte de circuit imprimé, vérifier les trous percés et compter des objets comme des bouteilles sur une palette ou des composants électroniques. La sortie DVI-I de la caméra permet aux utilisateurs d'analyser les résultats de recherche à tout moment et d'enregistrer jusqu'à 254 pièces personnalisées supplémentaires à détecter automatiquement. Les caméras du RCXiVY2+ peuvent être montées en position fixe au-dessus et/ou en dessous de la pièce de travail, ou sur le robot lui-même. Lorsqu'elles sont montées sur le robot, les coordonnées sont ajustées automatiquement pour corriger les effets du mouvement.
Le système RCXiVY2+ suit par ailleurs une nouvelle approche en matière de traitement de l'image appelée « détection des regroupements de pixels », qui permet de reconnaître des objets de forme irrégulière jusqu'à 10 fois plus vite qu'avec les méthodes traditionnelles de détection des contours. Cette approche améliore la prise, la reconnaissance de présence et le comptage à haute vitesse de pièces multiples et est particulièrement efficace lorsque les objets ont une forme irrégulière, comme les denrées alimentaires et les vêtements, ce qui élargit le champ d'application de la vision robotique. Enfin, le système peut également reconnaître les pièces qui se chevauchent et les exclure de la cible de recherche.
Conclusion
Les processus d'assemblage manuels traditionnels, même assistés par quelques automates simples comme les convoyeurs motorisés, offrent peu de marge de manœuvre pour améliorer le rendement et la productivité. Les approches traditionnelles visant à améliorer le temps de cycle ont parfois l'effet inverse en termes de productivité, tandis que l'ajout de nouveaux employés et de lignes de production supplémentaires fait grimper les coûts de fonctionnement et nécessite plus de place.
Les premiers pas dans l'automatisation robotique des processus peuvent se faire facilement et sans interruption de la production s'ils sont réfléchis, par exemple en remplaçant des convoyeurs rigides ou de grandes tables tournantes par des robots linéaires programmables. Au fil du temps, l'automatisation pourra s'étendre à d'autres processus et à de nouvelles lignes de production et des machines de vision pourront être ajoutées en complément, pour un retour sur investissement supérieur.
www.yamaha-motor.eu