www.industrieweb.fr
07
'22
Written on Modified on
MCLAREN RACING IMPRIME EN 3D 9 000 PIECES PAR AN AVEC LA TECHNOLOGIE DE STEREOLITHOGRAPHIE DE DERNIERE GENERATION DE STRATASYS
La FIA ayant réduit les délais et les budgets de production des véhicules de F1 en 2022, McLaren s'appuie sur une série d'imprimantes 3D Stratasys Neo800 pour gagner la « course » hors du circuit.
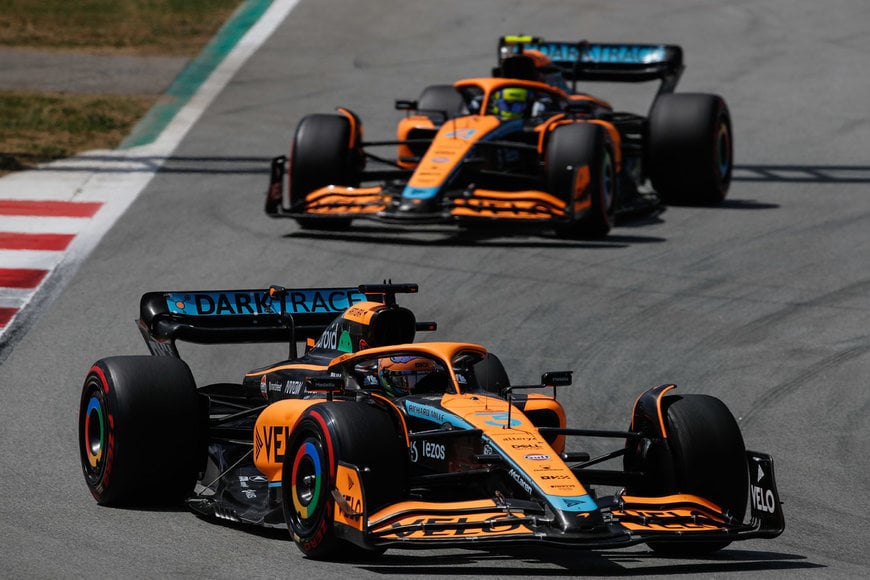
L'impression 3D diminue le temps de production de certains modèles réduits à seulement trois jours, ce qui accélère considérablement le développement de fabrication du véhicule.
L'excellente précision des pièces en matériaux polymères haute performance améliore les essais en soufflerie, ce qui permet à McLaren d'optimiser l'aérodynamique et de gagner des secondes essentielles.
Le géant de la Formule 1 McLaren Racing réagit au resserrement des délais et des budgets de production des véhicules imposé par la FIA en fabriquant des dizaines de milliers de pièces à l'aide de grandes imprimantes 3D stéréolithographiques Stratasys Neo®800 de dernière génération.
McLaren gagne la « course avant la course » en produisant jusqu'à 9 000 pièces par an pour de nombreux programmes d'ailerons avant et arrière, ainsi que de grandes pièces de la carrosserie latérale et du haut de caisse. L'écurie constate de grands progrès dans l'optimisation de l'aérodynamisme des véhicules lors des essais en soufflerie grâce à l'excellente précision des pièces imprimées sur ses cinq systèmes Neo800. Au-delà de l'aspect qualitatif, les délais de production des pièces ont également chuté de façon spectaculaire, l'équipe étant désormais en mesure de fabriquer certaines pièces de grandes dimensions, comme les hauts de caisse de ses modèles réduits, en seulement trois jours.
Le processus est également moins coûteux. Alors que le secteur est en proie à l'incertitude et qu'aucun revenu n'a été perçu pendant la pandémie de Covid-19, la FIA a décidé de ramener le plafond budgétaire de 175 à 145 millions de dollars pour sa première année d'exploitation en 2021, puis à 140 et 135 millions de dollars pour 2022 et 2023, respectivement.
Grâce à son parc d'imprimantes interne, McLaren peut fabriquer toutes les pièces aérodynamiques sur sa base de Woking, au Royaume-Uni, et économiser ainsi les coûts de sous-traitance et le processus d'assurance qualité associé. L'écurie peut également imprimer en 3D des gabarits et des modèles, ainsi que de petits moules qui auraient auparavant été usinés à partir de billettes de métal. Le processus de stéréolithographie de la Neo800 permet non seulement de gagner un temps considérable, mais aussi d'économiser en matériaux métalliques coûteux, car il évite la production de grandes quantités de copeaux issus de l'usinage soustractif.
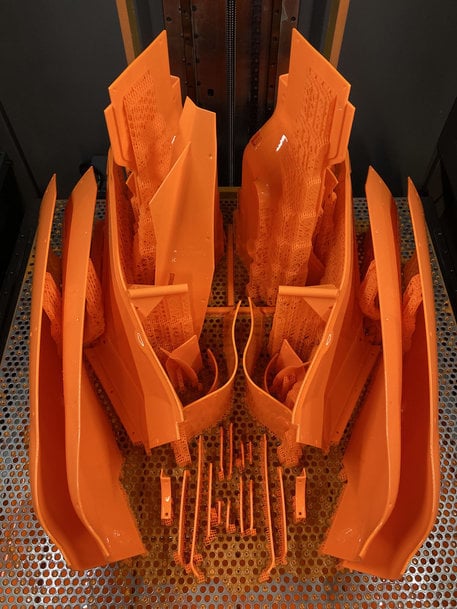
Selon McLaren, l'utilisation de la technologie d'impression 3D par stéréolithographie de Stratasys peut contribuer à réduire les délais de réalisation des composants et des projets aérodynamiques en soufflerie.
Les avancées en soufflerie font la différence
« La technologie de la stéréolithographie et les matériaux ayant évolué, nous avons changé notre façon dont nous les utilisons », explique Tim Chapman, responsable de la fabrication additive chez McLaren Racing. « Nous ne nous contentons plus de fabriquer des prototypes ; nous produisons désormais de nombreux composants à grande échelle et des outils à taille réelle. »
L'une des principales applications pour lesquelles McLaren estime que ses Neo800 de nouvelle génération sont les plus utiles est l'essai en soufflerie. L'écurie utilise des modèles réduits à 60 % pour optimiser l'ensemble aérodynamique et augmenter la déportance (et donc l'adhérence), et équilibrer les charges aérodynamiques avant et arrière de la voiture.
« Les essais en soufflerie restent essentiels pour évaluer le comportement de chaque surface, qu'il s'agisse d'un assemblage ou d'une voiture complète », explique Tim Chapman. « Nos imprimantes 3D de la gamme Neo nous ont permis de réduire considérablement les délais de production de nos composants et projets aérodynamiques en soufflerie. »
L'écurie imprime les pièces avec la résine Somos® PerFORM Reflect, qui a été spécialement conçue pour les modèles de soufflerie. Elle peut ainsi créer des pièces solides et rigides qui écourtent de 30 % la durée du post-traitement.
M. Chapman poursuit : « Nous constatons que les composants haute définition issus de nos machines Neo ne nécessitent qu'une finition manuelle minimale, ce qui permet un passage beaucoup plus rapide en soufflerie. En plus de la vitesse, nous pouvons maintenant produire des pièces de soufflerie avec une précision, des détails et une finition de surface remarquables, ce qui nous a permis d'optimiser les essais et de trouver des idées novatrices pour améliorer les performances. Je ne saurais trop insister sur l'importance de ces avantages en Formule 1, où les délais pour livrer les voitures à la prochaine course sont extrêmement serrés et où la moindre itération de conception peut faire toute la différence entre gagner, perdre ou gagner des places sur la grille. »
Les dimensions généreuses du plateau des imprimantes 3D Neo800 de Stratasys (800 x 800 x 600 mm) permettent de produire soit des pièces uniques de grande taille, soit une multitude de pièces beaucoup plus petites. Grâce à ce procédé, les détails complexes sont toujours préservés, avec une reproductibilité et une fiabilité de premier ordre.
McLaren en est l'exemple parfait : l'intégration de 50 ou 60 boîtiers dans ses voitures de course permet de mesurer la pression d'air sur différentes surfaces. Les petites prises de pression qui traversent ces composants sont très intriquées et détaillées, et sont placées à l'intérieur de la voiture pendant les essais et les courses pour permettre aux ingénieurs de surveiller et d'optimiser en permanence les performances aérodynamiques.
Andy Langfeld, président de Stratasys EMEA, déclare : « La révolution que représente l'impression 3D est liée à la possibilité de personnaliser et d'adapter rapidement des pièces à des applications spécifiques. Dans ce cas, McLaren a été en mesure de réduire considérablement le temps de développement du produit et de maîtriser les coûts grâce à la technologie de stéréolithographie de nouvelle génération de Stratasys, associée aux matériaux Somos de classe mondiale et à notre connaissance approfondie de la course automobile. C'est un fabuleux partenariat entre deux entreprises de niveau mondial. »
www.stratasys.com