www.industrieweb.fr
21
'23
Written on Modified on
La fabrication 3D chez Seco Tools offre de nouvelles opportunités
La fabrication additive, ou impression 3D, permet à Seco Tools de créer des produits qui seraient sans cela difficiles voire impossibles à produire. Parmi les avantages, citons des délais de production réduits, une durée de vie de l'outil améliorée et une durabilité accrue.
Le développement et la fabrication de prototypes pour l'usinage par le biais de la fabrication additive sont de plus en plus courants dans les opérations de Seco Tools. L'un des principaux atouts de cette méthode de fabrication est la possibilité de créer des outils et des solutions sur mesure et spécifiques au client, qui sont difficiles à réaliser avec une production traditionnelle. La technologie de fabrication additive révèlera tout son potentiel pour réaliser des outils dont la conception est spécifique. Cela peut concerner des géométries complexes ou d'autres adaptations aux besoins spécifiques du client.
Il peut s'agir, par exemple, de rendre les outils plus légers, ce qui améliore les performances d'amortissement des vibrations, ou de leur assurer de meilleures capacités de refroidissement. « En dirigeant l'arrosage directement sur l'arête de coupe, nous pouvons prolonger considérablement la durée de vie utile de l'outil. Grâce à la technologie de fabrication additive, l'arrosage peut être dirigé sur des zones qui auraient autrement été inaccessibles », explique Ingemar Bite, spécialiste R&D chez Seco Tools, qui pense également que cette technologie contribue à raccourcir les délais de production. « La fabrication additive nous permet de réaliser des géométries qui nécessitent moins d'étapes en production, ce qui se traduit souvent par des délais plus courts et donc des livraisons plus rapides. »
Une durabilité accrue
La technologie de fabrication additive permettra également de réparer les outils cassés à l'avenir, en supprimant les composants dysfonctionnels et en les réimprimant. Il peut s'agir, par exemple, des composants d'outil ou de la réutilisation de différents types de connexions côté machine. C'est notamment une bonne en termes de protection de l'environnement et de développement durable. Un autre avantage de la technologie de fabrication additive, par rapport à la fabrication traditionnelle dans ce contexte, est la réduction du gaspillage de matière. Dans l'ensemble, ce type de fabrication n'utilise pas autant de matériaux et les restes de poudre peut être réutilisé.
La fabrication additive pourrait donc être une méthode de production rentable et rapide pour les pièces uniques et le développement de prototypes. Néanmoins, elle pourrait également s'avérer excellente pour la fabrication à grande échelle de produits standard. Seco Tools fabrique déjà des brides d'arrosage pour ses outils Jetstream à l'aide de l'impression 3D. « Les brides d'arrosage ont une forme complexe avec des canaux incurvés et sont donc bien adaptées à ce type de fabrication », explique Ingemar Bite.
Des améliorations continues
Le service R&D de Seco Tools travaille en permanence pour améliorer l'utilisation de la technologie de fabrication additive pour le développement et la réalisation de produits nouveaux et existants. L'entreprise cherche constamment à améliorer ses produits et de tirer le meilleur parti de cette technologie. « Nous aimons collaborer avec nos clients dans ce domaine et réaliser des tests avec eux », déclare Ingemar Bite, qui estime que les matériaux eux-mêmes peuvent être
développés. « Les matériaux actuellement utilisés dans la fabrication additive fondamentalement différents que ceux utilisés dans les procédés conventionnels, et la technologie fonctionne correctement avec de nombreux métaux différents. À l'avenir, nous ajouterons encore davantage de matériaux de qualité supérieure, tout en adaptant régulièrement nos équipements et en mettant à niveau le matériel et les logiciels selon les besoins », conclut-il.
Différentes méthodes peuvent être utilisées pour la fabrication additive ; celle que Seco Tools a choisi est appelée SLM (Selective Laser Melting ou fusion sélective par laser). Avec cette méthode, les produits sont fabriqués à l'aide de lasers et d'un lit de poudre métalliques. Dans une machine SLM, une couche de poudre d'environ 20 à 60 µm est étalée, puis passée au laser. Ce processus est répété, couche par couche. Une fois toutes les couches en place, l'excès de poudre est éliminé et le produit passe à l'étape de post-traitement pour obtenir sa forme finale.
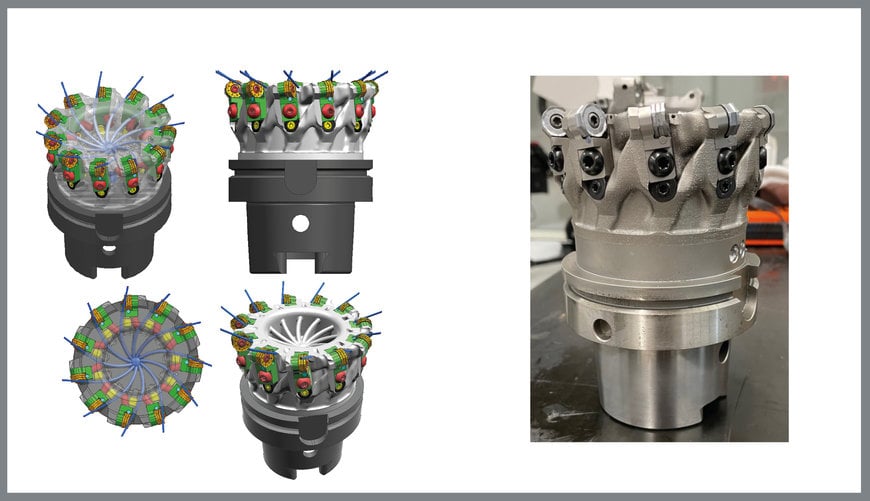
Finishing Hybrid AM Tool on HSK100

Coolant Clamp Mounted in Turning Tool