www.industrieweb.fr
12
'10
Written on Modified on
Placement de fibres à haute vitesse sur de grandes structures complexes
La réduction du poids des aéronefs est un sujet majeur. Non seulement, elle est très importante pour réduire la consommation en carburant, mais aussi, pour pouvoir parcourir des distances plus élevées. Du fait de sa haute résistance et son faible poids, la fibre de carbone est très attractive, mais le besoin de productivité élevée nécessite des machines très complexes. Electroimpact a développé une solution exceptionnelle offrant une vitesse de placement de fibres de 50mètres par minute. Cela implique un système de contrôle très sophistiqué, très stable et particulièrement précis des systèmes d'entraînement. Andantex USA a fourni tous les composants mécaniques critiques pour conduire les axes.
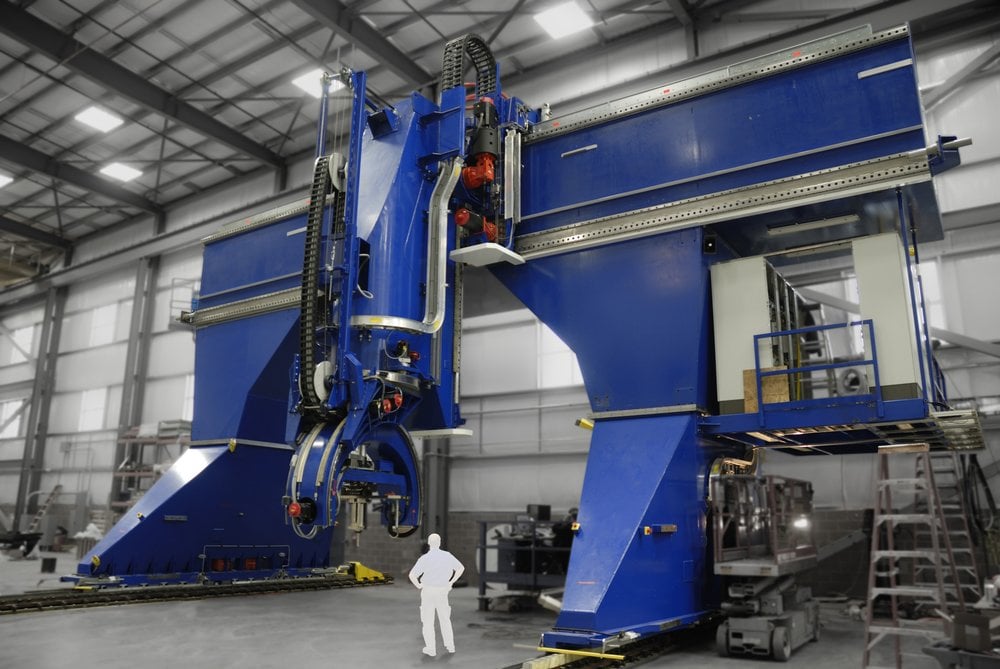
Electroimpact est une entreprise d’ingénierie dont la mission est d'être le premier fournisseur d'équipement automatisé pour l'industrie aéronautique dans le monde entier. Electroimpact a mis au point un système automatique de placement de fibres (AFP), une technologie qui permet de couper et d'ajouter des bandes de fibre de carbone dans les tolérances de placement du client à des vitesses jusqu'à 50 m/s via des rampes, le tout sur des surfaces complexes. Toutes les déposes peuvent être réalisées entièrement dans les deux directions et avec une régulation de la vitesse sans effet sur la précision de la coupe. Avec une équipe hautement qualifiée et pluridisciplinaire, Electroimpact est devenu le plus grand intégrateur de lignes d'assemblage d'avions dans le monde. La clientèle comprend des fabricants d'avions commerciaux et militaires à travers le monde.
Le client le plus récent est un grand fabricant américain de composants aéronautiques. Ils fabriquent , entre autres, des fuselages, des éléments sous voilure et des ailes. Le siège de la société se trouve à Wichita, au Kansas, la capitale mondiale de l’aéronautique, avec des implantations supplémentaires à Tulsa et McAlester, en Oklahoma, Prestwick, en Écosse, et Samlesbury, en Angleterre.
La machine automatisée de placement de fibres (AFP) est conçue pour la fabrication de grandes structures d'aéronefs commerciaux. Elle offre un fonctionnement modulaire avec une tête de dépose avec changement automatique en 30 secondes. Afin de fabriquer ces grandes pièces aérospatiales, le mouvement de la tête de placement de fibres est réalisé via 3 axes X, Y et Z. Elle pèse 175 tonnes et sa capacité d’accélération est de 0,2 g. Les bandes de fibre de carbone imprégnées sont posées sur des formes multiples (1 / 8 pouce sur les surfaces non planes, 1 / 4 pouce ou 1/2 pouce sur des surfaces planes). Il s'agit d'un processus sans torsion, ni rupture de jonction, et ce, dans un fonctionnement entièrement bi-directionnel.
Les axes linéaires X, Y, Z et les axes de rotation sont synchronisés pour que la fibre de carbone suive le contour de la pièce en cours de fabrication. Celles-ci sont placées sur un moule qui est usiné selon la forme de la pièce finale. La fibre de carbone doit être appliquée par le biais de différentes couches et avec des directions différentes pour optimiser la robustesse de la pièce finale.
Les courses peuvent varier en X de 2m jusqu’à 30m.
Un système de contrôle avancé
Cette machine impliquait une nouvelle conception du système de découpe et une optimisation du système d'alimentation et dépose de la fibre. La tolérance de placement de coupe est de +/-0.050 pouce (ou au total le chiffre k de 0,10 pouce total [k]), le temps disponible est :
T = k x 60 / 50 = 0,003 secondes.
En d'autres termes, à 50m par minute, 1 milliseconde équivaut à 0,033 pouces de déplacement. Cela montre que la précision et la répétabilité du système de découpe doit être meilleure que ce qu’offre une commande numérique classique (vitesse de balayage de 4 à 8 ms). La répétabilité individuelle des composants (par exemple, actionneurs, vannes, etc.) doit être inférieure à une milliseconde ou mieux. En outre, le système qui signale l’accomplissement d'une coupe doit avoir une résolution inférieure à la milliseconde.
Electroimpact mis au point un mécanisme de coupe à grande vitesse. L’opération est réalisée en moins d’une milliseconde. Ce système a également très peu de variabilité, permettant un placement précis et répétable de la fibre. Les facteurs, qui vont affecter le temps d’exécution, seront le programme, la vitesse de la sortie, l'actionnement de l’électrovanne, la circulation de l'air et l'inertie des mécanismes d'actionnement, etc. Chacun de ces facteurs génère un retard dans l'exécution d'une coupe. Si le retard est prévisible et reproductible, la programmation du déclenchement de la coupe peut le compenser. Ces décalages doivent également être réduits au minimum si possible. Grâce au développement fait par Electroimpact et des essais intensifs, la variabilité du décalage a été réduite en dessous de 1 milliseconde, ce qui la rend très précise à des vitesses élevées.
Des contrôleurs classiques, tels que les automates ou les CNC, fonctionnent généralement avec des temps de cycle généralement de l’ordre de quelques millisecondes. Les sorties sont actionnées une fois par cycle, ce qui limite la résolution temporelle de la durée de balayage. Avec un délai de 1 milliseconde résultant dans une erreur de placement de 0,033 pouce à une vitesse de 50 mètre par minute, l'introduction d'une erreur de seulement 1 milliseconde serait inacceptable pour la coupe grande vitesse à la volée ou la dépose de fibre.
Electroimpact a choisi d'utiliser le « customer board » de Fanuc, un système qui permet à Electroimpact d'interpoler le découpage et la dépose dans le profil de mouvement au niveau de commande de vitesse de la CNC. Il s'agit de la première mise en œuvre de ce type en dehors du Japon et Electroimpact a travaillé en étroite collaboration avec Fanuc pour implémenter des fonctionnalités spécifiquement pour cette application. La commande (de l’ordre de la milliseconde) a inclus des temporisations permettant une synchronisation.
Les clients d’Electroimpact ont reconnu la nécessité d'un logiciel de programmation devant être fournis par une société reconnue par l'industrie dans le cadre d'une série standardisée, mise à jour régulièrement et entretenue. Depuis plus de 2 ans, Electroimpact est partenaire non exclusif avec CGTech pour développer un logiciel de programmation appelé le " Vericut Composite programming and simulation Suite".
La solution unique de REDEX ANDANTEX
Pour Electroimpact, REDEX ANDANTEX a fait face aux contraintes les plus élevées : la combinaison de vitesses élevées, du masse énorme et de mouvements très complexes avec des accélérations fréquentes, et ce, dans toutes les directions.
«Nous avons choisi REDEX ANDANTEX parce que personne d'autre ne fait des entraînement de cette précision dans cette plage de couple et d’accélération», explique Peter Vogeli, ingénieur en chef, Electroimpact, Inc
Le premier problème est d'éliminer le jeu. Le système d'entraînement pignon crémaillère est composé de 2 servo-réducteurs planétaires montés en parallèle et couplés électriquement. Ce système de pré charge élimine le jeu et permet au système d'asservissement de contrôler précisément position de l'axe.
La deuxième question est d'assurer la plus grande rigidité pour offrir une parfaite répétabilité, malgré les accélérations fréquentes. La rigidité extrême est fournie dans toutes les directions par un arbre de sortie avec un pignon intégré soutenu par des roulements de sortie renforcé. Cette conception unique offre des caractéristiques de rigidité torsionnelle parmi les meilleurs sur le marché, mais surtout, il offre une rigidité exceptionnelle sur les autres dimensions (radiale et axiale), ce qui offre souvent une capacité d'accélération ou de déplacement de masse doublée par rapport aux autres solutions. Cette conception exclusive combine des roulements de sortie fortement renforcés avec des pignons qui partie intégrante de l'arbre de sortie (acier trempée et rectifiée du même diamètre que l'arbre). Le diamètre de pignon est optimisé pour assurer le meilleur rapport entre le couple transmis et la rigidité. Ils bénéficient ainsi du meilleur rapport possible entre couple transmissible et rigidité au niveau de la crémaillère. Le palier de sortie est constitué de deux roulements à rouleau à contact oblique, précontraints et largement surdimensionnés. Cette construction permet au palier de supporter le pignon au plus près de l’effort, car seule l’épaisseur de l’écrou de serrage sépare le pignon du roulement de sortie. Cette conception particulière permet une réduction considérable de la flexion radiale, qui est la cause de 60% de la déformation globale, mais est rarement traitée de façon satisfaisante par d'autres systèmes.
Andantex US est le fournisseur unique pour les entraînements mécaniques
Les équipements ANDANTEX sont installés sur tous les axes de sorte à créer une responsabilité unique pour le comportement globale de la machine.
L'axe de rotation entraîne l'outil sur lequel la fibre de carbone est posée. Cet outil se compose généralement d'invar qui est un type d'acier avec un taux de dilatation thermique très faible. Ceci est important, car une fois que la pièce est fabriquée; l'ensemble est placé dans un autoclave et cuit pour être sûr de la fibre de carbone imprégnées se fixe dans son état final. Après que l'outil est retiré et le reste est entièrement réalisée en fibre de carbone.
4 KRP Taille 6 permettent cette rotation précise.
- Vitesse Max. de rotation: 81 tr / min
- Vitesse de rotation nominale: 25 tr / min
- Couple maxi : 6600 Nm
- Configuration: 2 DUALDRIVE / axe
L'axe des X est équipé de 4 réducteurs planétaires KRP Taille 6, la plus grande taille disponible dans la gamme REDEX ANDANTEX. Ils sont mis en place sur deux racks de 35 m de long.
- Vitesse linéaire = 51 m / min.
- Masse = 160 tonnes
- Accélération = 0,2 g
- Configuration: 2 DUALDRIVE / axe
L’axe Y est équipée avec de 2 réducteurs SRP dans une configuration TWINDRIVE. Ils sont montés sur rack de 5,5 m
- Vitesse linéaire = 53m/min.
- Masse = 14,3 tonnes
- Accélération = 0,2 g
- Configuration: TWINDRIVE / axe
Pour le retour de position sur les codeurs secondaires des axe X et axe Y, Electroimpact utilise également le PDP de REDEX ANDANTEX pour entraîner l'encodeur directement de la crémaillère, sans jeu. Cette solution est la première génération de réducteur à pré charge réalisé par un double pignon. Il offre une haute précision pour les applications pignon crémaillère. Le PDP est constitué de 2 pignons WMH. Ils sont reliés entre eux par un système breveté de précontrainte pour éliminer le jeu sur la crémaillère. Le concept novateur PDP fournit la rétroaction d'encodeur directement à partir de la crémaillère assurant une précision de positionnement et une répétabilité élevées avec un budget très compétitif.
- Axe X Module 10 = 500 mm
- Axe Y Module 5 = 250 mm
Enfin, ANDANTEX a fourni à Electroimpact des modules 10 et 5 hélicoïdaux, des crémaillères en acier trempé et rectifié pour les axes X et Y avec des pignons lubrifiés par de la mousse de polyuréthane pour lubrifier automatiquement la crémaillère. Celle-ci est fournies en sections de 1 mètre (ou 2). Cela signifie qu’ANDANTEX US a fourni tous les éléments mécaniques entre le servo-moteur et l'axe.
"A la fin, la précision du placement est égale à la précision de coupe (+ / - 0,050") à la vitesse maximale. Les axes entraînés par les réducteurs REDEX ANDANTEX devaient être plus précis que cette valeur étant donné qu'ils travaillent tous ensemble pour être capable de réaliser des formes complexes. On peut estimer une précision à 1 / 10 sur les axes X, Y et Z ou une précision de placement de + / - 0,0125 mm, explique Dave REGIEC, chef de projet de ANDANTEX.