Tests de moteurs électriques pour applications automobiles
Pour ses bancs d’essais utilisés à la fois en laboratoire et en production, Unus International a choisi la solution clés en main de MEROBEL.
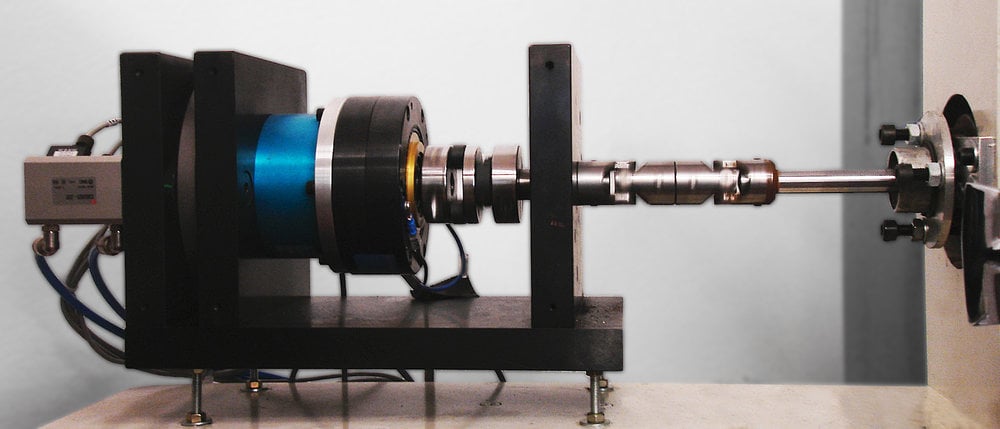
Fondée à Padoue dans les années soixante-dix et établie depuis 1995 à Rival di Pianiga (Venise), la société UNUS emploie actuellement environ 60 personnes et produit plus de deux millions de pièces par an.
La production comprend les principaux moteurs et motoréducteurs destinés aux applications automobiles suivantes :
- Glaces, toits ouvrants, stores électriques, mécanismes divers
- Réglages / déplacements de sièges
- Réglage volant
- Mise en œuvre de boîtes de vitesses automatiques.
La gamme complète de produits comporte également des équipements motorisés supplémentaires pour divers secteurs industriels tels que, par exemple, la gestion de portes coulissantes, de levée de barrières et autres solutions d’automatisation en général.
Les Ingénieurs d’UNUS International développent leurs nouveaux projets en se mettant au service du client.
Les compétences techniques et la flexibilité constituent les principales valeurs de l’entreprise, ce qui réduit le temps de conception, prototypage et fabrication des premiers échantillonnages des nouveaux produits. Cette organisation nous permet de répondre rapidement à un large éventail de besoins du marché, en assumant la gestion complète des questions de délais de mise sur le marché.
« Notre mission consiste à proposer des produits parfaitement adaptés aux besoins du client, pour lequel le niveau technique et la qualité sont des questions essentielles, explique l’ingénieur Massimo Melato, directeur général d’Unus International. Le point de départ, ce sont nos politiques qualité et R&D en évolution permanente, mais aussi notre organisation en matière de conception, de production et d’activités commerciales en général, systématiquement vouée à l’amélioration de la satisfaction du client ».
« Nos excellents résultats, réalisés sur les marchés intérieur et étrangers grâce à des produits à fort contenu technologique, confirment que nous allons dans la bonne direction, alors que nous améliorons en permanence aussi bien notre compétitivité que notre qualité. Rappelons que les moteurs et motoréducteurs UNUS™ sont utilisés en équipement d’origine par les principaux constructeurs automobiles allemands ainsi que par les plus importants fabricants de systèmes d’automatisation ».
L’importance stratégique des essais
Les raisons de ce succès, au-delà des compétences technologiques de l’entreprise, sont en partie imputables à la fiabilité et à la qualité élevées de la production.
UNUS International figure parmi les 100 entreprises italiennes les plus performantes selon Eurispes, l’institut italien de données économiques. Pour garantir un tel niveau d’excellence, les essais produits (non seulement en cours de production, mais aussi au laboratoire en phase de conception) revêtent une importance stratégique absolue.
Des bancs d’essais spécifiques ont été spécialement installés pour tester 100% des moteurs destinés à l’industrie automobile. « Il s’agit principalement de glaces électriques, de déplacement de sièges, d’ouverture de toit, de réglage de direction et de divers mouvements de translation, précise l’ingénieur Massimo Melato. Nous développons actuellement un moteur conçu pour faire fonctionner un compresseur de suspension pneumatique de voiture ».
Les bancs d’essais associés n’ont pas été conçus pour une application client particulière. UNUS a rassemblé toutes les directives d’un grand nombre de constructeurs automobiles et développé des bancs d’essais polyvalents susceptibles de répondre à ces cahiers des charges spécifiques.
« Les solutions habituelles du marché visent à satisfaire le plus large éventail possible d’applications, explique l’ingénieur Massimo Melato. Cela dit, elles ne répondent pas pleinement aux besoins et tâches que nous voulons leur assigner. Etant donné que nous avons construit nos bancs d’essai en interne et développé nous-mêmes le logiciel de commande, nos solutions ciblent nos exigences ou, plutôt, les véritables besoins de nos clients ».
Dans le processus de fabrication, chaque moteur est testé, aussi bien les principaux paramètres de fonctionnement que le niveau sonore. « Pour procéder à ces essais, nous disposons actuellement de 4 cabines de tests équipées de freins MEROBEL, souligne l’ingénieur Massimo Melato. Le cycle d’essai dure 5 ou 10 secondes en fonction du type de moteur, pour une production journalière d’environ 8000 pièces ».
Les autres bancs d’essais sont installés au laboratoire (où 5 systèmes sont équipés de freins MEROBEL), afin de contrôler la fiabilité des moteurs et motoréducteurs électriques au moyen d’essais de longévité et de fatigue.
Pour de tels processus, la durée des cycles d’essais est beaucoup plus longue. Certains tests d’endurance, avec des cycles longs et une simulation du vieillissement par le biais de cycles thermiques en chambre climatique, peuvent prendre jusqu’à 60 jours.
Il existe par conséquent deux applications très différentes l’une de l’autre.
« Au laboratoire, les essais sont principalement dévolus à la simulation du cycle de fonctionnement des moteurs sous différentes charges (c’est-à-dire avec différents niveaux de couple) et dans des environnements variés (dont chocs thermiques, gamme de température de - 40°C à + 90°C et différentes valeurs d’humidité relative), ce pour toute une série de cycles ou jusqu’à la fin du cycle de vie du moteur, confie l’ingénieur Massimo Melato. Ensuite, nous mettons en oeuvre un cycle d’essai bien défini, en fonction des spécifications client ». Pendant toute la durée des essais du moteur, chaque paramètre individuel est constamment surveillé et enregistré (consommation de courant, vitesse, couple et température).
Tout moteur ne satisfaisant pas aux qualifications requises ou présentant un défaut quelconque (surchauffe, usure prématurée des balais ou panne d’un composant par exemple) est prélevé aux fins d’analyse des causes du dysfonctionnement et de remise en état. Une fois la modification effectuée, le moteur est à nouveau soumis à un essai complet, de façon à répondre à la qualité requise.
Notre seul et unique objectif, c’est que le moteur satisfasse en tous points au cahier des charges du client et, une fois passé en fabrication, produise « zéro déchet ».
La même procédure s’applique également une fois par an aux essais des produits afin de vérifier l’absence de dérive dans le temps.
Des freins EMP robustes et fiables, des contrôleurs de boucle faciles à utiliser
Pour simuler sur banc la charge variable que le moteur est censé rencontrer au cours de son durée de vie, Unus a choisi une solution complète basée sur des composants MEROBEL, avec l’aide d’ANDANTEX SpA, filiale locale de l’entreprise.
Les composants retenus furent des freins EMP (type FAT120), un capteur de couple (type TRS50), et un contrôleur de boucle fermée (type DGT300).
« ANDANTEX nous a conseillés sur les freins MEROBEL à utiliser dans cette application ainsi que sur l’unité de contrôle et les différents paramètres à régler selon notre cahier des charges, explique l’ingénieur Massimo Melato. Un vrai partenariat a été établi avec ANDANTEX à propos de la fourniture des freins tout au long du développement de l’application. En particulier, le partage d’expérience avec nos concepteurs de logiciels personnalisés a joué un rôle déterminant pour mettre les systèmes d’essais finaux en parfaite adéquation avec nos besoins ».
La gamme étendue de solutions proposées par MEROBEL comprend des actionneurs de haute technologie tels que les freins et embrayages EMP, des contrôleurs numériques, des capteurs et des transducteurs. Grâce au savoir-faire particulier qu’elle a acquis, l’entreprise est en mesure de proposer des solutions optimales pour n’importe quel système d’application de couple, en fonction des contraintes spécifiques.
La gamme de freins et d’embrayage EMP (ElectroMagnetic Particles – particules électromagnétiques) de MEROBEL comporte deux rotors concentriques, l’un extérieur et l’autre intérieur, séparés par un espace qui abrite les particules magnétiques.
La variation du champ magnétique provoque la fluidité variable des particules magnétiques, induisant un accouplement mécanique homogène et variable entre les deux rotors (couple variable).
Cette technologie spécifique garantit un couple constant, reproductible et indépendant de la vitesse de rotation, facilement réglable par faible niveau de courant continu.
Parmi les principales caractéristiques des freins et embrayages EMP de MEROBEL figurent la proportionnalité entre le courant appliqué et le couple fourni, l’indépendance entre le couple et la vitesse, le fonctionnement bidirectionnel sans bruit et avec un faible niveau d’usure.
Par ailleurs, les freins et embrayages EMP de MEROBEL offrent un temps de réponse élevé (10 à 50 millisecondes), un comportement linéaire, une gestion à distance particulièrement aisée ; ils s’intègrent dans tous types de systèmes d’essais tout en se caractérisant par un entretien réduit et une faible consommation électrique.
« Nous sommes pleinement satisfaits des produits MEROBEL et du soutien d’ANDANTEX, conclut l’ingénieur Massimo Melato. Nous avons d’abord installé les freins MEROBEL sur les bancs d’essais de production. Et malgré les contraintes passablement plus élevées, nous avons désormais étendu avec succès l’utilisation de ces freins aux bancs d’essais du laboratoire ».